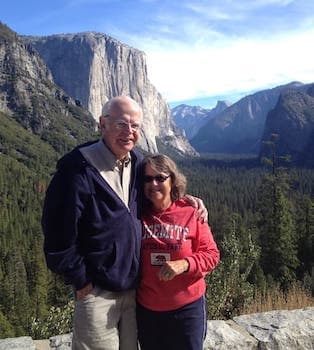
Curated with aloha by
Ted Mooney, P.E. RET
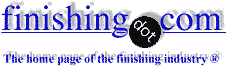
The authoritative public forum
for Metal Finishing 1989-2025
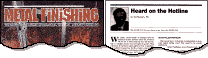
-----
Mirror finish on die-cast aluminium
Hi,
Would appreciate if someone can advise me on a suitable plating process/type to achieve a mirror like finish on A380 alloy die-cast aluminium. Currently I'm sampling polish vacuum cast part which are almost mirror-like (without visible defects) but end up with poor finishing after nickel or tin nickel plating. Please advise on a suitable solution and company if possible.
Thanks,
S H Wong- Singapore
--
Ed. note: You may want to hear
"The Lost Art of Tin-Nickel Plating".
I would certainly expect that you could nickel-chrome plate these parts if that's what you are looking for.
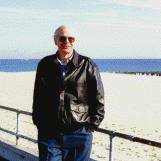
Ted Mooney, P.E.
Striving to live Aloha
finishing.com - Pine Beach, New Jersey
I have tried nickel-chrome without much success. The main issue that I faced is that shiny (not mirror-like yet) smooth surface cast part end up being filled with voids and flow marks after plating.
My guess is that cleaning process before the plating somehow etched away my top surface revealing the porosity below. Cast-parts by nature contains extensive porosity below the 'skin' and I'm looking for a plater who can recommend a plating process that remove of little my casting surface.
I might be wrong in my guess but something, I'm sure, during the plating process is creating defects on the polish cast parts.
SH Wong- Singapore
You might try putting on .0005-.001" of copper then polish then go to your nickel plate. This should help fill in any porosity but might not be cost effective. We plate heavy EN for diamond turning of optics and castings are definitely a poor substrate. What is your pre-treatment cycle?
Rick Richardson, MSFDayton, Ohio
Dear Mr Wong,
The concern of platers is with Adhesion of plating , hence it is possible that the plater is using Anodic/ Cathodic/ or strong solvents to clean the component. This has every possibility of penetrating the skin and exposing the defects you are seeing. My advice would be to go for only a soak cleaning in a fresh bath, in a non silicated cleaner, followed by hot water rinsing, double zincating and plating.
This above process will not damage your mirror finished parts.
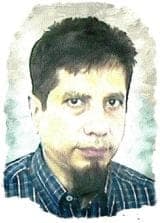
Khozem Vahaanwala
Saify Ind

Bengaluru, Karnataka, India
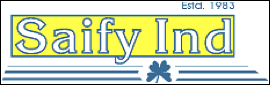
Nil, if you are talking about pre-treatment like heat stress relief. The part is vacuum cast to reduce porosity. And go straight to polishing and plate.
SH Wong- Singapore
Mr Wong,
After reading the above Msg.. I assume you want to maintain the original finished surface after plating..
When plating Aluminium Alloy casting without change to the original finished surface is tough..
Heat check, flow lines, patches are common with parts without further polishing.
For good adhesion etching is a must. which will bring out the flaws you are seeing after plating.
Maybe you can look into the whole manufacturing process flow to solve your problem.
Good Luck..
Jimmy Goh- S'pore
Hi Guys,
Still seeing some quality issues with the parts surface finish but things have improved markedly. Special thanks especially to Mr. Khozem Vahaanwala whose advice I tried and seen some of the greatest improvements. Thanks again and please do advise me further if you guys have any more ideas.
Thanks.
SH Wong- Singapore
Hi,
I know it's quite a bit after you posted your question but if you've still not achieved satisfaction, have you tried a company called "Alumiplate"?
Jeff Blythin- UK
Q, A, or Comment on THIS thread -or- Start a NEW Thread