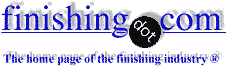
-----
Aluminum anodizing: Constant current vs. controlling the voltage

If you find yourself de-railed by the terminology on this page please review our "Intro to Anodizing", which we think will quickly bring you up to speed so you can readily understand the Q&A's ;-)
Q. Hello,
We seem to be having issues with keeping our power source on constant current. It will not allow us to set our Voltage/Current to the settings required. (Switches to constant voltage)
What would cause this to happen?
Thank you,
Incoming Quality Management - Ottawa/Ontario
January 10, 2023
A. To effectively run constant current/ASF anodizing you will need at least 60 volts to cover most alloys. Most alloys cap out somewhere in the 60s for voltages. To run ASF anodizing you will need to accurately calculate the SQ FT of the part tricky but not impossible. Take the SQ FT and multiply by 24 for 2000/7000 alloy and 30 for the rest. Set your voltage to full with AMPS at zero and slowly raise the AMPS to the total AMPS needed over 5-8 min. Hold for 24 min for 1 mil and 48 min for 2 mils. You should be close to thickness.
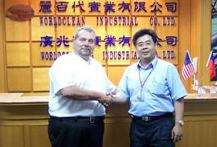
Drew Nosti, CEF
Anodize USA

Ladson, South Carolina
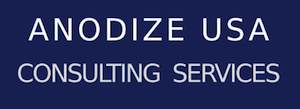
January 11, 2023
⇩ Related postings, oldest first ⇩
Q. I'm thinking about starting Anodizing and at this moment I would like to know how much voltage is usually applied in the process for both large and small materials . . . Can someone Help me out in this subject?
Thank's in advance,
Fridrich GrundingerLager's Inversiones C.A.
1998
A. I work at a shop that anodizes aluminum parts for aircraft. Our solution is a Boric (7.5 g/l) sulfuric (45 g/l) mixture. Our tanks are 48 feet long so we can run large and small parts. The voltage we use is 15 ± 1 Volt. Since we do aircraft, we are rigid about our voltage staying within this range; failure to adhere causes decreased fatigue life, burns, etc. Our voltage range doesn't change regardless of the size of the part.
Voltage has never been a problem for us, rather, the problem is with the amount of amps we draw, i.e., work load. We've gone to a 10,000 Amp rectifier to remedy this.
I guess it depends on what type of anodizing you are trying to do. With other techniques, such as hard anodizing or chromic, the voltage ranges are different.
James A. CorierA. It has been my experience that if you can figure your work load, you are better off running by amps/sq.ft. Voltage can vary because of many different reasons ... Loose contacts, tank temperature, chemical concentration, size of work load, etc.
Voltage will change depending on what kind of anodizing you are doing.
Darrell BarkerA. Architectural sulfuric acid anodizing requires 1.0-1.5 Amperes per sq.dm and you will need 15-17 Volts DC when your solution contains 160-180 gpl sulfuric acid and 5-10 gpl Al(+3) between 18-20 °C. Lower the acid concentration or raise the Al content it requires more voltage which means loss of efficiency, a situation not wanted.
Timur Ulucakaluminum extrusions & finishing - Istanbul, Turkey
A. Good anodizing is done using current density (amps/sq. ft.). Voltage is merely the "driving force" and is dependent upon many parameters in the process. For this reason, it is not a good way to anodize.
Those using constant voltage apply an anodic oxide that is formed from decaying current density because the oxide is a resistor and needs the "driving force" to maintain the required amperage.
This constant voltage anodizing can cause soft coatings, poor dyeability, poor seal (poor corrosion resistance) and usually greatly extends the anodize time.
My advice is to learn to anodize using current density and you will be far ahead.
Charlie Grubbs- Alpharetta, Georgia
Anodizing thickness vs. time
Q. There is an equation that tells a person if they are anodizing using constant current as opposed to voltage anodizing, the time it would take to achieve various thicknesses. Can you share this with me?
Thank you,
Edward f. Yostline operator quality control - Ramsey, Minnesota, USA
2004
A. Anodizing is theoretically by Current Density. I know a lot of anodizers that these many volts at this much time on this type of alloy will get you this thickness of coating; these numbers vary per shop and all ref. current densities
Chris Snyderplater - Charlotte, North Carolina
A. The following equation may help you: H = 0.4 * W * T * J/F
where H is layer thickness in microns
W is Anodic efficiency
T is time in minutes
J is total current (amperage) in amperes
F is surface area in sq.dm
(Anodic efficiency is around 65%)
Jan PrichystalAudio-visual - Denmark
A. I would suggest using the 720 rule. Try using this formula:
Square feet x Amps / Square foot = Anodizing Amps
Example (500ft2 x 20 amps/ft2 = 10,000 Anodizing Amps)
Square feet x Mill Required
___________________________
Anodize Amps x 720 = Anodize Time
Example-
500ft2 x .70 Mills Required
___________________________
10,000 Anodize Amps x 720 = 25 minutes Anodize Time
This should get you very close depending of course on tank temp or part thickness.
