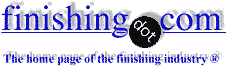
-----
Thickness Measurement Methods Question
I am need of some help before I pull any more of my hair out which I cannot afford to lose.
I have a part that I am plating with nickel sulphamate. The surface area of the part is approximately 1.3534 square centimeters. I have weighed the parts before and and after the nickel plating. My typical pre-plated weight is .1279g and my post nickel plated weight is .1455g. Using the density of nickel of 8.9 g/cc, I get a thickness (as determined by weight) of approximately 540 microinches. By cross-section, the values are quite different. By cross-section I get approximately 375 micro-inches. I have cross-sectioned well over 1000 of these parts and have found the cross-sections to be fairly consistent.
I have also done the same process of weighing parts using gold. My gold data by weight is almost a linear fit with a slope of 1. That said, my weight and cross-section data for gold are almost spot on. I am using the same calculation for gold as nickel with the only difference being that I picked a density of 19.1g/cc for gold.
Does anyone have any idea why my nickel data by weight would be 50% different than my nickel data by cross section when I can do this calculation well with gold. The nickel weight does have very good grouping (low sigma) so I know its not weighing problems (at least I think).
Any help would be appreciated
Dana Tompkins- Boulder, Colorado, USA
Dana,
To start off, I'm not a nickel, nor a gold plater.. my background is anodizing. The thought comes to mind, though, that perhaps there is an etching/cleaning process done before the nickel plating that is causing weight loss on your part after your initial measurements. Have you tried reversing your weighing process? Perhaps you should weigh your part after plating, find a solution that will dissolve the nickel (I believe nitric acid will dissolve nickel), but not your substrate (you didn't mention what your substrate was), then re-weigh. Perhaps then, your numbers will make more sense? Just a guess, though..as this really isn't my background. But that is how I measure coating weight in anodizing (I'll use a chromic/nitric acid mixture that will dissolve the anodic coating, but won't attack the aluminum substrate.
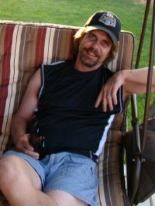
Marc Green
anodizer - Boise, Idaho
Dana,
Using the weight increase will give the average thickness of nickel but not how the nickel is distributed on the part.
There will be areas of high thickness and areas of low thickness. Your parts are very small. Do you see any edge build up of nickel on your parts. The edge build up can be 10-20 percent more nickel?
What is the shape of your part? Is it plated on one side or on both sides? I have seen people plate on a 2 sided thin flat part and neglect to calculate the surface area of the edges. This can frequently be 10 to 30 percent of the total area.
Your technique to prepare the cross sections seems very reproducible. Any chance you are smearing a soft base metal over the nickel? What is the base metal? Are yu using an etchant after polishing to remove any smear?
Are you using the same magnification to measure both the nickel and the gold? If they are different lenses maybe the one use for nickel needs to be recalibrated.
Finally - Is the surface of the part rough or porous? This can increase the surface area dramatically and it takes more metal to cover a rough surface than a smooth surface to the same average thickness.
Hope this has given you some things to think about.
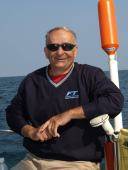
Pat Mentone
St Paul, Minnesota
Q, A, or Comment on THIS thread -or- Start a NEW Thread