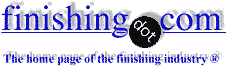
-----
Electropolishing of aluminum: concentration and chemical make up
Quickstart:
Electropolishing is a process resembling electroplating in reverse. The components are immersed in an acidic solution, made the anode, and (hopefully) their small burrs and asperities dissolve into the acid, smoothing the finish. Many different metals can be electropolished, with stainless steel being the most common.
Electropolishing may sometimes be more economical than mechanical polishing, but the compelling feature is the nature of the finish. Mechanical polishing always creates a finish resembling (under magnification) a farmer's plowed field; the scale of the furrows and clods can be reduced but always remains. Electropolished surfaces resemble (under magnification) gentle ocean swells with minimal tooth, no clods to dislodge, and no hiding places.
Q. Hello everyone!
I'm running a CNC machine shop and I've been working with anodizers for 2 decades. I've been also working for an anodizing company at some point. I've put together my own line. I've always had to bright dip my parts, but in-house I'd rather go for electropolishing. Can someone tell me the make up of the bath? I know it is H3PO4, but what concentration and so on? If someone is familiar with the process, I'm very interested in learning more about the process.
Thank you :)
- Geneva switzerland
March 27, 2021
9th Edition, Vol. 5
"Surface Cleaning, Finishing & Coating"
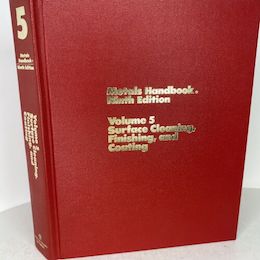
on eBay or Amazon
or AbeBooks
(affil link)
A. Hi Fab. Read on for one common formulation. And please search the site for 'electropolish aluminum' as we have many threads on the subject with some very detailed & insightful replies to help you get started. In addition to the often-cited Wernick, Pinner & Sheasby, ASM Metals Handbook Vol. 5 has great coverage of aluminum electropolishing. Good luck.
Luck & Regards,
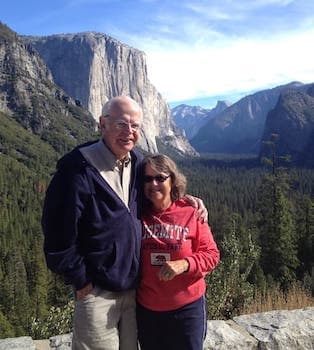
Ted Mooney, P.E. RET
Striving to live Aloha
finishing.com - Pine Beach, New Jersey
A. I hate to burst your bubble but I know of no electro-polish that gives the same results as "Brite Dipping". It is an age-old problem and if someone out there has an electropolish that can REALLY compete with "Brite Dip" I need to know ASAP.
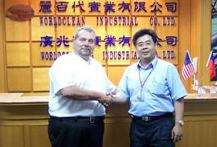
Drew Nosti, CEF
Anodize USA

Ladson, South Carolina
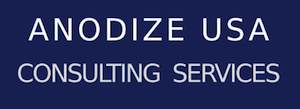
A. Hi Drew. Coincidentally, a similar question was asked on the same day on topic 51410, which resurfaced Harry Parkes' outstanding response explaining why the move from brite dipping to electropolishing before anodizing is often quite impractical from a production standpoint.
Luck & Regards,
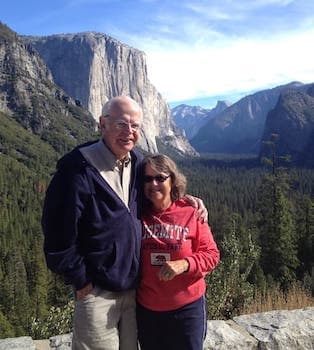
Ted Mooney, P.E. RET
Striving to live Aloha
finishing.com - Pine Beach, New Jersey
⇩ Related postings, oldest first ⇩
Q. I want to electropolish small Aluminium pieces 99.99% pure. I would like to grow porous alumina later. Can anybody help me about the electropolishing solution and parameters to use?
