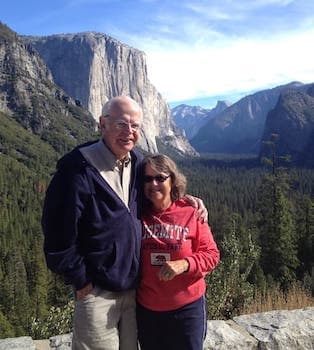
Curated with aloha by
Ted Mooney, P.E. RET
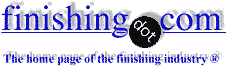
The authoritative public forum
for Metal Finishing 1989-2025
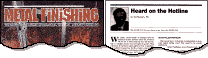
-----
Durable, attractive outdoor finishes for zinc die cast part?
Q. I am a product designer working with a zinc die cast part that has two steel pins press fit into it. The product will be placed outdoors and will require an attractive, chemical/corrosion and abrasion resistive surface. 1) What are the most durable finished available?
2) Can the two materials (zinc/steel) be plated simultaneously, i.e., after assembly? 3) What happens to zinc without any added finish? 4) Will any finish maintain its attractive luster for an extended period of time? (1-2 years)?
I would prefer a shiny silver finish but am open to other possibilities.
Thank you!
- Auburn, Pennsylvania, USA
2002
A. Zinc will quickly fade in lustre, get corrosion pits, and become covered with sticky white corrosion products. Untreated zinc is not an option. Unless, you say why not, we'd have to recommend copper-nickel-chrome plating, which is widely used and should easily last a couple of years if plated right.
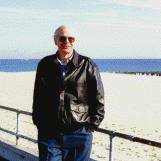
Ted Mooney, P.E.
Striving to live Aloha
finishing.com - Pine Beach, New Jersey
2002
A. Copper- Nickel -Chrome done properly will serve well. However, zinc die-casts tend to be porous, and zinc requires special treatment prior to plating. The nickel should be two layers-sulfur free semi-bright nickel followed by a bright nickel. The chromium must be porous chrome to enhance the corrosion protection. Automotive specs. address these issues.
There is also a company in the US hard anodizing zinc diecastings. The coating is a ceramic and extremely durable. (no corrosion on the front of tugboats for more than a year. (then removed- it could have gone much longer than a year.) The coating is called Iridize. it a matte finish but can be painted to produce a shiny durable finish.
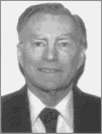
Don Baudrand
Consultant - Poulsbo, Washington
(Don is co-author of "Plating on Plastics" [on Amazon or AbeBooks affil links]
and "Plating ABS Plastics" [on Amazon or eBay or AbeBooks affil links])
2002
P.S.: I FORGOT TO ADDRESS THE STEEL IN CONTACT WITH ZINC. IT IS VERY DIFFICULT TO PLATE WITH THE STEEL COMPONENT PRESENT. IT CAN BE DONE WITH VERY SPECIAL PREPARATION STEPS. I THINK THAT THE ANODIZE (IRIDIZE) PROCESS WOULD NOT WORK WITH STEEL.
Q. I'm investigating finishing operations for diecast ZAMAK 3 & ZAMAK 5 parts
The decorative coating on the part will result in 2 different finish options with controlled CIELAB color values & gloss values
The coating will also have performance requirements listed below
UV Resistance: ASTM G155 980 hours
Corrosion Resistance: ASTM B117 240 hours
Temperature & Humidity Range: -40 to 70 °C, 0-95%RH
Thickness control : Not important
Adhesion : Cross-cut Level 4B
Scratch resistance : 3H @ 1000g
Currently the processes I'm interested in are
ZAMAK/Cu/Ni/Cr/Primer/Paint
ZAMAK/Chromate conversion (clear)/Primer/Paint
ZAMAK/Chromate conversion (clear)/Ecoat
ZAMAK/Phosphate conversion (clear)/Primer/Paint
ZAMAK/Phosphate conversion (clear)/Ecoat
Finishes we're not considering
Powder coat (poor scratch & abrasion resistance)
Polishing/brushing (Won't match our CIELAB color & gloss requirements)
adv (affil link): Color assessment booths on eBay and Amazon
We plan on testing the coating configurations coming in to see if they meet our environment test requirements but I guess my question is, are there existing resources (literature or otherwise) that rank diecast ZAMAK finish options in terms of appearance, adhesion, UV resistance, etc?
Any help would be greatly appreciated!
May 6, 2020
- NYC, New York, USA
A. Hi Gurshan. Finishing.com did a study for IZA/ILZRO a few years ago where we corrosion-tested some 'green' finishes including Ecoatings and Ecoatings + polyurethane clearcoats. This was but one of many studies IZA/ILZRO has produced regarding finishes for diecastings. A summary of our study and some other studies have been published in "Diecasting Engineer". A little googling with "IZA", "ILZRO", "Diecasting Engineer", and possibly "Dr. Frank Goodwin" should be productive.
You can start with
https://www.researchgate.net/publication/295969663_Selecting_a_surface_for_zinc
which is a paper by Dr Goodwin summarizing our study and an earlier study.
I personally think you will find phosphating to be a more satisfactory paint base than chromating, and that a clearcoat on top of the Ecoating will prove necessary.
Regards,
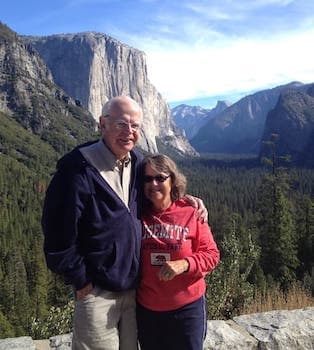
Ted Mooney, P.E. RET
Striving to live Aloha
finishing.com - Pine Beach, New Jersey
May 2020
Hey Ted, Thank you so much for your comment. I found a condensed summary of the study
https://www.eazall.com/PublicDoc/Surface%20Finishes%20for%20Zinc%20Die%20Castings%20-%20Evaluation.pdf ⇩
It's very helpful for relative corrosion resistance of coatings and to an extent, adhesion strength of the coating.
Do you know of any resources that are similar for UV performance? From my initial research it seems that UV resistance for organic coatings comes from UV inhibitors in the coating itself or a specialized topcoat.
- NYC, NEW YORK
May 13, 2020
Ed. update: The above link is broken. Thankfully, the Internet Archive preserved a copy here
Please consider a donation to The Internet Archive. Don't follow abandoned links, old URLs are sought out by hackers!
A. Hi again. Yes, that is the 2006 corrosion study which preceded finishing.com's 2012 update study.
I understand the importance of UV resistance ...
... but sorry, I can't offer any resources.
Regards,
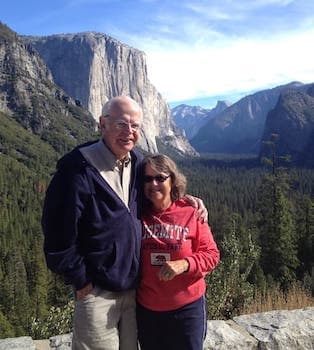
Ted Mooney, P.E. RET
Striving to live Aloha
finishing.com - Pine Beach, New Jersey
May 2020
Q, A, or Comment on THIS thread -or- Start a NEW Thread