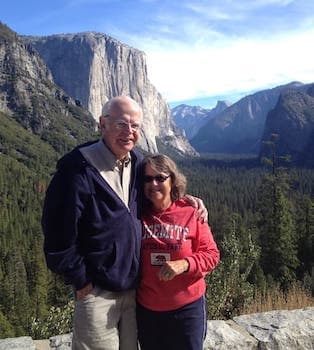
Curated with aloha by
Ted Mooney, P.E. RET
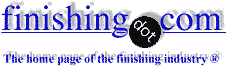
The authoritative public forum
for Metal Finishing 1989-2025
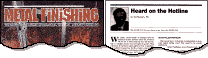
-----
O-ring seal on hard coat anodize
I use a hard coat anodized aluminum as a wear surface for a piston. The piston uses an o-ring as a seal for hydrogen. This is a dynamic seal. At cold temperatures(-40 F) the seal will leak. It appears that the pores and irregularities in the hard coat act as a leak path. Is there a way to solve this problem.
Thanks,
Tom Bydalek- Elk River, Minnesota
That is a possibility for H2 and even a probability for He, but I suspect that you have a coefficient of thermal expansion problem. Check it out for the piston, the cylinder and the O ring material. Teflon is about 10 times that of steel and aluminum is not the same as steel by a significant amount when you are talking about +70 to -40. At 40 below, we expected our aircraft seals to leak hydraulic fluid and that is a massive molecule compared to H2.
James Watts- Navarre, Florida
Polishing or honing either before and/or after hardcoating will smooth the surface.
Chris Jurey, Past-President IHAALuke Engineering & Mfg. Co. Inc.

Wadsworth, Ohio
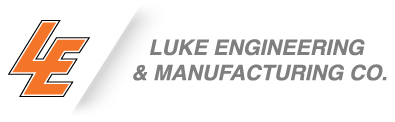
Tom,
Most O-ring surfaces are masked, prior to hardcoat for the same reason you are experiencing. A typical O-ring surface will have an Ra of 16 or better, while most hardcoats raise that # to 24+. It is possible to polish the hardcoat surface to a lower Ra #. Either way..masking or polishing..you are probably going to experience an increase in cost to your product.
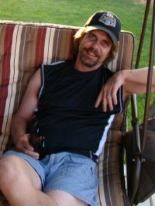
Marc Green
anodizer - Boise, Idaho
Masking off the area sounds like the best solution. This area could then be chromated for protection if necessary.
Keith Rosenblumplating shop - St. Paul, Minnesota
Thanks for the responses.
I need this hard anodize for wear purposes and to prevent galling of the piston in the bore. I have made this design work with electroless nickel plating but one customer will not accept this due to the risk of hydrogen embrittlement of the nickel.
I will look at honing to see if this is an option. I sectioned this part and noticed that the anodizing has some grain structure(direction) to it. The direction is opposite my machined(turned) finish. Would this be a function of the bar stock grain or the direction of current when anodizing. If I could control the direction of this grain it might help.
All help is appreciated.
Thanks,
Tom Bydalek- Elk River, Minnesota
Tom,
The grain structure you are seeing is coming from the aluminum itself.. this has been a problem for me also, albeit in a different application where I had to meet a certain Ra spec after coating, and was dealing with some aluminum that had a particularly large grain structure (this seems to be a manufacturing issue with plate aluminum, towards the middle of the plate, in larger thicknesses) Anodizing pretty much mimics the alloy, and surface, that's being coated, as it is "grown" rather than deposited. I posted a similar question on here, myself, a couple of months or so ago...but didn't get any advice. I wonder, though ... since you are manufacturing pistons ... aren't you using round stock? I have not come across this problem in the parts we manufacture out of round stock, just plate. I hesitate to recommend an Al supplier.. but we have found that Alcoa products tend to be more consistent than other Al manufacturers.
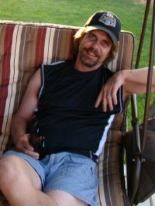
Marc Green
anodizer - Boise, Idaho
Q, A, or Comment on THIS thread -or- Start a NEW Thread