Thanks,
Technical University of Valencia - Alicante, Spain
2002
A. Hi Emilio. High purity aluminum is ideal for the electropolishing process. You'll find excellent detailed data about electropolishing aluminum in ⇦[this on eBay, AbeBooks, or Amazon affil links] , and you can simply read on here for direct answers to your question. But keep in mind that small pieces can have extremely high surface area so things may proceed a bit differently than you expect if you don't stay mindful of it. Powders may explode in metal finishing processes which are slow and well controlled on large pieces :-(
Luck & Regards,
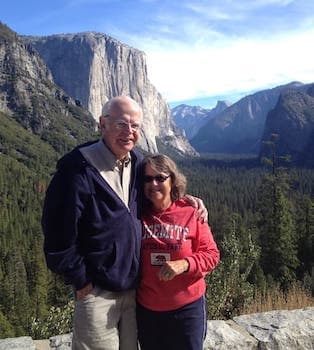
Ted Mooney, P.E. RET
Striving to live Aloha
finishing.com - Pine Beach, New Jersey
April 2021
Q. What is the best solution for electropolish of series 7000 aluminum.
Mohammad Jiriayee- Tehran, Iran
2002
A. The 7000 alloys are not recommended for electropolishing applications, since is a high alloyed aluminum and may be pitted very easily.
Gabriel SchonwaldBnei Berak, Israel
2002
Q. I am trying to set up a small 20 liter bath for electropolishing aluminium. I have had no success with the Brytal process; can you please suggest chemical formulation, temperature, current and voltage for a SMALL hobby bath which can be run in a garage as a hobby. I want to electropolish alloy parts for my car wings on my car and stainless steel parts.
I have been looking around in WA but no one does electropolishing for alloys; the others don't want to talk to me as it is a hobby; for now your help will be greatly appreciated.
Best regards,
- Souther River, Western Australia
2002
A. Hi Michael. Per the Canning Handbook [on
eBay,
Amazon,
AbeBooks affil links], Brytal is a registered trade mark of the British Aluminum Co. and consists of 150 g/l of sodium carbonate
⇦ on
eBay or
Amazon]
and 115 g/l of trisodium phosphate
⇦ on
eBay
or
Amazon [affil links]
. It is operated at 12-15 V, 5-10 A/dm2, 85-90 °C, for 5 to 20 minutes. See the handbook for further details.
You'll see that many readers discourage chemical processing by hobbyists due to safety issues and possible environmental damage.
As you say, some processes work only on some alloys, and Brytal is for 99.8% super purity aluminum -- do you know what alloys you'll be dealing with? Are you restoring previously electropolished aluminum or trying to brighten something that was dull, painted, or plated? The safe way is to mechanically polish and buff the aluminum.
Electropolishing stainless steel is a completely different process, and you won't be able to use your tanks and solutions on the stainless parts. Good luck.
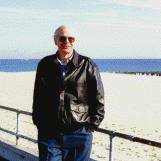
Ted Mooney, P.E.
Striving to live Aloha
finishing.com - Pine Beach, New Jersey
Q. Dear Ted,
Thanks for taking the time to answer my question.
I have been trying to use H2SO4 and H3PO4 for the last 2 weeks to try to come up with a workable solution. I have even built my own DC rectifier with Pi filter to make sure I got true DC; the alloy I am using is 5038 5005 6006 and 5083 these alloys are mostly high tensile alloy used for boat building except 5005. I am making wings, skirts and dash parts for my Nissan 280zx. I like to make unique things, polishing is okay but it takes forever, the finish produced still has cutting marks and does not last in our environment here.
I was hoping to electropolish the alloy parts and bright anodise them to make them last. We are a sign company, the car will go to a car show with other alloy decals we make.
Bkg: bio 45 years old have spent 8 years murdoch univ lab tech bioenvsci. wind erosion research. I have had some experience with chemicals.
I am also experienced with a phosphoric/citric acid solution. I want to clean off the weld smut from stainless welding; at the moment the trades are using hydrofluoric/phosphoric paste (very dangerous); have had good success but cleaned weld is matte I was hoping for a bright finish. The reaction should give a bright finish; your help in these areas will be greatly appreciated.
