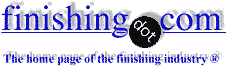
-----
Standard Average Thickness for Anodizing
What is the standard anodizing thickness in terms of mils or microns? Coming from overseas, it seems that our factory actually produces thicknesses of 15 mils, yet after speaking with some domestic buyers, they are buying only 7 mils amount.
Thanks.
John Brinks- New York, New York
![]() |
It is dangerous to use a phrase like "standard" thickness or "commercial" thickness because if a dispute arises you have nothing to go by but hearsay. Rather, you should refer to a specific spec and require a specific thickness. ASTM B580-73 calls for 2 mils for hardcoat; 0.7 mils for Architectural 1; 0.4 mils for Architectural 2; 0.3 mils for automotive exterior; 0.2 mils for interior use at moderate abrasion; and 0.1 mils for interior use at limited abrasion. However, higher thicknesses may be required if you are doing colors; the darker and more saturated the color which is sought, the greater the required thickness. It is common, for example, to use up to 0.7 mils even for interior use if the parts are to be dyed black. Without knowing what you are building, it's hard to say for sure, but 0.7 mils sounds like a substantial coating thickness that will meet MOST needs. ![]() Ted Mooney, P.E. Striving to live Aloha finishing.com - Pine Beach, New Jersey Wow....are you sure we are talking about anodizing here? 15 mils would be a pure coating (almost burnt), and 7 mils is pretty high too..achievable only on a few select alloys, but definitely not a "standard coating". I'm assuming we are talking about hardcoat here.. so a standard coating (mil spec 8625f) would be 2 mils, or approximately 50 microns (roughly 25.4 microns=1 mil=.001"). Of course, more or less coating thickness is achievable, depending on the application. ![]() Marc Green anodizer - Boise, Idaho |
Marc,
Obviously 7 and 15 mil's are out of the question. My guess is he meant 1.5mil's for hardcoated surfaces and possibly .7 mils for type II? Or possibly he was measuring the build-up on the part, and getting .7 mil build-up which would tend to indicate a 1.4-1.5 mil hardcoat layer. Going with the 50% buildup 50% penetration arguement. Obviously there was some mistake on what was intended here, but I think that above scenario sounds more "in-line" with what we all know about anodizing.
Matthew Stiltnerplating company - Toledo, Ohio
Perhaps there is a decimal point that was omitted? 1.5, and 0.7 would make more sense. I should have caught that (like Ted did?) prior to replying last week.
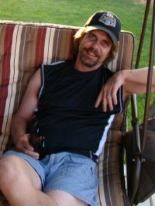
Marc Green
anodizer - Boise, Idaho
Q, A, or Comment on THIS thread -or- Start a NEW Thread