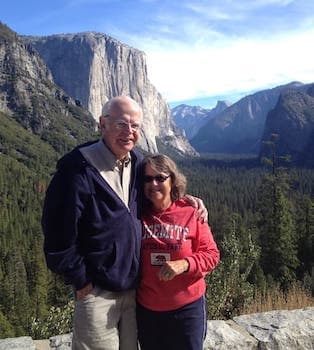
Curated with aloha by
Ted Mooney, P.E. RET
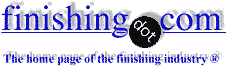
The authoritative public forum
for Metal Finishing 1989-2025
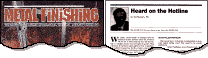
-----
Salt Spray Results vs. Panel Preparation (Alodine, Iridite, Chem-film, Mil-C-5541)
Q. Hello,
We have been getting irregular chem film salt spray results the last few months and aren't sure what the issue is.
Our Iridite bath started producing poor coatings, resulting in yellow 2024 failures, but yellow 6061 still passed.
The following month, we had another yellow 2024 failure and a clear 2024 failure, but yellow and clear 6061 still passed. Because clear 2024 also failed, we assumed it was an issue with our 2024 panels and found a new supplier.
Next, we replaced our Iridite bath. We then passed yellow 2024 but failed yellow 6061. We also failed clear 2024 despite new panels (clear 6061 passed).
Currently, we are dealing with failures on yellow 6061 and clear 2024. We are passing yellow 2024 and clear 6061. 2024 panels are new and from a more reputable supplier. 6061 panels are old stock, but are passing our two week anodize salt spray, so I don't think the 6061 failures are panel related.
I am not sure why we are getting these flip flop results. If anyone has any troubleshooting ideas or recommendations, they would be greatly appreciated.
- Denver Colorado
April 12, 2024
A. At a previous shop that I worked at we polished the panels first which corrected all of the scratches and irregularities of the panel or differences between panel suppliers. It made a huge difference in salt spray performance. You may need to hand clean the panels to remove any buffing compound prior to processing. I am not positive this is currently allowed, but at the time there was no prohibition against prepping the panels that way.
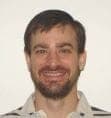
Jon Barrows, MSF, EHSSC
Independence, Missouri
April 17, 2024
A. Hi Zander,
There are a few things that stand out to me from your question. You're going through the traditional trial-by-chromate conversion coating [CC so I can stop typing it out] that all us lab dweebs have lost sleep over at one time or another (*cough cough last week).
2024 is objectively harder to conversion coat than 6061 due to the alloying constituents. I think it's the copper that twists the knife in this case, but I'm not a metallurgist.
I'm gonna start by saying, don't ever beat yourself up over passing double-hours salt spray anodize on the same substrate you failed CC. It's not apples to oranges. It's apples to carrots.
Anodize gets a WAY more aggressive etch prior to processing than a cc does. CC should only be routed for a flash etch to the point where the tech observes an even fizz across the whole surface, bang, done, get it out of there. Too long brings way more of the non-Al constituents into play.
Anodize tends to be routed for an etch that actually has a dimensional goal, and is therefore significantly longer and takes off more material. This negates the Mill Roll problem, which we will get to.
After we talk about seal.
I'm again not an expert, but Taber Abrasion, Coating Mass, and Coating Density give data on the quality of your time in the ano tanks... salt spray tells you how well your seal likes its substrate.
You can work MAGIC with a good seal over a good crystalline structure, even over an ATROCIOUS substrate.
Conversion coating gives you neither of those things to work with.
Test coupon substrate is literally the bane of my miserable lab rat existence, and I'm not even being facetious here.
Fact: your customers who need +6 non rohs cc are sending you really sweet precisely finished parts, in a hurry, so fresh off the 5-axis that they still smell like overheated coolant from that new 'engineer' who is on a mission to drive down run times. *SKREEEEEEEEEEEE you know that sound.
Unless there's smearing from a bad mill op, or the coolant is literal ectoplasm, those parts are theoretically ideal.
Fact: your test coupon supplier is not milling a nice surface on your panels. They are either mill roll, or sanded to some degree that you need either a microscope or a salt fog test to confirm adequate. In the second case, you're in trouble by the time you know why. Therefore, they are already not meeting the intent of the [absolutely poorly designed] spec.