P.S. hydrofluoric/phosphoric paste is being banned here.
Best regards,
- Australia
Courtesy Wikipedia. For full credits see https://en.wikipedia.org/wiki/File:HF_burned_hands.jpg
Treatment &
Finishing of
Aluminium and
Its Alloys"
by Wernick, Pinner
& Sheasby
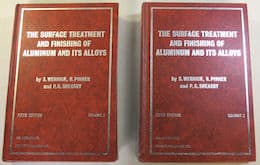
on eBay or Amazon
or AbeBooks
(affil link)
A. Hello again. Please remember that there are 100 readers for every poster. While your c.v. is impressive, the internet is a giant one-room schoolhouse where people with no chemical training "overhear" stuff and may try it if not warned against it. So we frequently remind readers that hazardous chemicals are for those who have received chemical & haz-mat training, and working in proper facilities with proper personal protection equipment.
Hydrofluoric acid is truly nasty stuff, so it's easy to understand the paste being banned as it can accidentally be left on surfaces which might be touched.
According to an old but detailed paper by A.W. Brace, "European Bright Anodising Practice", published in the 1959 AES Proceedings, the phosphoric-sulfuric bath should be 75-80 percent (vol) phosphoric acid and 20-25 percent (vol) sulfuric acid and, ideally, with 1/2-1 percent nitric acid--but he mentions other formulations.
You may know this, but other readers may not: Wernick, Pinner & Sheasby ⇨
is the exhaustive authority on finishing of aluminum. Good luck.
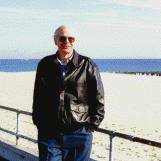
Ted Mooney, P.E.
Striving to live Aloha
finishing.com - Pine Beach, New Jersey
A. Mike,
EP of aluminum can be a tricky process. The alloys you mentioned are all pretty low in Si, which does make them easier to polish. Most EP tanks are heated (approx. 165 °F), and agitated. You have to make sure that your agitation is good/even, or your parts will be pitted. It's a tricky process for a novice. The other thing you'll want to look at is the amount of current you are putting into your parts, and the fixturing you are using to hold them. In an ideal situation, you'll want to use copper-tipped Ti racks (so no current robbing takes place). Have you considered, perhaps, sending these parts out.
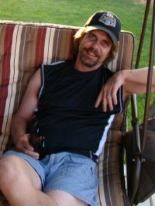
Marc Green
anodizer - Boise, Idaho
Phosphorus contamination of aluminum after electropolishing
Q. I have a slight problem with my electropolishing method. I'm electropolishing 316 SS and my goal is to have less than 1% phosphorus contamination on the surface afterward. I have tried everything, two HOT DI water rinses after electropolishing, then single passivation followed by another two HOT DI water rinses. The PH values in the rinse baths are kept above 3-4 ph. In addition, I have tried Ultrasonic bath at the very end, but to my surprise I have worst results with ultrasonic than without. As for the test method I'm using AES to get the surface composition. Please let me know what you think.
Thanks,
- Lawrenceville, Georgia, USA
2003
A. The problem is viscous EP solution drying on the part after removing from the hot EP solution. Try 1) Lowering the EP solution temperature, 2) A light DI spray rinsing while withdrawing the part above the EP tank, to both rinse & cool the part, and 3) Faster transfer to the rinse tanks. Also, warm rinses are better than hot to avoid drying of the liquid film when transferring between tanks. Use air agitation, and let the rinsewater pH go below 3 (add a little nitric acid if necessary) to dissolve phosphates, except for the final, post-passivation rinse, which should be DI. Are you analyzing and changing your DI rinses? Suggest counterflowing from the final to the initial.
See Mr. Mooney's "20 Ways to Cut Water Usage in Plating Shops" for more rinsing suggestions at www.finishing.com/library/mooney/20ways.html
- Goleta, California

Rest in peace, Ken. Thank you for your hard work which the finishing world, and we at finishing.com, continue to benefit from.
2003
A. Dead spray rinse well
Rinse/Rinse
30-60 sec 10-20 nitric acid
Rinse/Rinse
Hot D.I. dry
If still a problem use a citric acid passivate after the nitric dip and rinses.
