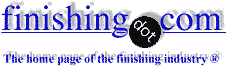
-----
Outgasing on powder coated sandblasted steel
I just opened a small custom powder coating shop. We are coating a lot of used steel patio furniture. We sand blast the items and then coat them. We are having a problem with outgasing on heavily rusted areas. We are learning daily and want to put out a good finished product.
Any and all suggestions would be greatly appreciated.
- Bloomington, Indiana
2002
David,
I assume that you have sandblasted the rust away completely. Powdercoating over rust or oxide is "never" a viable alternative, because the rust will continue to grow, and eventually will peel your topcoat. Also, if you have not completely removed all of the rust, you can have topcoat performance issues such as the ones you are having. You may want to try changing the abrasive media and/or coarseness of the media. Sandblasting can usually work well in this type of situation, however, care needs to be given to even media distribution and completeness of the area needing to be cleaned. Remember that the type of media and it's size will determine how the surface profile will look after the topcoat has been applied and cured. You may want to test different media abrasives on test parts first. Also, make sure that you have properly pretreated the metal soon after you sand blast so that it doesn't start to rust. (At this time, there is NO organic protection from the element! /s so rust comes fast). It may take a bit more impingement pressure if you are using large media. Make sure no organics are left on the part (in the valleys) before topcoat or they may well offgas during the cure cycle.
![]() Bob Utech Benson, Minnesota |
![]() Ed. note: Bob is the author of: "High Performance powder Coating" on eBay or AbeBooks or Amazon [affil links] |
Thank-you for the response. I am wondering about the chemical reaction that creates the gas. It must be activated by the heat of the cure oven. Would a chemical bath, (pickling ?) neutralize the corrosion? We deal with thin and very old substrates that are destroyed by the heavy forces of mechanical cleaning.
David Willibey- Bloomington, Indiana
2002
There need not be any CHEMICAL reaction. The rust is inherently porous and thus is full of air. When the component is heated to cure the coating, that air, now trapped under the coating, simply expands as any gas expands with increased temperature. Either get rid of the rust beforehand, perhaps by use of an inhibited acid pickle (which is likely covered in the archives of this site), or else impregnate the rust with some sort of resin so that the cavities in the rust are filled and thus can't store air. But the latter course could well require vacuum treatment to get good impregnation and of course the filler would have to remain inert at the coating curing temperature.
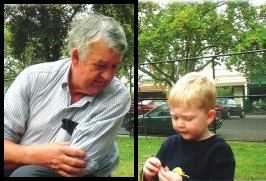
Bill Reynolds [deceased]
consultant metallurgist - Ballarat, Victoria, Australia
We sadly relate the news that Bill passed away on Jan. 29, 2010.
2002
Thank you for the response. I am still confused. I am sand blasting these parts till they free of rust(I think). The parts are not white metal but they are free of rust. Some finished parts look great and others look like a sponge. There does not appear to be any rhyme or reason to what turns out good and what doesn't.
David Willibey- Bloomington, Indiana
2002
David,
We have been operating a small custom coating shop for a couple of years now. We do a lot of auto streetrod and restoration stuff. We have not had the problem that you describe but you may find this interesting. We do a lot of aluminum parts, and they outgas like crazy. What we do to prevent this is to sandblast the parts with aluminum oxide media (120 grit) then prebake the parts at 250 to 300 deg F for about 20 min to 1/2 hr. Then let cool to room temp and coat and bake the coating. The prebake seems to get rid of the gas that is trapped in the casting. This may work on your rusty steel. It's more expensive to do from a time and power point of view but it works for us. It is possible that the media that you are using is too coarse, this will close up the smaller pores and trap some rust inside that will not be clean, even though the parts look clean. Try a finer media. Do not use glass beads, doing so will really close up any minute porosity and give you nothing but grief.
- Thunder Bay, Ontario, Canada
2002
How well does steel and aluminum pre-treated by blasting with Bicarbonate of Sodium (soda blasting) respond to powder-coating?
Thanks...
soda blasting - Memphis, Tennessee
2004
Dave
Can you tell me if the rusting is occurring where there is a metal to metal contact. If so I would suspect that the powder coating cannot get into these areas which would cause this problem. As for the outgassing problem with casting: If you preheat the part to a higher temp then what you cure at say preheat to 400 deg then cure at
375 deg this should solve your problem.
powder coating shop - Brownsburg, Indiana
2004
Q, A, or Comment on THIS thread -or- Start a NEW Thread