In fact, your coupons being rolled sheet stock while your customer parts are probably milled from a fat extrusion or plate [assuming 6xxx or 2xxx] just means you're testing ... the quality of your coupons. Not the customer parts, which come to the CC shop clean except for paw prints and coolant stains. No big whoop. Not much etch required, rock n roll.
You can see how this is problematic.
Can we talk about 'pass' and 'fail'. Your lab gives pit count per panel. In a set of 5, do you have results varying from 0 to >5 within one set, or is it all sorta borderline, or is it a full set of catastrophic failures? This is a HUGE question.
You say "clear", I assume you are running B449? Are you passing coating mass? (Unrelated to salt spray, but Nadcap auditors got sent an alert about this just recently, and it's a hot mess in which actual customers also seem to be like, "wait whut, why do I need that? It passed salt spray dude?", heads up).
You hold Nadcap, and I assume you also trace substrate mill certs; look at your source mills and H/L codes more than your panel suppliers. I hope you have actual mill certs, not just supplier hand me down certs.
In the past 4 years, the aluminum supply has gone off the rails. A previously trusted test coupon (certified as test substrate, adhering to specific ASTM specs) supplier sent me a grand worth of *ahem* imported from outside NATO substrates, since my dumb ass assumed it was sort of you know... a given, for a company selling to various Nadcap shops. My bad for a P.O. missing the statement "please don't send me metal from a country we are in an active trade war with, and also no Uyghur labor, plsthx xoxo #ano4lyf!!" .
I kept them and chopped them up for dye samples for Sales. I did report the issue as a heads up. No refund requested, professional courtesy. We used the bits.
The same supplier then sent a subsequent lot of material with inclusions. Nicely sanded on one side, really did a nice job hiding them... anyone who has worked with Oak wood as a fine finish carpenter will get this best. It's the closest thing to describe the defect.
More sales color chips. Last order from that vendor. I bought a mini air RO sander for $30 and resigned myself to a permanently ratty manicure from now on.
I don't keep my Museum of Crappy Aluminum in my phone, otherwise I'd post examples.
Next up. Did you dump and replace the whole bath, or did you leave a heel? If it was a full dump, what did you do to precondition it? CC, like ano, doesn't work right 'out of the box'. It needs to build up an agreeable level of aluminum to activate fully. Why they don't advertise a new tank supplement is beyond me, lol couple tablespoons of salt and some AlOx powder...
Quick before your tank gets too old, grab a sample and run it through your ICP-OES (or AA) and check aluminum chromium barium iron copper nickel zinc. Hold that data for "fresh tank" reference, as well as titration results from the day you took that sample.
I recall chatting with you previously in 2021, and there's a bunch more info there, specifically about deox... go back and check up... you have a LOT of moving parts in your situation. We will get you straightened out.
Cheers
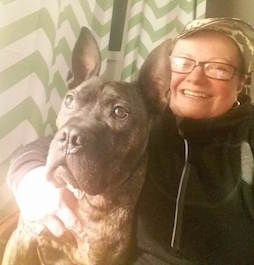
Rachel Mackintosh
lab rat - Greenfield, Vermont
June 15, 2024
⇩ Related postings, oldest first ⇩
Q. Here I am revisiting an old thread with a new focus... Here goes:
We failed our colored Alodine salt spray testing for about 5 months before we finally got a hold of the problem (I think) and are now passing, albeit barely. My question is this: Is salt spray a controlled test to show corrosion protection under ideal circumstances or a test to be representative of production parts?
I am inclined to believe the former, meaning that one could use any means at their disposal for cleaning and treatment (i.e. scotch brigt-ing with DI water and solvent cleaning...) in addition to concurrent processing with production parts prior to the test. If the latter is true then only processing concurrently with production parts would be allowed to ensure that the test panels are representative.
I am very curious to hear some replies to this question. I strongly believe that the SS test itself is irrelevant as a qualitative test, and too greatly ambiguous to be a "standard" since no two companies/entities are likely to prepare and process the test panels identically.
Fire away!
