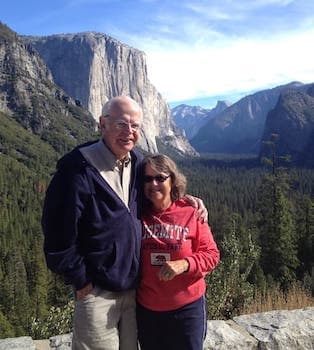
Curated with aloha by
Ted Mooney, P.E. RET
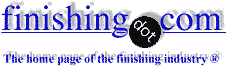
The authoritative public forum
for Metal Finishing 1989-2025
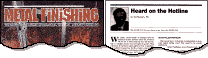
-----
Corrosion resistance of zinc on steel
Can somebody help? Which gives the better corrosion resistance on steel screws, given that the same thickness of plating is applied: Zinc plated and clear passivated or zinc plated and chromate conversion (colour passivated)? Is the difference substantial or marginal? Any date would be of great help.
Thank you for your help.
Arnie Gobel- London, United Kingdom
![]() |
Clear passivation will give you 12 hours to white corrosion but colored or yellow chromate should at least reach 48 hours or 72 hours to WC if the thicknesses are the same. ![]() Cliff Roy plating shop - Conestee, South Carolina 2002 Firstly you have to decide which kind of finish you require that is clear or colour chromate but the best corrosion resistance you get in olive green passivation. Then comes yellow passivation on zinc, again we all know that clear passivation gives the least corrosion resistance but if your requirement is same it can be increased by a topcoat of organic coatings which will increase corrosion ressistance also enhancing the same finish. ![]() Praveen Kumar plating process supplier Mumbai, India 2002 |
2002
The yellow hexavalent chromates over zinc plating offer substantially greater resistance to white rust than the clear chromates. I believe the rule of thumb is 96 hours salt spray to white rust for the yellow hexavalent chromium and 24 for the clear trivalent chromium (see the MFSA's 'Quality Metal Finishing Guide' to Zinc and Cadmium finishes).
But there is a whole 'nother issue here in that the world is rapidly moving away from hexavalent chromate finishes due in good part to European Parliament rules. What you really need is probably a modern proprietary system that will give you the corrosion resistance of the yellow chromate without the yellow chromate.
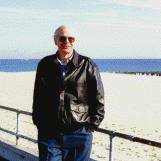
Ted Mooney, P.E.
Striving to live Aloha
finishing.com - Pine Beach, New Jersey
----
Ed. note: The above replies predate the widespread use of modern high corrosion resistance, RoHS compatible, trivalent chromates.
Hi
Do any of you buddies know if it might be a problem to use heavy dipped galvanized nuts on a zinc and clear coated bolt
I will be installing them in a harsh climate kazakhstan temps -45 °C to +50 °C in a petrochemical plant
any comment would be appreciated thanks
Derek
- Atyrau, Kazakhstan
October 4, 2008
October 12, 2008
Hi, Derek. Electrochemically they will be compatible, but it probably won't work because the threads won't fit properly. I believe that galvanized nuts will not run on a zinc plated bolt.
Regards,
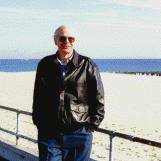
Ted Mooney, P.E.
Striving to live Aloha
finishing.com - Pine Beach, New Jersey
Q, A, or Comment on THIS thread -or- Start a NEW Thread