Bruce Pfaff- Wausau, Wisconsin
Multiple threads merged: please forgive chronology errors and repetition 🙂
Control of Type III Anodize by Current Density Versus Voltage
Q. Hello,
I'm the quality manager at a small (15 people) metal finishing job shop. We are in the throes of gaining NADCAP approval for several processes. The process that's causing me the most extra work right now is Type III anodizing. Can you recommend some journal articles that spell out the advantages of control by current density instead of voltage? I found the reference books you recommend on this site, but haven't seen much on this specific subject other than "you need to do it this way". I'm looking for some justification.
Thanks in advance for your help. You have a fascinating and useful site. I've already found answers to some other quality problems here.
Jan Harrismetal finishing shop - Tucson, Arizona
2004
Ed. note: Thanks so much for your kind assessment, Jan!
A. Check out http://www.sic.shibaura-it.ac.jp/~sato/lab/plaza/chap328.html, it may have what you're looking for.
"Anodizer's Plaza" --> 100 Q and A --> question 28.
Compton, California, USA
Ed. update: We also loved Anodizer's Plaza, but it no longer exists :-(
Treatment &
Finishing of
Aluminium and
Its Alloys"
by Wernick, Pinner
& Sheasby
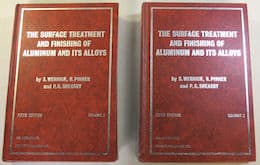
on eBay or Amazon
or AbeBooks
(affil link)
A. Hi Jan
Perhaps you will have difficulties with finding a book, even though I think this is mentioned in Wernick, Pinner and Sheasby's bible. ⇨
It can be explained very easy by the resistance of the formed oxide layer.
If you are doing voltage control Ohm's law U=R*I will show you that building up the oxide layer which increase the R; for the same "U", your current will decrease over time. The decrease will depend on many things such as concentration, alloy, temperature and so forth.
If you on the other hand choose current control You will increase during the formation of the oxide layer (R)
If you have enough voltage, current control will always be the best and most economic way to go.
I have some articles which go into this subject because that is one of the important features when Pulse Anodizing.
Sunny regards
Anne
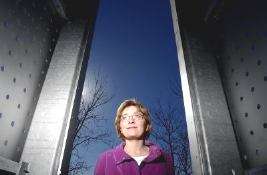
Anne Deacon Juhl
- - Trustrup Denmark
May 21, 2009
Q. For hard anodizing process, I want to know for sulfuric acid bath what should be current increment or how to reach higher limit of current and how do we calculate it?
Nilesh [last name deleted for privacy by Editor]- Anand, Gujarat, INDIA
June 12, 2012
A. Hi Nilesh. Most readers are suggesting constant current, rather than increments. The anodized layer in hard anodizing gets very thick (0.002") and consequently very highly resistive; so, depending on the alloy, to hold 24 - 36 ASF, it may take a lot of volts (maybe 48 -90 volts).
Regards,
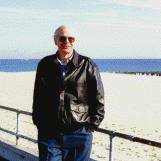
Ted Mooney, P.E.
Striving to live Aloha
finishing.com - Pine Beach, New Jersey
Q. Dear friends,
for Mil type 2 we consider voltage for anodizing, and for type 3, i.e, hard anodizing we consider amperes ...
So why it is like this, why not vice versa -- and which parameter is good voltage or amperes?
Aijazullah Tajir- Abu Dhabi, UAE
March 27, 2014
A. Hello cousin Aijazullah.
Most of our readers do not agree with anodizing by voltage for either process. Rather, they suggest anodizing by constant current :-)
Some "rules" of anodizing science are based on "first principles", but at this point in our knowledge, many are still based on empirical personal knowledge. So, while some people may prescribe complicated amperage-time profiles or voltage-time profiles for a given part of a given alloy in a given tank, believing them to be more effective in some way than a simple constant-current profile, there does not seem any consensus that such complications are an improvement in the general case. Where it can help of course is if you were dealing with constantly changing load sizes which would require constantly changing amperage settings. Good luck.
