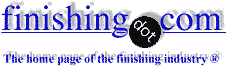
-----
Black chromate on acid Zinc-Cobalt
Q. Dear Sirs,
We are having some problems trying to apply "black chromate" on parts that have been Acid zinc cobalt alloy plated. the color we are obtaining is not real black but a dark olive drab, despite the cobalt content in the alloy ( from 0.2 to 1% Co ) and using a silver or a silver free chromate, the results are consistently the same. Can you give any suggestions please?
Thank You
Domingos J C SpinelliEletroliga H-5
1998
A. Zinc-cobalt and it's black chromate are a package deal, the supplier that sells you the zinc cobalt additives has to supply the adequate chromate as well. It's not for you to try different chromates, silver based or not, the supplier has to advise you what to use.
By the way, acid zinc cobalt is out - alkaline zinc cobalt is in.


Sara Michaeli
Tel-Aviv-Yafo, Israel
1998
A. Domingos,
As you probably know, this is a common problem. One way to get around this is to convince the customer to go for a regular acid zinc plate and then use a highly corrosion resistant Black Chromate. I know of one specialty Black Chromate that gets over 250 hours to white corrosion in neutral salt spray. If this could meet their needs your problem could be greatly simplified.
Mike McDonaldmack products - Jefferson, Wisconsin
1998
1998
A. Domingos,
We run an alkaline zinc cobalt with black chromate from Atotech 24 hrs a day. You are right. We do, on occasion drift from the black to green color. Remember that the chromate is basically olive drab chemistry and if you look up any troubleshooting guide from the supplier, it says to add cobalt.
We, through our own investigation, have found this, not to be true. Like all alkaline systems it is important to maintain the Zinc to Caustic ratio.
What we have found, is that it is even more important, in termsof maintaining a black color, to maintain a ratio between the Zinc metal and cobalt
We typically run with a cobalt level in the range of 160 to 200 ppm
If our zinc drops below 1.0 oz/gal, we lose the black
Raising the Zinc metal to the 1.2 to 1.4 oz/gal range helps us maintain a very solid shiny black
You should also know that we use inert anodes and maintain the zinc with a re-generator
--
The point I was trying to get across - perhaps playing with zinc to cobalt ratio in your acid bath might do the same as in our alkaline case
I have also had experience with olive drab chromates following acid zincs. You should check the chloride level in the non silver black chromate - chloride when dragged in to a chromate acts as a secondary catalyst and changes the color dramatically.
Ray Delorey- Cambridge, Ontario, Canada
1998
A. There are many factors that influence the production of a good quality black from acid Zn/Co solutions.
In my experience the production of green coatings from the above system is nearly always due to low cobalt in the deposit.
%Co in deposit should not be less than 0.8%
The factors that affect Co co-deposition are:-
- Conc of Co in soln. As Co increases % Co increases
- Ratio of Zn: Co.As Zn increases Co decreases
- Ratio of Zn: Cl.As Cl increases Co increases
- Temp As temp increases Co increases opt 28-30 °C
- Agitation. As agitation increases Co increases
Time in black passivate.If the time is excessive then the Chromate appearance will go more green as the time increases.
The introduction of Chloride into the chromate normally increases the depth of black, typically 5g/l is beneficial.
Lynn LewisA. Hi, Domingos:
As Lynn said, there are a number of variables influencing the appearance of ZnCo black chromate, enerally speaking, plating variables and chromating variables.
It should be indicated that Co content in the deposit has different even opposite role in silver and non-silver black chromating processes. For non-silver chromate formulation, high Co content (around 0.8 - 1.2%) is helpful to get real black color. By contrast, low Co content deposit is easier to get balck color. To adjust the Co content in deposit, the rules given by Lynn can be regarded as general guides. In addition, the black apperance is very sensitive to the brighteners in plating bath and the brightness of the deposit, as far as non-silver black chromate is concerned.
Regarding chromating process, pH, chromate concentration, agitation, temperature and time are very important variables. For silver black chromate, of course, silver concentration is definitely essential to be taken into consideration. Too low or too high Ag concentrations both lead to brownish or olive drab black color. Besides, the aged black chromate solution with high Fe content often results in olive drab color.
Another two factors which can be used to adjust the Co content in ZnCo alloy deposit. 1) Co content increases as pH is raised. 2) Co content increases as power is raised. But should be careful with burning problem.
ZnCo alloy plating followed by a black chromate finish is an integral process. Not only chromating variables but plating variables will affect the quality and appearance of alloy plating finishes. The more you play it, the more familiar you get with it. Good luck!
Ling Hao- Grand Rapids, Michigan
1998
Q, A, or Comment on THIS thread -or- Start a NEW Thread