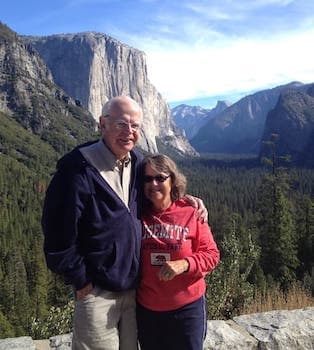
Curated with aloha by
Ted Mooney, P.E. RET
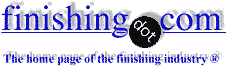
The authoritative public forum
for Metal Finishing 1989-2025
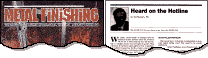
-----
Difference in Durability and Rate of Oxidation of a 440A Grade Carbon Stainless Blade and a 300 Grade
I sell knives for CUTCO, and recently I was discussing the grade of metal we use in our carbon-stainless steel blades, (type 440A) with a customer who owns a gun stock business who argued that a 300 grade metal would be better for a knife blade, and added that if 440A is used in doctor's instruments, why then do scalpels rust? I didn't have any answers and I am not familiar with the properties associated with the different grades of metals. Could you please explain the difference in durability and oxidation between a 300 grade steel and 440A Please.
Kasey Mayclin- Mitchell, South Dakota
First of two simultaneous responses --
440A is a martensitic stainless steel. That means you can make it very hard and wear resistant. It doesn't have a great deal of corrosion resistance because so much of its chromium is tied up by carbon in the hardening process. 304 is very corrosion resistant, but it is pretty soft for knife blades unless it's highly cold worked. Only cheap knife blades use un-hardened stainless or those where holding a sharp edge is secondary to corrosion resistance.
Mike McGuire- Pittsburgh, Pennsylvania, USA
Second of two simultaneous responses --
Hi Kasey,
You're asking for a book! But without going into WHY the properties of the materials are what they are, the end result that the user sees is:
300 series stainless steels have better corrosion resistance than 440A stainless. Generally vastly better, not just a bit better.
But 300 series stainless steels can't be hardened, so they can't hold an edge. No good for knives or scalpels!
But 440A can be heat treated to a very high hardness, as you well know, which is needed for cutting edges. But the same aspects of chemical composition that allows 440 to be hardened, simultaneously prevents the high level of corrosion resistance of the 300 series. 440 has resistance to rusting, and resistance to corrosion by various mild corrodents, but falls far short of any of the 300 series steels.
There are other stainlesses that are developments of the 440 base, and that have better corrosion resistance than 440 and can be hardened at least as high as 440, and have better edge retention than 440, but you're talking big dollars for the better material. The cost/performance balance seems to make 440A and 440C the materials of choice for the stainless knifeblade application.
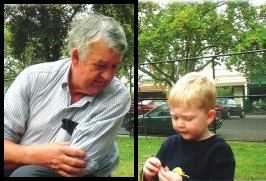
Bill Reynolds [deceased]
consultant metallurgist - Ballarat, Victoria, Australia
We sadly relate the news that Bill passed away on Jan. 29, 2010.
As mentioned in the previous replies, 440A stainless steel is martinsitic and can be heat treated to make it harder. It has 16-18% Chromium in it but no nickel. Conversely, 300 series stainless steels have between 16 and 26% chromium and between 6 and 22% nickel, depending on the grade. The nickel contributes to the 300 series corrosion resistance, but is not the only reason for this enhanced property. The lack of nickel in the 440 series will result in a deterioration in the metal's corrosion resistance compared against the 300 series materials. there are many authoritative text books on the properties of stainless steels, which should be consulted if you want chapter and verse.