Regards,
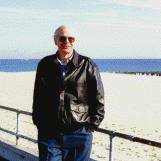
Ted Mooney, P.E.
Striving to live Aloha
finishing.com - Pine Beach, New Jersey
March 2014
Anodizing with Stepwise Voltage
Q. Hello,
I am trying to anodize a 3D printed aluminum in order to color it black. The best result I could get was using stepwise anodizing. Can anyone help me to understand the effects of stepwise anodizing and how I should control the steps and current density? Or any other tips about this process (anodizing in sulfuric acid at room temperature)?
- Germany
November 28, 2017
A. Hi Payam. Anodizing at "room temperature" in sulfuric acid is what people here are calling "Type 2" anodizing (which refers to Type 2 in USA MIL-A-8625 / MIL-PRF-8625 [⇦ this spec on DLA]).
Whether you do 'stepwise voltage' or 'constant current', the reason and justification is the same: bare aluminum is highly conductive, but the anodized coating is resistive/insulative in proportion to its thickness. If you try anodizing a bare aluminum part at a high voltage, the current will be excessive and it will burn; but high voltage is required later on in the processing because current will decrease or stop if low voltage is maintained as the coating builds up and insulates the part. So whether you operate the process by maintaining a constant current density, or you gradually step up the voltage, you are doing more or less the same thing.
Stepwise voltage is sometimes called "ramp control". Per my posting just before this one, some people believe in very complex 'ramp control', other believe in the simpler 'constant current', but this is based on their personal experience (and possibly prejudices) ... I don't think we yet have a solid theoretical basis for choosing ramp control over constant current. However, if load sizes vary, voltage ramp control can accommodate this whereas it might be a hassle to keep changing the current setting for each load.
Regards,
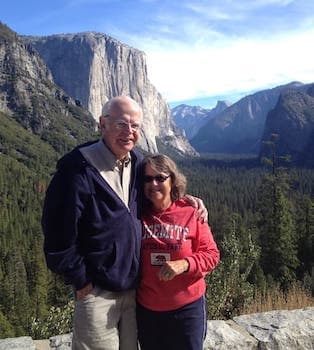
Ted Mooney, P.E. RET
Striving to live Aloha
finishing.com - Pine Beach, New Jersey
Q. Dear Sir,
If we control current density for this anodizing process at 3 A/dm2, is this for anode surface or cathode surface?
Please advise.
Thanks a lot.
- Batam, Indonesia
May 3, 2018
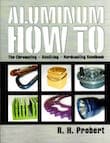
Aluminum How-To
"Chromating - Anodizing - Hardcoating"
by Robert Probert
Also available in Spanish
You'll love this book. Finishing.com has sold almost a thousand copies without a single return request :-)
A. Hi Dallas. Such numbers always refer to the anode (the parts you are anodizing). Robert Probert suggests 24 ASF (2.6 Amps/sq. dm) for hardcoat anodizing with proprietary additives, and half that for conventional Type II anodizing with straight sulfuric acid, so you are probably a bit high for jobshop hardcoating, although perhaps okay if you run only one kind of part and you can optimize for it.
Please fully describe your situation (Type II / III / 2-1/2 -- jobshop or captive --experienced anodizer vs. neophyte -- where you got "3 A/dm2", etc.) so readers don't have to qualify everything with a dozen "ifs, and, and buts" that don't apply to you anyway. While very specific questions can often be answered here, "general" answers often can't be covered in the few paragraphs appropriate to a forum, and require book suggestions. Good luck!
Regards,
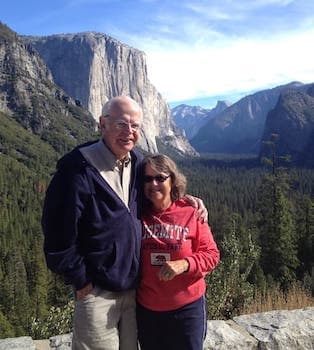
Ted Mooney, P.E. RET
Striving to live Aloha
finishing.com - Pine Beach, New Jersey
Q. Hi my name is Tod Robinson
I am trying to anodize a bunch of different sizes, thickness and shapes of aluminum remote control car parts. I have very little knowledge of anodizing and I need to ask how do I find the square surface of all the different parts? I have rings, shafts, blocks, and all different shapes? Do I need to be exact or can I just a rough guess? Thank you.
