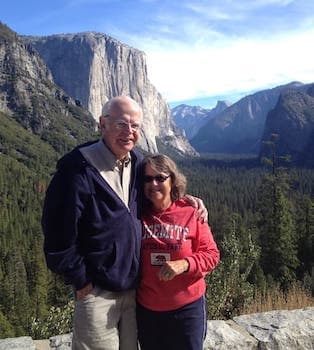
Curated with aloha by
Ted Mooney, P.E. RET
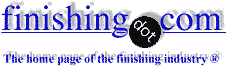
The authoritative public forum
for Metal Finishing 1989-2025
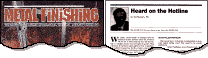
-----
Finish for compressor blade erosion prevention
I am looking for suggestions for a finish to apply to gas turbine engine compressor blades made from AM-355 stainless steel (semiaustinitic, ppt hardened). Currently, blade life is unacceptably low when used in a sandy environment (like Kuwait, for example).
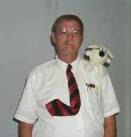
James Totter, CEF
- Tallahassee, Florida
In many cases turbine blades have been electroplated with Palladium ,Platinum, or Rhodium to extend the life and ware.
Louis Hirbour- Yorba Linda,CA. U.S.A.
James:
There has been a lot of work done on compressor airfoils for Jet Engines and ground based steam/gas generators to increase corrosion resistance. One well accepted method is to produce the correct surface texture to minimize moisture retention on the blade surfaces. The process is to vibratory finish the blades with a non-abrasive surface active Oxalate process that will remove micro-surface asperities. This actually produces a negative skew surface profile, along with a passivated and compressively stressed surface layer. This greatly reduces retained moisture on the surface and reduced surface moisture equals improved corrosion resistance. Also, because the surface has been mildly passivated, there are less active Iron sites on the surface to react with moisture to initiate corrosion. The process I am describing here is used by many large ground based steam and gas generator OEMs and has been reported to greatly improve corrosion resistance on steam turbine blades. Good luck,
Bill BoatrightRaleigh, North Carolina
Mr. Totter, You should look among institutions that are fulltime dedicated to this research like the EPRI (ELECTRIC POWER RESEARCH INSITUTE). I believe that the state of the art for your application are the plasma or HVOF coatings of alloys with aluminum, chromium and Ytria. Good luck
Guillermo MarrufoMonterrey, NL, Mexico
James -
Generally, its difficult to find a coating for erosive impact/wear applications like this because of the relative thickness of the coating compared to the diameter of the impact particle. Hardness, toughness, bond strength, and thickness of the coating all need to be maximized as much as possible. Your best bet might be a thermally-sprayed coating such as tungsten carbide or chromium oxide, but if that's the case don't be afraid to ask for the coater to really layer it on (hopefully you can still keep the parts within tolerance). I hope someone from the field of cryogenic treatment speaks up here, also - it seems like something that would help (not solve, but help) you with your problem - but I don't know enough about the topic personally to go preaching about it. If you find anything marginally successful, please post it here, as I was recently involved in a similar line of inquiry and I would be very interested to see what you come up with.
Erik Mundy- Kingston, New York
I worked for a company that did aircraft engine overhaul several years ago and electroless nickel was the choice, particularily on aluminum stators.
Thermal spray, while good, is too rough for an airfoil surface and would destroy engine efficiency. It would seem like an excellent candidate for PVD, if you can afford it.
James Watts- Navarre, Florida
Electroless nickel has been successfully used for compressor blades in aircraft engines. For increased hot corrosion resistance EN followed by cadmium and a chromate followed by diffusion of the cadmium into the nickel. There are environmental issues to deal with if Cad and chromate is used.
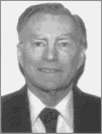
Don Baudrand
Consultant - Poulsbo, Washington
(Don is co-author of "Plating on Plastics" [on Amazon or AbeBooks affil links]
and "Plating ABS Plastics" [on Amazon or eBay or AbeBooks affil links])
Multi-layer PVD coatings were developed by the Russians for their helicopters due to high levels of turbine compressor blade erosion in Afghanistan. The U.S. Navy is in the process of setting up to apply the same coating on some of their helicopter turbine blades.
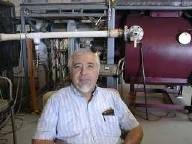
Jim Treglio - scwineryreview.com
PVD Consultant & Wine Lover
San Diego, California
Abrasion resistant tungsten carbide liners and claddings used for fans and other severe wear applications may be applicable.
Bob JanisMfr. Rep. - Lakeland, Florida
Sir,
There is a new type of patented advanced HVOF method that can apply a coating on your blades with a 20 micro finish of carbide. The problem with HVOF is that it is too rough of a finish to polish down to an acceptable finish that will not create air flow resistance.
- Charlotte, North Carolina
I would consider Titanium Nitride (TIN) applied by PVD it is an extremely hard, thin film coating that is applied mostly to precision metal parts. There have been applications recently on 400 series compressor blades on large gas turbines.
There is some concern in the industry that if the coating is breached and the blade is in a wet environment with chlorides present that a corrosion site might develop. This has not been shown to occur with TIN PVD applied coatings to my knowledge.
Miles ValentineTampa, Florida
2007
Q, A, or Comment on THIS thread -or- Start a NEW Thread