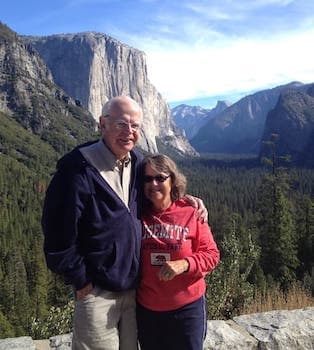
Curated with aloha by
Ted Mooney, P.E. RET
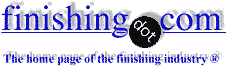
The authoritative public forum
for Metal Finishing 1989-2025
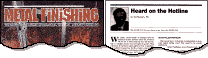
-----
SURSULF PROCESS AFFECT ON HOT SHOTNESS
I AM INTERESTED IN SURSULF PROCESS. I WANTED TO KNOW WHETHER SURSULF PROCESS DIFFUSE S (SULFUR)INTO SURFACE? IF YES, HOW WILL IT AFFECT THE PROPERTIES WHEN COMPONENT IS BEING USED FOR ELEVATED TEMPERATURE. I THINK S DIFFUSION INTO THE COMPONENTS LEADS TO "HOT SHOTNESS". AWAITING FOR YOUR REPLY.
THANKS WITH REGARDS,
- Bangalore, KARNATAKA, India
2002
There's a double whammy for us. Not only do I not know of the surfulf process, I never heard of hot shotness either. But I would agree that sulfur diffusion could cause brittleness at high temperatures.
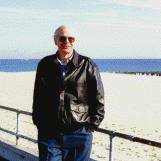
Ted Mooney, P.E.
Striving to live Aloha
finishing.com - Pine Beach, New Jersey
2002
Hi Ted!
Sursulf is a salt bath nitriding process with sulfur added to the bath to accelerate it. It's an old trademark of Park, now part of
Heatbath. Oddly enough I don't see 'Sursulf' on their website, so maybe it's a product they've stopped making. However, I'm certain Mr. Narayan can get the answers he wants from Heatbath.
Oh, and by 'hot shotness' he means 'hot shortness', an embrittling phenomenon caused by excess tramp elements that wind up on grain boundaries.

Lee Gearhart
metallurgist - E. Aurora, New York
2002
2002
Ted- after looking closer at my ancient brochure, Park was the
"Exclusive US & Canadian Licensee" of the Sursulf name, which came from
Hydromecanique et Frottement
Zl Sud
Rue Benoit Fourneyron
42160 Andrezieux Boutheon
France
This brochure predates December 1980, so caveat reader...
- East Aurora, New York
Thanks for taking the time for such a well detailed response, Lee.
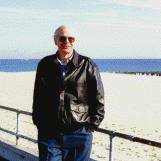
Ted Mooney, P.E.
Striving to live Aloha
finishing.com - Pine Beach, New Jersey
2002
2005
Hot shotness is occurring in hot working process like hot forging, hot rolling which will be carried out 1050-1100 °C. In this case the sulfur in the steel melt is react with Iron and forms a low melting point compound Iron sulfide FeS and it is segregated along the grain boundary during solidification. But this compound melts or fused at hot working temperature and cracks are formed, during hot forging or rolling in these regions. Hence it is called hot shotness.
Increasing the Manganese content reduces or eliminate this problem. Eg, in case of free cutting steel where the sulfur content is kept intentionally minimum of 0.15%{0.035%max in other grades) to facilitate better machinability and at the same time the Manganese content also proportionately increased,because Manganese forms as Manganese sulfide MnS which is higher melting point than Iron sulfide and it will not melt at hot working temperature so this problem is eliminated by increasing the manganese content.
In case of sursulf process the diffused sulfur remain only on the surface in several microns and the parts which are treated by sursulf are not subjected to any hot working process. The question of hot shotness does not arise at all.
- Bangalore, Karnataka, India
We are performing some trials for cam shaft by Sursulf process
Could you please explain more about Sursulf process?
1) In sursulf process the diffused sulfur remain only on the surface. Will there be any affect on the component due to this difuused sulfur and also please explain about white layer.
Thanks & regards
Bhargavi
Employee - Chennai, Tamilnadu, India
September 9, 2010
October 15, 2010
The levels of Sulfur we are talking in Sursulf process is 1 part per million (1 ppm), sometimes increasing by a few more parts per million. This level of sulfur is obtained by addition of Potassium Sulfide in the molten salt bath of Sursulf chemicals. By no way - I repeat by no way - this is going to form iron sulfide and precipitate along grain boundries and lead to melting etc.
1)First sursulf is invariably the last step of manufacturing process. Exception to this can be severe surface finish oriented application like lapped finish components used X Mas tree - say gate valves and seating rings. Hydraulic applications too may require polishing of surface after sursulf treatment to achieve the required surface finish.
2) No mechanical working involved, unless in service like gears and pinions. These are again cold working and not hot working.
3) The presence of Sulfur is in traces. May be we do not have yet a method to determine at PPM levels the presence of Sulfur.
Sulfur besides creating micro surface pores which act as lubrication reservoir, also helps in converting Cyanide to cyanate and carbonate and in formation of epsilon nitride.
Epsilon nitride is more ductile under identical situation
to Gamma Prime nitride, which is predominant in traditional gas nitriding.
Now coming to cam shaft:
Cams make intermittent contacts with tappets and what is required here pitting resistance for cams. Pitting can lead to corrosion subsequently. Sursulf nitriding (followed by Oxidizing called Arcor process) can enhance the pitting corrosion of the cams in cam shaft.
Again I should know which type of cam shaft you are talking about? Chilled iron camshaft like the ones once used in Perkins engines or case hardened steel cam shafts. In the case of steel cam shafts, the advantage of sursulf may be surpassed by the disadvantage of softening of the core, leading to decrease in cross sectional strength and impact resistance of cams while tapping.
Regards
Dr Venkatraman Gopal
- Houston, Texas, United States
Q, A, or Comment on THIS thread -or- Start a NEW Thread