- East Brady, Pennsylvania USA
March 11, 2019
A. Hi Tod. Although it's usually not recommended, it is possible to anodize by voltage even if you don't know the surface area; further, there is a technique called "The Parallel Circuit Method", illustrated in Robert Probert's "Aluminum How-To" that allows you to calculate the surface area from the way the parts react in the anodizing tank ... but those are probably better suited to experienced anodizers than beginners.
The truth is that, almost by definition, surface area is absolutely crucial to surface finishing and you need to become comfortable with methods to estimate it!
You can't anodize different alloys at the same time, and the rings, shafts, and blocks are quite possibly made of different materials. I'd suggest picking one part and experimenting until you figure out how to anodize it properly before trying to move on to different shapes and alloys. Good luck!
Regards,
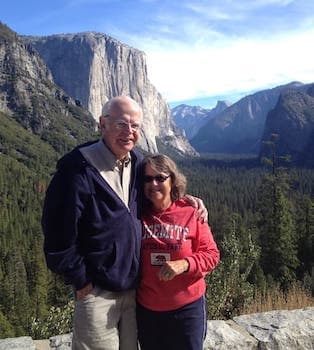
Ted Mooney, P.E. RET
Striving to live Aloha
finishing.com - Pine Beach, New Jersey
April 2019
Q. We apply sulfuric acid anodizing by using constant voltage control and amperage is allowed to roam freely, but we face some problems during the process including :
• Layer thickness for the inner and outer diameter of the same work piece don't match
• The anodizing layer of small threads is easy to remove
• Anodizing layer thickness of different parts is not homogeneous
• Upon assembly, black powder appears in the magnifying devices.
• Not all Al alloys used produce good anodizing layer like 3XXX,2XXX and 5XXX series.
• The dimensions required for the work pieces are of very high accuracy, so I need to achieve the required thickness.
We hope to contribute to solving these problems with your experience in this field.
Sabah elaraby
- Cairo elsalam, Egypt
A. Hi Sabah. You have a lot of problems :-(
You should be anodizing by current density as explained in several responses to this thread which we appended your inquiry to.
• ID and OD thickness not matching isn't a big surprise unless you are taking action unsuccessfully. But you need to be more explicit about what the parts are and their dimensions.
• Threads shouldn't be anodized.
• Both geometry and material can be interfering with getting constant thickness.
• We'll probably need more hints to guess what that black powder is.
• Different alloys need different etching, desmutting, and anodizing parameters.
• It may prove necessary to machine to different dimensions; anodizing may not be able to achieve what you want in terms of dimensional additions.
Luck & Regards,
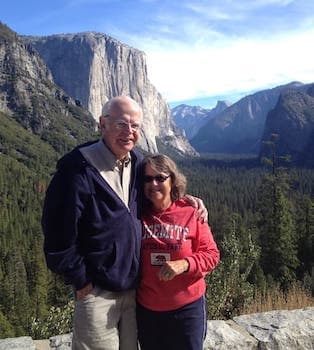
Ted Mooney, P.E. RET
Striving to live Aloha
finishing.com - Pine Beach, New Jersey
Q. I am anodizing a part at 12.5 V 30 minutes without racking and have different colors with anodizing a part for 30 minutes with racking. Does surface area of racking cause this difference? How do we calculate voltage and anodizing time for different loads (I use power supply with adjustable and control voltage)?
Thanks for your help
- Salatiga, Indonesia
December 28, 2020
Q. We are a small shop providing plating & anodizing for our customers only. I am having a problem with a new bath that we just made. I use 175-185 g/l concentration, I am using aluminum sulphate to start at 2 g/l. We have a 600 gallon tank. It is a sulfuric anodize type II.
I started my 1st load after mixing up the bath. I realized I have an Amperage drop; it continues dropping till it gets to zero. I checked my connections. All is well. Can anyone help?
- Miami, Florida
December 15, 2021
by Runge & Kaufman
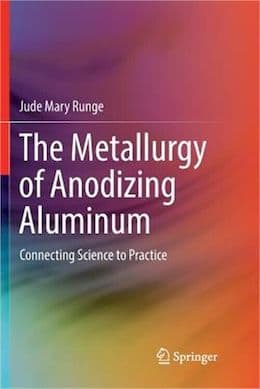
on eBay or Amazon
or AbeBooks
(affil link)
A. Hi Tony. If your previous experience is limited to plating, you need to know how anodizing is different: it builds a resistive oxide coat which impedes the flow of electricity and will cause the current to drop at any constant voltage.
If you have previous anodizing experience and still find what is happening to be unusual, the first thing to check is probably the meters on the rectifier. It's possible they're wrong; on a new installation you might even have the wrong shunt feeding the ammeter. Do you have a thickness gauge to check what is going on with the anodizing?