- Minneapolis, Minnesota
Q. Hello Ken,
You have suggested lowering the EP and DI rinse temperatures. Right now my EP is set at 175 °F and DI at 150 °F. Should I go lower than that? If yes what do you recommend?
- Lawrenceville, Georgia, USA
2003
A. The EP temperature seems quite high. A phosphating reaction may possibly be occurring after the current is turned off. The EP solutions developed by Charles Faust at Battelle generally have working ranges of 80-175 °F. At the lower end, the solution is highly viscous (excessive drag-out) and you cannot evaporate excess water (as from rinsing). Temperatures of 140-160 °F are common. I suggest 120 °F for all rinses except the final DI, which can be kept at 150 °F for better drying. The sulfuric acid component of the EP rinses more readily than does the phosphoric, and you don't want to bake on any neutralized phosphoric acid (phosphate). Do not allow any liquid residue on the surface to dry while transferring parts between tanks. A longer time in the passivation solution (nitric?) should also help.
Ken Vlach [deceased]- Goleta, California

Rest in peace, Ken. Thank you for your hard work which the finishing world, and we at finishing.com, continue to benefit from.
Q. Ken,
Can you expand on the H2SO4 rising faster than the H3PO4 in EP solutions? I too have read Faust...like his papers.
- Minneapolis, Minnesota
2003
Q. Ken,
One more question. What is recommended for aging the EP solution? We are using brass bars currently. What is your recommendation?
Thanks,
- Lawrenceville, Georgia, USA
2003
and Chemical Polishing
of Metals in
Research and Industry"
by W.J. Tegart
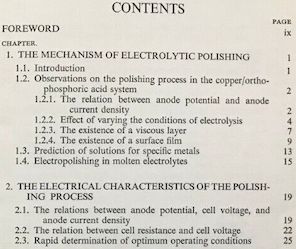
on eBay or Amazon
or AbeBooks
(affil link)
A. Arek,
I think aging is unnecessary and wasteful in terms of EP bath life and sludge generation. Not recommended for any proprietary product that I am aware of, and it isn't practiced by the large EP companies that produce tubing and fittings for the semiconductor industry. However, I have met EP'ers who believed it necessary to add some old solution when making up a new one. Anyone else with opinions or experiences on this subject?
Jon,
I can't find a reference re. my rinsing statement. Made a move several years ago, and may have lost or not unpacked some relevant papers. However, it makes sense both scientifically (sulfuric mixes very exothermically with water, phosphoric has a higher viscosity, phosphoric can form insoluble phosphates on ferrous metals) and empirically (Mr. Dyrdol found phosphorous residue). Also, have observed that a 60-20 sulfuric-phosphoric solution rinses better than a 65-15 (wt. percentages).
- Goleta, California

Rest in peace, Ken. Thank you for your hard work which the finishing world, and we at finishing.com, continue to benefit from.
A. Hi folks:
AES is an unusual way to get surface contamination from parts coming out of wet process... IPC-TM-640 calls out a standard test method for 7 most common anions found clinging to wet process parts.
I primarily suspect your rinse water, the cleaning process, the atmosphere quality above your tools, and your test method, rather than the EP process. Additionally, you never told us what is your offending surface concentration of Phos? 316SS comes with intrinsic phosphorous, maybe 0.05%W/W so it will never be "all gone." It may be trapped in the EPOx matrix so that the IPC test will detect no free, dissolvable, surface phosphorous, but AES will still pick it up because you blast the matrix away with the Auger sputter. The closer you get to the base material, the higher the concentration the AES will detect until it reads the intrinsic level.
The air above the process has some Phos in it. Just wave the part around in humid air and AES will pick that up. Every worker breaths out aerosols loaded with Phos.
