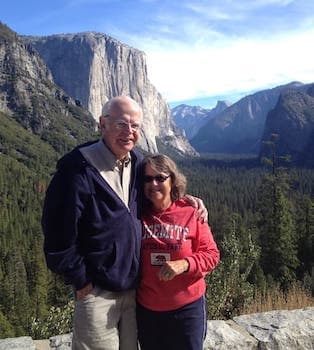
Curated with aloha by
Ted Mooney, P.E. RET
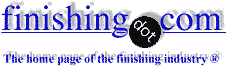
The authoritative public forum
for Metal Finishing 1989-2025
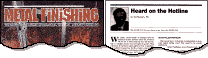
-----
PAINTING OVER HOT DIP GALVANIZE
WE HOT DIP OR MECHANICAL GALVANIZE SCREW PINS FOR OUR LIFTING SHACKLES. WE THEN PAINT THE PINS OUR TRADEMARK COLOR. WE HAVE A VERY DIFFICULT TIME GETTING THE PAINT TO STICK TO THE ZINC. THESE ARE LARGE PRODUCTION LOTS CONSISTING OF SEVERAL THOUSAND PIECES. ANY SUGGESTIONS?
CHRIS HIGGINS- LONGVIEW, Texas
Chris,
The screw pins must be pretreated with zinc phosphate prior to painting. The part must be oil free and dry. Because of the climate there, you must consider the effect of condensate on the part. In other words, parts cannot be stored outside in the cold and painted without warming to about five degrees above the dewpoint temperature.
Since the part is galvanized, the phosphate stage of the process must also contain fluoride. The fluoride ion content must be carefully controlled and maintained.
Herb Ashley- Smartt, Tennessee
Chris, you did not mention anything about chemically treating the parts before painting so I'm assuming that your are not doing that currently. Zinc surfaces tend to develop a oxide layer rapidly after the coating process. This oxide layer results in poor paint adhesion. Using a wash type primer or chemically pretreating the parts before painting will improve the paint adhesion by removing the oxide layer and replacing it with a conversion coating. Zinc phosphating would provide the best performance from a pretreatment standpoint.
Roy NussTrevose, Pennsylvania, USA
When you use the term "Zinc Phosphate" as a pretreatment, are you referring to Commercial Phosphoric Acid Pretreatments? (e.g. PPG's DX520SG Metal Conditioner)
It is my understanding that oils must be removed prior to etching. How can you determine if there is an oil on the surface? Is this oil applied to the surface for some reason or does it have something to do with the galvanizing process? I don't know of any more misundertood or recurring problem in the painting industry.
Thanks for your help.
Sincerely,
Patrick Chism- San Diego, California, USA
Patrick,
The zinc phosphate process is an alkaline clean, rinse, and acidic zinc phosphate pretreatment process. Oil must be removed prior to the zinc phosphate pretreatment. There are rinses involved. Several chemicals are used and generally are metered into the solution tanks with metering pumps.
The process may be conveyorized with a shroud above holding tanks, or dip tanks may be used. The part and production speed requirement will determine the type of system.
One conveyor system in the midwest processes refrigerators at a speed of 50 ft./min. Parts are usually processed at 12-24 ft./min.
Herb Ashley- Smartt, Tennessee
Another way to attack the problem is using Chromate Conversion pretreatment, before painting. From my experience it is superior on Zinc phosphate and easier to maintain and apply, and at the end the quality results are better than Zinc Phosphate.
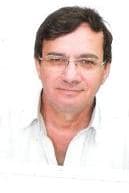
Yehuda Blau
YB Plating Engineering and Quality - Haifa Israel
Q, A, or Comment on THIS thread -or- Start a NEW Thread