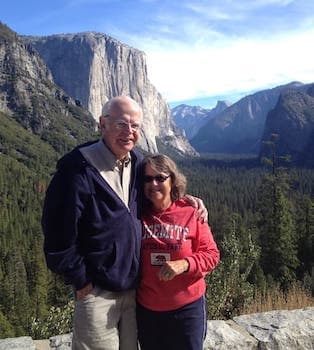
Curated with aloha by
Ted Mooney, P.E. RET
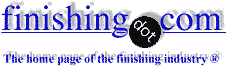
The authoritative public forum
for Metal Finishing 1989-2025
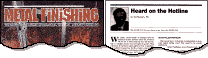
-----
Plasma Nitriding
Q. I would like to have information about plasma nitriding for surface hardening of automotive parts and screws and barrels of extruders.
1. How successful is this technology?
2. Is it economically feasible to set up this plant, how much can be the cost of the required equipment/s.
3. Does it have an advantage over traditional methods of nitriding( technical and economic feasibility).
Thanks,
Varun Kapoor- New Delhi
A. Varun, it sure sounds like you want to talk to a manufacturer of the equipment, a user of the equipment, or a heat treating consultant. If you're serious about plasma nitriding, you realize it is not inexpensive. It can work very well, especially for large numbers of similar parts, which would justify the tooling needed. Yet plasma nitriding has many quirks, not the least of which is the necessity for a uniform plasma field. I believe you would be wise to hire a good consultant.

Lee Gearhart
metallurgist - E. Aurora, New York
----
Editor's Note: Please visit our
Consultants Directory.
A. Yes,
all above items are most suited for plasma nitriding. We know from our own experience that this has become a hot topic in India.
- Weingarten, Germany
Q. Hello, I am a product engineer in Auto ancillary manufacturing unit. I would like to know the process of Plasma Nitriding, which is said to give wear resistance. Is there any difference between salt bath nitriding and plasma nitriding?
Thanks,
SENTHILKUMAR- CHENNAI, TAMILNADU, INDIA
2003
by John F. O'Hanlon
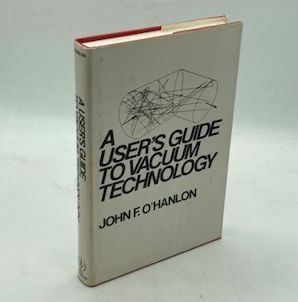
on AbeBooks
or eBay or
Amazon
(affil links)
A. There is a very major difference between salt bath nitriding and plasma nitriding. In salt bath nitriding, the component(s) are placed in a molten salt bath and the entire component it heated to get a hard nitride layer on the surface. In plasma nitriding the nitride ion is bombarded on the component at much lower temperature to achieve the same end. The component is not heated to the same extent. The hardening is more uniform and the depth can be controlled to much better accuracies. The equipment is exponentially expensive and since the coating is done in a vacuum chamber, you cannot do it on all components economically. Typically, this is done by job coaters only since a single industrial entity is not able to justify the investment for in-house production.
Gurvin SinghMohali, Punjab, India
2003
A. Hi Gurvin,
As a person intimately associated with development of plasma nitriding process and its varied applications for the past 20 years, I must beg to differ.
More and more companies are looking at having their own plasma nitriding systems to cut down on time wasted in sending, processing, receiving their tools, toolings and components. It is likely that this trend may see ten to twelve nitriders installed in-house by leading companies before we ring out this year.
It is heartening to see many drawings now having "to be plasma nitrided" instructions stamped on them. A huge wave of adoption seems to have got activated by the auto ancillary industries.
Thanks for explaining the process so well in brief.
Cheers!
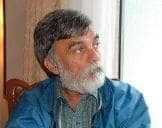
Max Babi [deceased]
- Chennai, Tamil Nadu, India
(with great sadness we acknowledge the passing of the great
Sir Max [Mushtaque Ali Khan Babi] on March 15, 2015)
2005
Q. Respected Sir,
I am student of Tarbiat Modares University of Iran(tmu) doing project of plasma NITRIDING OF H11 STEELS
So sir please send me some notes and how to establish the process.
Thanking you sir, waiting for your mail.
student - Tehran, Iran
September 7, 2008
A. Dear Sir
H11 material is suitable for Plasma Ion Nitriding
We do usually 250 Microns depth and we will achieve 1200 Hv at 100 g load
It is the best process for hot forging application.
- Tamil Nadu, India
February 7, 2012
Q. Dear Sir
I am Material Science Engineering now graduate for master's degree, and working in plasma lab in the University the equipment available, DC power supply (5kV, 2.5A) commercial magnitron (2.45GHz,700W) I generate plasma by two sources. My question (for my research) How to make nitriding process by these equipment and what is the best DC or MW).
Thank you with my best regards
Hesham E. Aboryana- Tripoli, Libya
2003
Q. Respected Sir(s),
I am attached with the Liquid Nitriding process in Kolkata for about 12 years. Now I am hereby requesting to be provided the detail of Plasma Nitriding, its cost effectiveness over liquid nitriding, and the minimum cost of establishment.
Regards,
consultants - Kolkata
October 2, 2012
Q. Sir,
I am a supervision engineer, having 14 stages of firm's production. My company produces blades of crop cutting threshers, and reapers. To avoid rust on blades (of 0.8% carbon, manganese, silicon, sulfur, phosphorus composition) we dip them into hot molten state sodium nitrate
⇦ this on
Amazon [affil link]
at 560-570 °C. So, please explain to me other alternate solution to get the result at 250-300 °C.
Thanking you, yours faithfully,
- ludhiana, Punjab, India
June 1, 2014
A. Hi Sandeep. It sounds to me like you are presently doing a salt bath nitriding process. Corrosion resistance is not the only object of this operation; it is also intended to provide hardening. If you only want corrosion proofing, there are many low temperature processes available to you, but you cannot achieve the hardening by simply dipping at lower temperature.
You can, however, obtain similar results by plasma nitriding -- so we appended your inquiry to a thread on that topic. Good luck.
Regards,
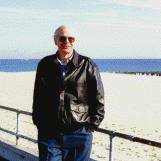
Ted Mooney, P.E.
Striving to live Aloha
finishing.com - Pine Beach, New Jersey
June 2014
Q, A, or Comment on THIS thread -or- Start a NEW Thread