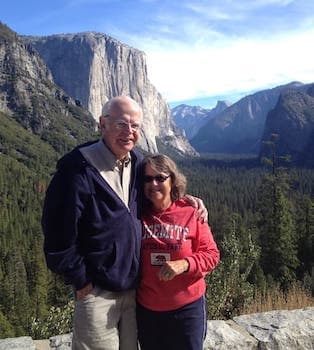
Curated with aloha by
Ted Mooney, P.E. RET
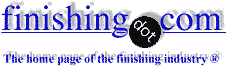
The authoritative public forum
for Metal Finishing 1989-2025
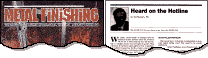
-----
Marine copper plating
Our company manufactures sailboat parts and sailing equipment. Recently, we've begun building centerboards for sailboats that are unavailable elsewhere. My problem is this: Many of my customers would like to have a copper plated steel centerboard. Approximate size, 3/8" thick, 24" wide, 48" long. As you can see this is a fairly large plating project. The copper plating would provide an anti-fouling protection in saltwater marine environments. In order to be competitive, I would like to begin doing this plating in-house. Should I plate with zinc first, then electroplate with copper? The plated layer can be quite thin and still be effective.
Any advice greatly appreciated.
Joel Santarone- Boise, Idaho USA
![]() |
If GM and GE can't afford to do in-house plating maybe it's not going to save you as much as you hope :-) But I don't think you want to zinc plate these centerboards before copper plating. It would seem to me that sacrificial corrosion of the zinc would undercut the copper severely. Also, make sure the copper plating is legal. As you allude to, it is a powerful biocide; and powerful biocides like the formerly popular organotin paints have been outlawed for most applications. I'm not saying copper is a problem, but check before you build a plant to do it. ![]() Ted Mooney, P.E. Striving to live Aloha finishing.com - Pine Beach, New Jersey Hello ! I read your question to plate copper on steel part. I do not think so you have to plate zinc then copper. You can plate copper strike on steel then copper plate and acid copper. ![]() Popatbhai B. Patel electroplating consultant - Roseville, Michigan Joel, I really don't think you would like to do the plating in house. It takes a totally different approach to a fabrication facility and even poses antagonic issues to your existing equipment, environmental liabilities and overall operation. Think of a new company put up for the purpose, if it makes sense and the business could support it, go ahead. If not, go out shopping for the lowest price contractor which still gives you the quality you need. If cost is still jeopardizing your project think of other possibilities like buying from low labor countries. Guillermo MarrufoMonterrey, NL, Mexico |
Joel,
May I stick an oar in?
How about a suitable plastic? Am thinking of urethane, but not the el-cheapo paint you get in the stores but the 2 component Urethane.
I was never involved with Urethanes because their chemistry is not as good in acids as many other thermoplastics ... but their abrasion resistance is superlative and the urethane elastomers have an enormous stretch capability.
Back in ye olden days I got some from Monsanto. Superlative smooth finish. Hard, super smooth finish. I painted the garage floor as an experiment but then wished I sure hadn't as it became very, very slippery when wet.
Am not sure of its bonding strength to steel. This is something you'd have to find out. Also you can get them in different grades of 'flexibility' rather than the dead hard paint I used which might suit your purpose better. I suggest you approach a local (?) fabricator specializing in these materials for some advice.
Food for thought, eh?
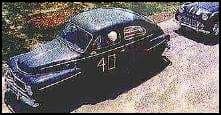
Freeman Newton [deceased]
(It is our sad duty to advise that Freeman passed away
April 21, 2012. R.I.P. old friend).
Q, A, or Comment on THIS thread -or- Start a NEW Thread