Benjamin J. Curto- Ponderay, Idaho, USA
2002
![]() |
A. Go to the ASTM Spec ASTM B117 and read about SS. It is, as you say, a controlled test to show corrosion under ideal circumstances and it is always done on panels and should not be done TO SPEC on parts. The single most important and most frequent reason for failing is the existence of PITS in the panels before you ever apply the chromate. After that the surface preparation is next: Non-silicate soak clean, CWR, Proprietary Deox (nitric alone will not do it), CWR, Chromate 1.8 oz/gal, 1.8 pH, 1.8 minutes, room temperature, then CWR, dry on some "yellow rinse water", do not wrap until 24 hours later. Take two aspirin and call me in the morning. ![]() Robert H Probert Robert H Probert Technical Services ![]() Garner, North Carolina ![]() A. Ah, our favorite subject--the salt spray test. The salt spray test is a process control tool. For example, if under the proper circumstances, a coated part will pass 240 hours of salt spray, and suddenly, it does not, there is something wrong with the process. If you refer to B117, there are several paragraphs which attempt to "warn" the user of the deficiencies and suggest the proper use of the test. (Also note that B117 is not a TEST, it is a standard practice for operating a salt spray chamber.) Cynthia L. Meade- Sylvania, Ohio, USA |
Q. Dear readers,
I would like to know if really all Alodine 1200 conversion coated specimens undergo 336 hour salt spray test?
Based on my experience some of them fail after 200 hours.
I would like to know how can we rely on the salt spray results?
When we were developing a chromate free conversion coating, one of the coatings withstood salt spray for more than 400 hours without any significant corrosion product on AA2024 (as per MIL-81706 specification); but when it was tested in EIS [electrochemical impedance spectroscopy] it showed poor performance ... why?
Please I would like to learn more about this aspect.
- Bangalore, Karnataka, INDIA
August 12, 2013
A. Hi Yoganandan. This is a very complex question. NASA seemed to feel ("Improved Accelerated Corrosion Testing of Zinc-Rich Primers", NASA Tech Briefs, March 2000) that EIS plus natural exposure proved to be a good way to test zinc-rich primers on stainless steel. My limited understanding is that NASA discovered that after a small amount of natural exposure there was a degradation of the coating that could be discovered via EIS long before it became apparent via visual or microscopic examination, and that the degree of this degradation seemed to be a good indicator of how long the coating would last. But what is your basis for believing it is an effective way to test non-chromate conversion coatings on aluminum? (I'm not saying it isn't, just that it sounds like a huge extrapolation from very limited data).
As Cynthia has told us, accelerated corrosion tests are only quality control tests. Whether salt spray or EIS, I believe an accelerated test correlates to real exposure life only to the degree that has been proven, if that much.
Regards,
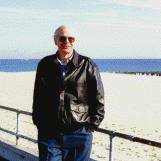
Ted Mooney, P.E.
Striving to live Aloha
finishing.com - Pine Beach, New Jersey
A. In the greater Seattle area, following Boeing & NADCAP guidelines, the Alodine 1200S panels are subjected to salt spray analysis for 168 hours. The Boric/Sulfuric Anodize are 336 hours.
Fauna Tester- Seattle, Washington, USA
Q. Hello all!
I work in a aerospace company and we have been facing some problems to have Alodine 1200S 2024 sheets approved on salt spray. We operate a new line but using the same specifications and products from an older line.
We don't have problems with other Al alloys. We sent some sheet samples to a supplier to check the Al sheet and the results are good. The next thing we tried was to borrow some Alodine from our supplier in order to make tests. Even with our supplier Alodine the specimens failed the corrosion test.
Our process sequence is: Alkaline hot degreasing, DWR, Acid cleaning (base is inorganic acids and ammonium bifluoride), DWR, Brightening in Nitric Acid, DWR, Chromating, DWR and drying.
My suspects are on surface preparation. Do you have some idea of what can we do to find the problem?
- Guaratingueta, Sao Paulo, Brazil
August 22, 2013
A. Hi Adriano. Buy new test panels from at least two different vendors before wasting any more time on process work. This problem has been addressed several times in this forum, but what the salt spray test mostly tests is just the quality and age of the test panels :-)
Regards,
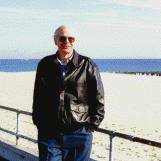
Ted Mooney, P.E.
Striving to live Aloha
finishing.com - Pine Beach, New Jersey
A. Adriano, I would leave out the nitric acid brightener dip as nitric acid can passivate aluminum to such an extent that the conversion coating will not form properly. Instead use a proprietary de-oxidizer with sulfuric acid. Our experience is that sulphates in the rinse water prior to conversion coating will greatly improve the color and coating weight of your coating and the chance of meeting the salt spray requirement.
Regards,
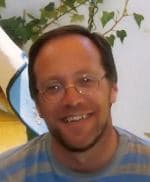
Arnold Langeveld
aerostructures - Papendrecht, The Netherlands
November 4, 2013
Q, A, or Comment on THIS thread -or- Start a NEW Thread