Luck & Regards,
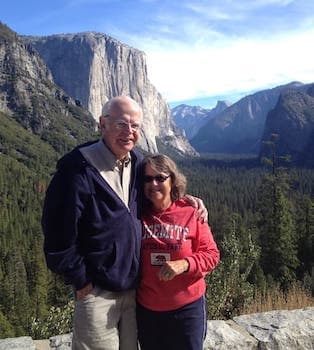
Ted Mooney, P.E. RET
Striving to live Aloha
finishing.com - Pine Beach, New Jersey
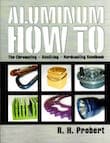
Aluminum How-To
"Chromating - Anodizing - Hardcoating"
by Robert Probert
Also available in Spanish
You'll love this book. Finishing.com has sold almost a thousand copies without a single return request :-)
A. First use Mooney's advice above. then let's check what you say about "180 g/L", that is 60.6 gallons of standard commercial sulfuric acid in a 600 gallon anodizing solution.. Is that what you started with? Now if you used some sort of battery acid ⇦ on eBay or Amazon [affil links] , then tell us the label and we will calculate that for you. Now when you start the current are you chilling the solution to hold the temperature to about 72 °F?
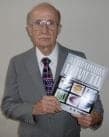
Robert H Probert
Robert H Probert Technical Services

Garner, North Carolina
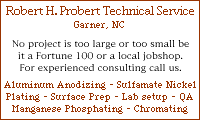
A. It seems easy problem according to your explanation. Most likely source of problem is rectifier or rectifier's setting. You should focus on rectifier with electrical technician in order to find problem. He can measure input/output of rectifier at voltage with a device under voltage. I am sure you will find the problem. I skipped the chemistry of bath because I assume your data is true, checked by a chemist.
alaattin tunaAnodizing Supervisor - sakarya, Turkey
A. Check to see which terminal is hooked up to the cathodes (Negative) And the parts (positive). I had this same problem with a big customer in Romania and we needed to reverse it to get anodizing.
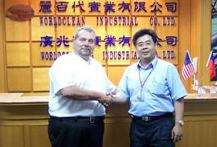
Drew Nosti, CEF
Anodize USA

Ladson, South Carolina
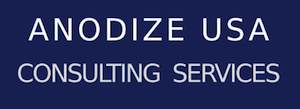
On second thought, I bet Drew's exactly right :-)
Luck & Regards,
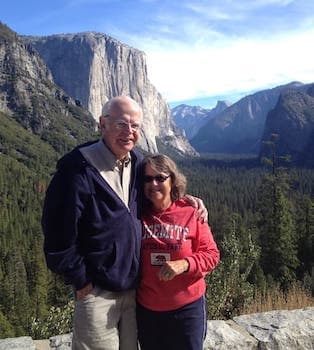
Ted Mooney, P.E. RET
Striving to live Aloha
finishing.com - Pine Beach, New Jersey
A. Hi Tony,
It sounds like you've just had this issue with a fresh tank but have been successful before? Your question doesn't sound like this is a brand new process for you.
Your aluminum is a little low. Normally you'd decant an old tank to get closer to 10 g/L, using the dissolved Al in the heel of the old tank to get right back to work with no fuss. But what I want to put out there is another thing to check -- is your racking, and your connection to the flight bar, still clean and tight? Are you stripping racks between uses? Are the techs scotch-brighting the flight bars before clamping spines to them? Are the undersides of the spines clean? Are the cradles also free of oxidation? Just general question on connectivity throughout the system.
Lots of good advice here and this is one more thing to check on.
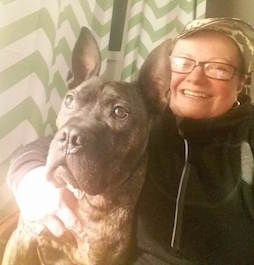
Rachel Mackintosh
lab rat - Greenfield, Vermont
A. What's the voltage/amperage capacity of your rectifier? What amps/ft2 (amps/dm2) are you running at? If you're going by amps you must set the voltage at max on your rectifier so the power is there if needed to keep the required amperage as the non-conductive anodise film builds up. In my experience calculating amps per part via the surface area, 20-24 volts max is usually more than enough (depending on work loads) to keep a good stable amperage (very rarely goes above 20).
Danny BakerSenior Lab Technician - Yeovil Somerset
February 20, 2022
Q, A, or Comment on THIS thread -or- Start a NEW Thread