300 series stainless steels cannot be heat treated but they can be hardened if they are extensively worked. However, what is more important, as far as good edges for knives and the such is concerned, is the amount of carbon present: - 400A has between 0.6 and 0.75%, whilst 300 series has between 0.03 and 0.25%. These high carbon content steels are known as "high carbon steels" and have been used for sharp edged products such as swords and razor blades for many years -it is only since the 1960's that stainless steel has been used in razor blades and these use only special alloys. There are two essential features in having a sharp edge; the first is the ability to make it and the second is the ability to maintain it. It is very difficult to produce a sharp edge on soft metal because of its ability to deform and round off - have you ever tried to sharpen pure lead or tin? Furthermore, if the base material is essentially soft (i.e., not hardened) it will soon lose any edge imparted to it, so the ability to harden the edge becomes essential. 300 series stainless steels have typical hardnesses of about 180-300Hv (Vickers), whilst hardeneable stainless steels can be as hard as 600-700Hv.
In days gone by the art of sword making was a highly treasured skill as a good sword that kept its strength and sharpness whilst not breaking was essential to the owner's survival. One method used to increase the amount of carbon in the outer layers of good swords was to plunge the red hot sword into a convenient prisoner of war or hostage. Fortunately these days have long gone, but I believe it was practiced until the Middle ages, especially in Europe and Western Asia.
Although 440A stainless steel is mentioned, both both 440B and C have even higher levels of carbon in them, 0.75-0.95 and 0.95-1.2% respectively. These would make even better sharp edges, but they are probably more expensive than 440A. I hope this explains your problem.
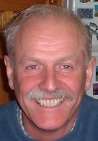
Trevor Crichton
R&D practical scientist
Chesham, Bucks, UK
Ok, Trevor... No problem with anything you said about carbon content...but I couldn't let the comment about the swords pass! :) I can't speak about the forging practices in Europe, but as a student of Japanese Sword, I have studied the history of the craft. By the year 900, the Japanese sword was made using essentially the same techniques that are used by swordsmiths today (yes, there are still swordsmiths in Japan). The swords from year 900 on were single edged blades with curvature (the famous "Samurai" swords). The central core of the sword is forged from a billet of lower carbon content steel and a higher carbon steel jacket (forged and folded) surrounds it. After forging is complete, the blade is covered with a slurry of clay. The smith carefully scrapes off clay at the edge of the blade. This leaves a thicker layer of clay on the back (known as the 'mune')than on the edge (known as the 'ha'. The blade is then heated for the last time and traditionally is quenched in water, NOT people. Although smiths kept their methods somewhat secret, the temperature of the water was described as "the temperature of the water in February". Not quite body temperature, eh? (Note: Some blades were oil quenched during the Showa era...that is; around WWII, and are not considered entirely "traditional" because of that.)
The purpose of the clay is to form an insulating layer. This allows the edge of the blade to be quenched quicker than the back of the blade. The edge is harder (and more brittle), but holds an extremely sharp edge. The back of the blade, cooled at a slower rate, is softer. In combat, one slashes with the edge of the blade, and blocks with the softer back of the blade. Having the central core steel softer, makes the sword more flexible and thus less likely that it will break in battle. It is true that CUTTING practice (to prove the fitness of certain blades) was performed on the corpses of executed criminals along with a variety of armor and other objects, but the quenching of the blade to harden the edge was done under very controlled conditions in water. :)
Ronna Erickson- Amherst, MA.
While Moby Dick [on Amazon affil links] is obviously fiction, it is also largely fact-based. And the good captain, Ahab of Nantucket, orders the three barbs of his harpoon quenched in the volunteered blood of his three harpooners.
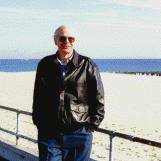
Ted Mooney, P.E.
Striving to live Aloha
finishing.com - Pine Beach, New Jersey
Maybe the good Captain did not want to tap into his fresh water barrels. ;) (Wouldn't want to waste good water now, would you?) Maybe that is the way things were done in England, and thus in the Colonies as well. I have no idea.
For quenching,his whale oil would have done an equally good job, no doubt.... but it just isn't as good a story as using the blood of the harpooners. I can only vouch for the techniques used for making Japanese swords.... They used water.
Ronna Erickson- Amherst, Massachusetts
What can you tell me about 17-4 s.s ? and Inconel s.s I know its good and I know you can do alot with the two of them its very tugh steel but how good are they for sword making?
Joseph Davidovtool & die maker - Toronto, Ontario, Canada
Q, A, or Comment on THIS thread -or- Start a NEW Thread