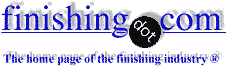
-----
Standards for Hydrogen Embrittlement Relief after Zinc Plating
Q. Does ASTM A572 Grade 50 material need to be baked after Acid Zinc/Nickel electroplating. If it does, at what temperature and for how long?
Richard Comp- Greensboro North Carolina
September 1, 2021
A. Hi Richard. In the case of zinc plating per ASTM B633, the spec dictates what requires baking. I'm not sure what spec you are doing acid Zn-Ni in compliance with, but it may well tell you what needs embrittlement relief baking.
ASTM A572 Grade 50 is only 73 ksi ultimate strength / 50 ksi yield point (that's what the 'Grade 50' means), so I would be very surprised if any spec required baking for such a mild steel.
Luck & Regards,
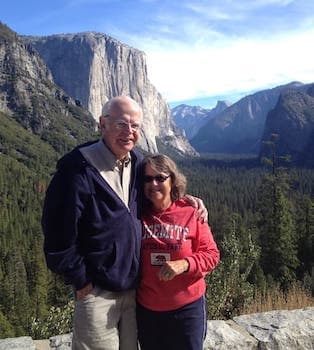
Ted Mooney, P.E. RET
Striving to live Aloha
finishing.com - Pine Beach, New Jersey
⇩ Related postings, oldest first ⇩
Q. I am a small metal stamping job shop. We sent some steel parts (SAE1050) to our heat treater and plater (zinc & bake). The parts failed in service. Our customer is claiming our plater didn't bake them right. The plater has told me what he did, but I have no idea how to evaluate if it's right or within any applicable standards or rules of thumb.
Is there a standard for how long and at what temperature parts should be "baked" after zinc plating?
Is there such a thing as "standard commercial zinc & bake"?
Thanks in advance.
Michael Wagner- Toronto, Ontario, Canada
2002
![]() |
A. What did your PO state in the ordering documents? Did you indicate that the parts require baking? Different specs require different bake cycles and more importantly different delays following baking to the start of baking. The more critical the application and the more prone the parts are to embrittlement, the shorter this delay becomes. For many aerospace applications on hardened steels, above Rockwell C 36 hardness, this delay becomes 30 minutes. For most applications, commercial for instance, this becomes 4 hours. A conventional callout for baking parts following plating is: 375± 25 degrees F for 3 hours minimum within 4 hours of plating. For springs and parts that are subject to flexure or extreme loading, often this bake is extended to 8 hours or up to 24 hours in some cases. Most platers have baking charts and baking records that can be produced as objective evidence of baking the job. Check closely when the parts came out of plating and when they were at temperature ( should be less than 4 hours ). Failures of platers to bake parts properly or at all usually stems from lacking of citing a proper specification in the ordering document or not giving the plater enough information to indicate that the parts require baking. As Chairman of ASTM B8's subcommittee on coating pre- & post-treatment, I have seen and heard of many such problems. Operating a specification plating shop myself and having worked in the industry for thirty years, I've seen it all. Communications is key! ![]() Milt Stevenson, Jr. Syracuse, New York 2002 A. How do you know that it was an aspect of the plating that caused the service failures? Consider the possibility that there was a design deficiency, or that your client specified an inappropriate material, and hence the parts might have failed even if they had never been plated. ![]() Bill Reynolds [deceased] consultant metallurgist - Ballarat, Victoria, Australia We sadly relate the news that Bill passed away on Jan. 29, 2010. 2002 |
2002
Q. "What did your PO state in the ordering documents? Did you indicate that the parts require baking?" It said zinc and bake.
"For many aerospace applications on hardened steels, above Rockwell C 36 hardness, this delay becomes 30 minutes. For most applications, commercial for instance, this becomes 4 hours." It's not an aerospace application, but it was 1050 heat treated to midrange for 1050 (Rc 39-43)
"A conventional callout for baking parts following plating is: 375± 25 °F for 3 hours minimum within 4 hours of plating." We are subcontract manufacturers. We stamp the parts according to the designers specs and handle post-processing according to the designers specs. In this case, the spec was "zinc & bake". Is there a "standard" interpretation for such a specification? Can the question "did our plater act within that spec" be answered meaningfully?
"Most platers have baking charts and baking records that can be produced as objective evidence of baking the job." Thanks. I'll follow up on that.
"How do you know that it was an aspect of the plating that caused the service failures?" Two independent labs analyzed a few failed parts. One said the parts were clearly underbaked for this application. The other said either they were underbaked or overbaked. Neither really addresses whether what was done to the parts falls within industry standard practice for a simple "zinc & bake" specification.
"Consider the possibility that there was a design deficiency, or that your client specified an inappropriate material, and hence the parts might have failed even if they had never been plated." I have tried to explain to our client that this was his responsibility to specify tighter if the parts were sensitive to this processing, but it's been tough sledding.
Thanks for your feedback, and I await more information.
Michael Wagner- Toronto, Ontario, Canada
A. I think the specification you are looking for is ASTM B633. There are others. The spec states "All electroplated parts 1200 MPa or higher shall be baked at 190 °C for 3 hours or more within 4 hours after electroplating.
Several other issues to consider:
1) Baking times should start when the center of the furnace load reaches temperature, not when the furnace does. This can be a huge issue if the load size is large.
2) Embrittlement can be created during service if the parts experience a galvanic couple or electrolysis.
3) I have yet to see any evidence of over baking (related to time at the proper temperature) causing embrittlement. If the lab is using the term over baking to define temper embrittlement, this is an entirely different issue. One that has nothing to due with hydrogen embrittlement.
4) If you have to use this plating company, visit the facility and walk through the process. Observe times, attention to requirements, furnace charts, etc.
Matthew Horton- St. Paul, Minnesota
2002
A. Hi Michael. Matthew has offered sound advice. A serious problem here is that "zinc & bake" is nothing close to an adequate specification. You can't order processing of a critical part with 3 syllables ... you can't even order a sandwich.
Still, once the plater was alerted that baking was required, "proper" baking to ameliorate hydrogen embrittlement was clearly implied, and most if not all of the onus for lack of communication was shifted to him.
Regards,
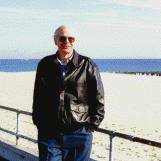
Ted Mooney, P.E.
Striving to live Aloha
finishing.com - Pine Beach, New Jersey
Q. What time and temperature for hydrogen embrittlement process on zinc plated spring steel component ?
Thank You
With Regards
plating and paintshop - India
February 17, 2009
A. Hi, cousin Sanjay. Milt already answered that on this page, and by reference to ASTM B633, Matthew did as well. But please rely only on the primary specification, not on internet postings :-)
Good luck!
Regards,
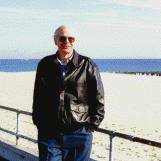
Ted Mooney, P.E.
Striving to live Aloha
finishing.com - Pine Beach, New Jersey
February 17, 2009
Q. The ASTM B633 makes reference to parts having an MPa 1200 is there a standard for zinc plating on C1022 carbon steel that has lower MPa
Douglas Holmberg- Concord, California, USA
June 25, 2009
A. Hi Douglas. I may be misunderstanding your question, but ASTM B633 fully applies to lower strength carbon steels. I think the issue may be that hydrogen embrittlement relief is not required for low strength (softer) steels, and someone might be misreading a statement about that.
Regards,
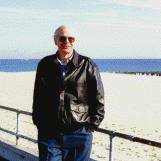
Ted Mooney, P.E.
Striving to live Aloha
finishing.com - Pine Beach, New Jersey
Q, A, or Comment on THIS thread -or- Start a NEW Thread