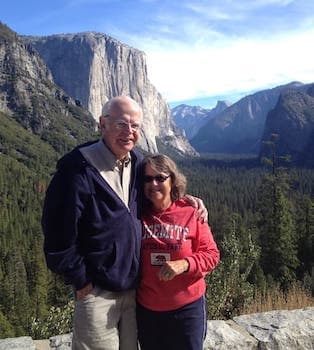
Curated with aloha by
Ted Mooney, P.E. RET
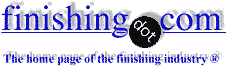
The authoritative public forum
for Metal Finishing 1989-2025
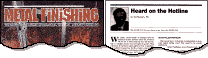
-----
6061-T6 aluminum corrosion protection
Q. What would be the best solution to provide corrosion protection for 6061-T6 aluminum sheets without the use of a topcoat? Such as zinc chromate, zinc phosphate, zinc oxide, or a plain metal primer. Also, would cold galvanizing compound Cold Galvanizing Compound / Zinc Rich Paint be appropriate or recommended as corrosion protection on a 6061 aluminum substrate instead of a primer?
Thanks,
- St. Charles, Missouri, USA
2002
A. Chromate conversion coating, as described in MIL-DTL-5541 [⇦ this spec on DLA], would probably be the best idea.
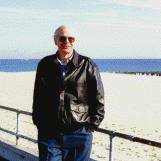
Ted Mooney, P.E.
Striving to live Aloha
finishing.com - Pine Beach, New Jersey
2002
? Brian,
Please be a little more specific..as to the environment your parts are in, and what type of corrosion protection you are looking for. That makes it easier for us to recommend a coating that will suit your needs.
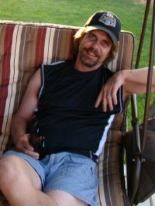
Marc Green
anodizer - Boise, Idaho
2002
Q. This application is for the interior of a fuselage and wings of an aircraft that is to be primarily constructed of .020 inch 6061-T6 aluminum sheets.
Thanks,
- St. Charles, Missouri, USA
2002
A. Hi Brian. I'd probably stick with my first answer then. Cold galvanizing could be a very bad idea because of galvanic corrosion.
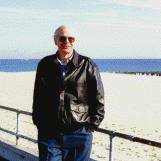
Ted Mooney, P.E.
Striving to live Aloha
finishing.com - Pine Beach, New Jersey
2002
Q. I am asking a semi-related question. I am a mechanical engineer, so my knowledge on the subject is at a minimum. I have some duct work that has 6061 aluminum extrusions extending from the supply fan discharge downstream. I have abnormal corrosion characteristics with the aluminum corroding and "flaking" apart. I am looking to coat this corroding aluminum so that it will prevent further corrosion. I then plan on covering these sealed extrusions with stainless steel lap strips and corner angles. Any suggestions for a coating?
Nick Culley- Richmond, Virginia, USA
January 23, 2013
Q. I have a project of aluminum 6061-T6 gangway for marine structure and I would like to know what type of finishing I can use to have a clean, smooth and corrosion resistent surface after welding. I have tried light sand blasting but after putting in accelerated corrosion test, there was severe corrosion on the surface. Please help.
Omid A- UAE
February 10, 2015
A. Hi Omid. Bare aluminum is not corrosion resistant. You should probably anodize it. Good luck.
Regards,
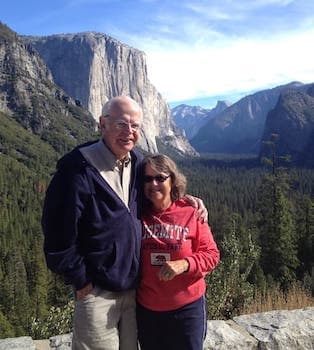
Ted Mooney, P.E. RET
Striving to live Aloha
finishing.com - Pine Beach, New Jersey
October 2019
Q. What is the best medium to test the corrosion behaviour of Al6061? Is 3.5% NaCl good to go?
M. Ali Khan- Australia
October 18, 2019
A. Hi Ali. Your question is rather vague. All accelerated tests are unrepresentative of actual atmospheric exposure, but if you use a standard one like ASTM B117, then at least you'll have some published feedback regarding how representative it is or isn't. Simply dipping in 3.5% NaCl doesn't seem like it will tell you much about whatever finish you are planning to apply to the aluminum. Good luck.
Regards,
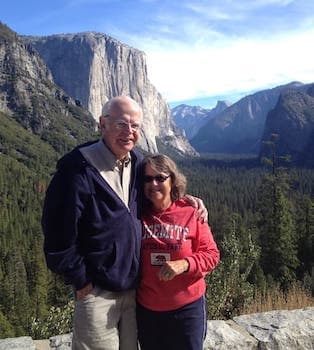
Ted Mooney, P.E. RET
Striving to live Aloha
finishing.com - Pine Beach, New Jersey
October 2019
Q. Hi Ted. Thanks for your feedback. Here is some more details on what I am doing. I want to compare the effects of different heat treatments on the corrosion of Al6061 alloy. I agree with you that following some standard is good like B117. But this standard is salt spray testing which I think is more representative of atmospheric corrosion than immersion (seawater) corrosion in which I am interested in. In literature people have used 3.5% NaCl for corrosion (immersion) testing of Al6061. So, is 3.5% NaCl is a good medium to test the corrosion behaviour of different heat treated Al alloys with respective to their application in seawater environment?
Ali Khan- Melbourne Australia
October 26, 2019
A. Hi again. Well, yes, the ocean is about 3.5% salt, so if you're attempting to approximate seawater, that's the right number.
Regards,
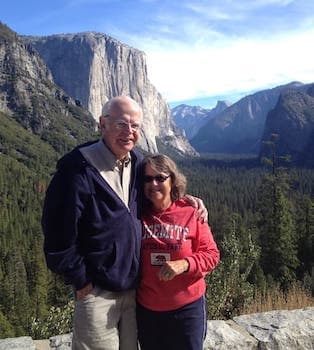
Ted Mooney, P.E. RET
Striving to live Aloha
finishing.com - Pine Beach, New Jersey
October 2019
A. Hi Ali,
Years ago we used to go down to the local coast with 5 gallon drums and fill them with sea water for our corrosion tests (bit of a pain in the proverbial, as the coast was about a half hour away). Later, we used an artificial solution, containing about 12 different salts, to closely emulate sea water. Finally, we went away from sea water testing and adopted standard testing in accordance with ASTM B117.
Now, as you are trying to compare how different heat treatment states react to corrosive atmospheres, I'd suggest that as long as the salt concentration is consistent for all tests, you could use 3.5%, 5% or even 8%, just make sure the conditions of test are not a variable you need to consider, otherwise interpretation of results will be difficult.
Whichever test conditions you use, I would be very interested to hear what you find out :)
Aerospace - Yeovil, Somerset, UK
October 28, 2019
Q, A, or Comment on THIS thread -or- Start a NEW Thread