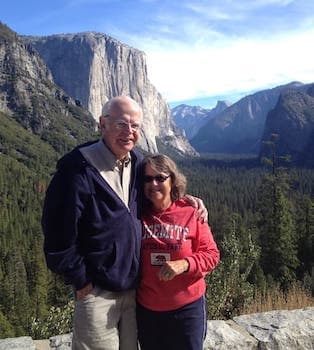
Curated with aloha by
Ted Mooney, P.E. RET
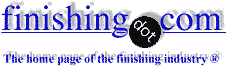
The authoritative public forum
for Metal Finishing 1989-2025
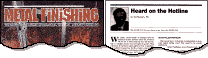
-----
Disadvantage of Electroplating in Powder Coating Vs. Advantage of Zinc Phosphating in Powder coating
Sir,
We are in the process of Powder Coating on a Low Carbon steel OR CRCA steel (Cold Rolled Cold Annealed Steel) which is Electroplated (Zinc plating with Yellow passivation). Of course, the material is manufactured by one of the Global manufacturers of Industrial Powders. The electroplated sheet metal part is Chromatized before Coating.
The major problem we face is due to the Pin holes after Powder coating and baking at 180 °C. The area of sheet metal (CRCA) is 1300mm (L) x 70mm. with a sheet thickness of 2mm.
The Powder coating thickness is around 60 microns.
Kindly answer the following questions for me at the earliest:
a) What is the Technical reason for Pin holes/ bubbles after baking.
b) What is the effect of Electroplating on this?
c) What is the advantage of Zinc Phosphating over Plating to overcome this problem?
d) What parameters should be followed if we opt for Zinc Phosphating?
e) What is the effect of Powder quality on this?
f) What is the role of Zinc Phosphating in preventing Corrosion?
Please answer!
P.R.SHESHADRI- Bangalore, Karnataka, India
Phosphatizing is cheaper than zinc plating plus chromating, and it may be good enough for your application; but it is far from being the equal of zinc plating, which is a true sacrificial coating which will protect the product from rust despite scratches and abrasions in the powder coating.
I cannot advise on the pinhole problem from this distance; hopefully someone else can though.
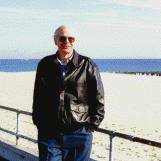
Ted Mooney, P.E.
Striving to live Aloha
finishing.com - Pine Beach, New Jersey
![]() |
Dear Mr. Seshadri, a) Pin holes, bubbles could appear on either zinc plated or phosphated parts if your reprocessed powder is mixed with fresh powder. Never use a mixture of RP powder as you will loose your good powder as well. There is no way the pretreatment either zinc plate or phosphate is responsible. b) Zinc plating should be mildly phosphated to turn black , then dried, then powder coated in my opinion. It is possible to also powder coat parts very successfully directly on zinc yellow or blue passivate, by lightly emerying the surface of the zinc plate prior to powder coating. However see 'a' as above. c) Zinc phosphating has no advantage other than cost saving. It is inferior as a coating per se vis a vis zinc plating. In my opinion zinc plating, with a mild phosphate is best. d) What parameters do you mean ? Ask your phosphate supplier you support you on this. e) Powder coating quality will depend upon how well you cope with either of the pretreatments. It is for you to manage and cannot be judged from the outside. f) Very vital. However for your powder coating application, it is more for the bonding that is vital. If you are looking for corrosion protection, choose plating. Regards, ![]() Khozem Vahaanwala Saify Ind ![]() Bengaluru, Karnataka, India ![]() Mr. SHESHADRI, You ask a lot of questions which cannot be answered in just one or two sentences. Nevertheless some hints to overcome your problem: a: The problems you describe look like degassing and this normally occurs only at hot dip galvanized objects and not at electrolytic zinc-ed ones. Try to give the products a preheat treatment before powder coating. Approx. 15 mins @ 200 °C. Apply the powder immediately after complete cooling down and treat the powder as usual. If the problem is gone you have two options 1: do it always like this (probably not practical because of increasing costs and decreasing production) or 2: talk with your powder supplier who can supply powder with degassing agents. b: Some platers rinse the parts after the passivation with a "dewatering" solution (sorry I don't know the English expression, (Editor's Note: possibly "Rinse Aid", an additive to lower the surface tension of the rinse water so more water drips from the work after removal from the tank) but your plater should recognize this). Ask him if he changed anything, or did you change the plater? Best regards, ![]() Remmelt Bosklopper - Enschede, The Netherlands |
Dear Sir,
Our company also have the same problem. But our surface treatment is Hot-Dip zinc before powder coating. We found that there are so many pin-hole after the coating.
We have done the pre-heat before the coating. But the problem is still staying. Anyone have idea how to overcome the problems, please? We also tried to sand-blast before
rinsing and pre-heat.
Thanks for any answer.
- Hong Kong, China
Q, A, or Comment on THIS thread -or- Start a NEW Thread