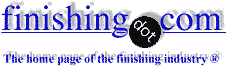
-----
Hard anodizing problem, aluminum alloy
Our company trying hard anodizing of 2219 T6 aluminum alloy. Our bath concentration is 250-280 H2SO4,at -3--5 C,with titanium rack, but every time one part is burning ,our voltage increase to 27 volt in 20-25 minutes then stopping increase of voltage then burning. We are using NaOH (40-50 gr/lt) then %12 nitric acid neutralization, we tried many things, but result is same, burning or low coating thickness. Thickness is wanted 13-60 micron, if you help me, it will be pleasure.
Sincerely
Ida- Turkey
First of two simultaneous responses --
How many amps /dmÄ did you place on you work piece?
Andy Dhaen- Brussels
Second of two simultaneous responses --
Dear Ida,
2000 series alloy's are more difficult to do to start with. Based on what you have said your starting with three strikes before you get to the plate. Or your behind 3 goals in football before the game starts.
1)Your acid concentration should be between 180 and 200 grams per liter
2) use aluminum racks Very important
3) lower temp to -2c to 0c or 30-32f
4) try to eliminate etching before anodizing
5) turn up the agitation
6) 10 minute ramp
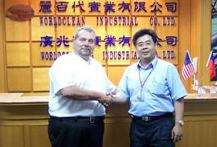
Drew Nosti, CEF
Anodize USA

Ladson, South Carolina
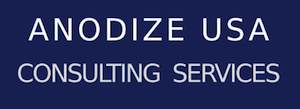
Andy Dhaen;
Firstly, I want to thanks answer my question, I am searching and trying many things, changing amp/dm2(1-3)generally 2 amp/dm2, changing concentration bath(lower acid concentration), changing rack(using aluminum rack) and temperature, I also tried without etching, but result is same, burning and too high thickness or too low thickness.
Ida- Turkey
Ida,
Can you describe the form of the workpiece, and where is your contact point or points?
Andy D'Haen- Brussels
Mr Nosti's advice was excellent. Do it. Except for one thing, all copper bearing alloys anodize better at higher acid concentration (but not quite as high as yours), so bring the acid down to 225 gm/L. Repeat 225!
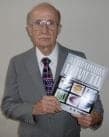
Robert H Probert
Robert H Probert Technical Services

Garner, North Carolina
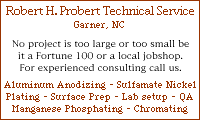
Use oxalic acid concentration 12 g/l.
Moshe Yaakov- Lod, Israel
Q, A, or Comment on THIS thread -or- Start a NEW Thread