The DI water may be bad, and can get contaminated just by exposing it to the atmosphere. Remember, 18.3 MOhm is true only inside the closed teflon pipes leading up to your process. You indicated the problem worsens in ultrasonic DI, which usually indicates bad DI. The recording head industry(a famous example was in Goleta!) are probably the best surface cleaners in the business. They use expensive DI, multiple staged rinse processes, staged ultrasonic DI with a variety of additives, alcohol or some other inert water-displacer at the end of process, and they blanket the whole line in inert gas. That's how you get truly clean parts. Your requirements may not be so strict.
Also, there is no "best" temperature. Sometimes I run my baths below the freezing point for special reasons.
Requires a hog power supply.
Regarding 316 SS & Sulfuric/Phosphoric baths, general rules are:
1. Lowering temperature helps
2. Lowering EP bath water concentration helps(the bath will pull humidity right out of the air)
3. Raising Current density helps.
Hope this helps. Maybe send out some parts to a test lab for the IPC anion test, and compare to your AES test.
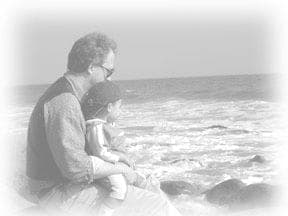
Dave Kinghorn
Chemical Engineer
SUNNYvale, California
Removing aluminium from an Electropolishing Bath
Q. Hello,
Is there any process/machine which could remove Aluminium particles
(contents) from an Aluminium Electro-Polishing Bath which are added to the electrolyte (solution) after certain time of usage of the same bath?
I look forward to your comments/suggestions.
Kunal
Anodizing Plant jobs - Rajkot, Gujarat, India
May 27, 2009
A. Hello,
I'm not sure whether or not it would work for a electropolishing bath, but for our anodizing bath we use a specially designed filter (I'm not sure whether or not I can mention the manufacturer, as they are not an advertiser of this site) that removes the vast majority of the dissolved aluminum. There may be similar technology available for electropolish solutions as well.
Good luck!
Compton, California, USA
Q. I am electropolishing aluminum for my college project. I used phosphoric acid 85% as electrolyte. After keeping the aluminum work piece in electrolyte when removed for rinsing in water a whitish layer is formed over it. I tried to removed to latter by rinsing with nitric acid diluted 20%. But the latter has increased. How to fully rinse the residue after keeping in electrolytic bath?
ALLEN VARUGHESE- coimbatore, India
January 27, 2015
A. Hi,
As this is a college project I expect that you know during the electropolishing of aluminium an oxide film continuously forms and dissolves. When you stop the current flow, the remaining oxide film dissolves into the electrolyte. The speed at which it dissolves depends on bath temperature, water content and when used, sulfuric acid concentration.
If you rinse quickly then some oxide may remain undissolved. It is necessary to remove this oxide in a suitable stripper. Nitric acid is not effective. I suggest that you try 5% w/v sodium hydroxide at room temperature few seconds. You can tell when the oxide has dissolved because the aluminium begins to gas. If the immersion is too long the sodium hydroxide will etch the surface.
Conversely, if the time between stopping polishing and rinsing is too long, the electropolishing solution will start to etch the aluminium. This etching can also result a white bloom. However, the defect is not a surface coating but the aluminium itself and cannot be removed by chemical treatment.
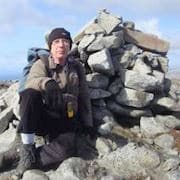
Harry Parkes
- Birmingham, UK
Q. I was wondering how electropolishers handle doing differing materials, do you need separate tanks for alloys and stainless, or is it easier to change chemicals using the same tank when the need arises?
Erik Berthelsen- Brisbane, Qld, Australia
November 12, 2012
A. Hi Erik.
There is no fixed answer to that question, but the basic proposition would be that open top rectangular tanks are ideal for processing, but poorly suited to long term storage. So, if the solution will not be used for a very long time, transfer it to drums or closed round tanks. But if you will be alternating frequently, just cover the tank when not in use and use another tank for processing.
Regards,
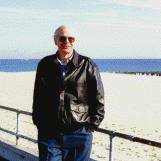
Ted Mooney, P.E.
Striving to live Aloha
finishing.com - Pine Beach, New Jersey
Q, A, or Comment on THIS thread -or- Start a NEW Thread