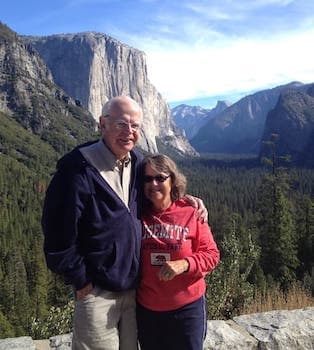
Curated with aloha by
Ted Mooney, P.E. RET
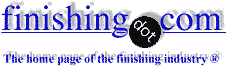
The authoritative public forum
for Metal Finishing 1989-2025
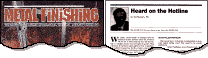
-----
Sulfamate Nickel Strike Help Needed
Q. Need advice on Nickel Sulfamate Strike solution. Experiencing frustrating problems maintaining pH under 1.5 per our specification. Either Sulfamic acid or HCl are recommended by specification to lower pH. We have added as much HCl as allowable without exceeding the Cl- limit for the strike bath. Large and very frequent adds of Sulfamic Acid are required and we are forming excessive amounts of Nickel sulphate crystal. This crystal is plugging filters, pumps and generally making a mess of the bath.
It appears that we are driving a hydrolysis reaction(?) due to low pH and temperature (bath at 120-125 °F).
We are performing Nickel Sulfamate Flash Plating prior to nickel brazing for a variety of Nickel and Nickel Cobalt aerospace alloys (controlling specification AMS2403 / AMS2424). We switched to use of a Nickel Sulfamate Strike from a Wood's Nickel Strike in the interest of reducing the number of rinse tanks needed in a newly installed processing line.
Our strike bath make-up is;
50% by volume Nickel Sulfamate solution (20 oz./gal. Ni)
4 oz./gal. Boric Acid
1.54 fl. oz./gal HCl
2.7 oz./gal sulfamic acid
⇦ this on
eBay
or
Amazon [affil links]
We currently maintain our bath at;
10-12 oz. wt./gal Ni
4 oz./gal minimum Boric
0.4-1.0 fl. oz./gal Chloride (as Cl)
pH 1.5 Maximum though it frequently creeps up to 1.9
(We experience activation problems at this level)
We are using Nickel S Rounds in double bagged titanium baskets. Our Anode area is constant and cathode area varies with load size but Anode to Cathode ratio is approx. 2 to 1 or higher. Also, it has been noted that sulphate crystal has formed in the interstitial space between S-rounds in the basket and may in fact be reducing anode surface area by "masking" or blocking.
We strike @ at CD of .208 to .313 amps per square inch of load surface area. with rectifier settings to nominal .260 asi. We are in strike bath for approx. 1-3 minutes.
Does anyone else use a Sulfamate Nickel Strike? Can you maintain a low pH? Do you have problems with formation of crystalline compounds? How can we limit or eliminate this problem?
Brent Pettegrow- North Berwick, Maine
A. Using nickel sulfamate in a hot, low pH solution results in a fast hydrolysis of the sulfamate ion to produce both sulphate and ammonium ion. Further, the ammonium ion is reacting with the nickel sulphate to produce nickel ammonium sulphate (or double nickel salts or DNS) that has rather low solubility. The anode efficiency is close to 100% resulting in a localized high concentration of nickel within the anode baskets. The result of both of these reactions may be twofold; 1) the crystallization of nickel sulphate within the basket as a result of the high-Ni/low-pH conditions and 2) the likely possibility of crystallization of DNS salts. The double bagging is probably exacerbating the problem by reducing solution flow in/out of the basket. If the crystals within the basket are dark green, then they are probably nickel sulphate, if a light green then they are probably DNS, if they are yellow then anhydrous nickel sulphate is being formed which is almost insoluble. I'm not aware of any simple procedure that will remove ammonium ion.
The use of nickel sulfamate under these conditions is a waste since the bath is producing ammonium and sulphate rather quickly. Substituting nickel sulphate for the nickel sulfamate would do just as well and eliminate the ammonium problem. Unfortunately, it will be necessary to replace the bath.
Lou GianelosRetired - Eastlake, Ohio
Q. The hydrolysis reaction is what I suspected. X-ray Diffraction confirms that most of the crystalline compound we are forming is Nickel sulphate crystal.
I have heard numerous references here and elsewhere to Nickel Sulfamate Strike solutions as an alternative to Woods Strike. Since the hydrolysis reaction appears inevitable with this chemistry at this pH, what is the secret to it work and minimizing the tendency for this hydrolysis reaction and the dealing with the continual rise in pH? Any experience from users of this strike bath would be helpful. Are other formulations and operating conditions (temperature, pH) recommended? more successful?
Brent Pettegrow [returning]- N. Berwick, Maine
A. I am not aware of a sulfamate type strike as a replacement for a Woods nickel strike. I understand that it is used, however, as a strike when operated at pH > 3 in place of Watts types in order to take advantage of lower stress but at the low thicknesses used I fail to see where stress can be a factor and ductility from either bath is good.
What are the requirements for your strike bath, eg, why must the chloride be low? Why can't a low pH, say 2.5, Watts strike be used? Say preceded by a reverse sulfuric acid to activate the Ni/Co/Ni-Co alloy. A Woods strike IS the best procedure to use but apparently your rinsing needs to be improved. Why not install spray rinses over your existing rinse tank(s) to beef up rinsing?
Lou GianelosRetired - Eastlake, Ohio, USA
Q. The trade literature I have in file (old, ca. early 1980s) from BARRETT reflects use of this strike bath with the following operating conditions;
Solution Temperature 80F-100 °F
pH 1.5 Max.
Cathode Current Density 10-100A/ft2
Strike Time 30-60 Secs.
Cathode Efficiency 50%-60%
Anode to Cathode Ratio 1:1
A similar trade literature specification (ca. 1985) from M&T Chemicals is roughly the same with pH listed at 1.5-2.0.
The listed advantages of use of BARRETT sulfamate strike vs. Woods include; "less hydrogen embrittlement better adhesion of subsequent coating, Higher Cathode efficiency (50%-60% vs 7%-9%), parts can be transferred without any intermediary steps to a nickel sulfamate bath, less corrosive, easier to purify, can be used for barrel plating, can be used to strike multimetal parts, not limited to use of nickel bar anodes; can use less expensive S-Rounds in titanium baskets."
Can anyone with experience in use of this bath shed additional light on whether the problems we are experiencing with pH and crystallization are normal and inherent in this bath and if not what can be done to minimize the problem. Any BARRETT sulfamate nickel strike users out there?
Brent Pettegrow [returning]- North Berwick, Maine
A. We switched from Wood's Nickel Strike to Sulfamate at November 1996. We use the same spec as you, as I guess, but we never had the problem you describe. The only difference I can see is the operating temp. We use 80-100 °F as you mention in old BARRETT spec instead of 120-125 °F you are using. Also we use only one bag per anode, and the process time in our strike bath is 4 minutes instead of 1-3 in yours.
By the way, all of the benefits you mentioned about sulfamate strike are absolutely true and they were the reason for us to covert from Wood's to sulfamate. If you have any additional questions, re-contact.
Good luck,
Alex Sirota- Lod, Israel
adv.
"The Sulfamate Nickel How-To Guide"
by David Crotty, PhD
& Robert Probert
published Oct. 2018
$89 plus shipping
Q, A, or Comment on THIS thread -or- Start a NEW Thread