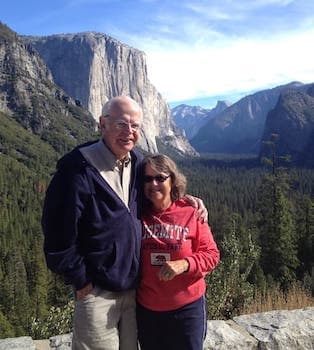
Curated with aloha by
Ted Mooney, P.E. RET
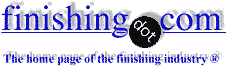
The authoritative public forum
for Metal Finishing 1989-2025
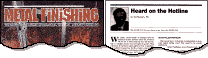
-----
High Friction Coating Material
Q. Dear Sirs:
I am looking for a material with a high friction coefficient, a low wear rate, high temperature resistance. I am thinking about a fluororesin with some fillers. The material will be deposited on a metal surface.
Can anybody help me?
Charo Fernandez- Spain
2002
A. Not sure how high the temp you have in mind. Electro nickel plated diamond will give you a finish of diamond file. Or thermo-spray, say chromium oxide with appropriate grade of powder. Need more details of your requirement.
CC Chaw- Hong Kong
2002
A. If you meant a low coefficient of friction, you can try a Teflon coating :-)
If you are looking for a high coefficient of friction you can try a plasma coating.
Suerte.
Jordi Pujol- Barcelona, Catalonia, Spain
2002
2002
Q. I also am looking for a high-friction coating. the requirements are as follows:
1. Thickness tolerance ± .0005
2. Applicable to stainless steel (304 or 316)
3. Electrically non-conducting (or at least 1000 times less conductive than copper) (note: voltage only ~3V)
4. Friction coefficient (f) at least .5 against an electrical steel (i.e. Fe + 2.5% Si) with yield stress 65 ksi.
5. Must transfer 3000 psi of shear stress
6. Normal force will be 3000/f times a safety factor (1.5?)
7. Purpose of friction is to lock parts together as part of an assembly procedure... during assembly parts need to be aligned to a high tolerance, but after assembly the parts should not move
8. Friction interface will be subject to a large number (100,000?) of load reversals during its lifetime ... the friction joint should not "walk", creep or chafe
9. Friction interface should be as stiff as possible both axially and in shear
10. Temperature of operation will be as high as 100 °C
- Waltham, Massachusetts
Multiple threads merged: please forgive chronology errors and repetition 🙂
Plating with high friction coefficient
Q. I am in search of a plating or coating to be used on carbon steel components. The plated component will have a high contact stress (20,000 to 30,0000 psi or more) interface with an uncoated carbon steel component. This interface needs to be an absolutely zero slip interface and requires as high a static coefficient of friction as possible without damaging the components. Does anyone have any suggestions?
Brent Harralddeepwater technology - Houston, Texas
2003
![]() |
A. With the very little info you give it is difficult, but I would say that the highest friction between two mating metal parts will be attained with both elements being of the same alloy. Molecular cohesion (same type of molecules) is normally higher than adhesion (different type). Alternatively, if the parts are intended to remain together you may think of adhesives instead of plating. Guillermo MarrufoMonterrey, NL, Mexico 2003 A. Try electroless nickel with co-deposited silicon carbide. Our firm sells it, however, there are others in the plating industry that sell equivalent. The electroplated nickel with silicon carbide coating, widely known as Nikasil, is also available. There are also combinations of diamond with electroless nickel, however, these tend to be pricey. ![]() Milt Stevenson, Jr. Syracuse, New York 2003 |
A. I suggest that you try belting the different alloys together with some sort of foreigner clamp. These products come with complete instructions, so nothing is left to the imagination. I bet you will experience vast improvements in outstanding performance. Good luck.
Errland Ignignotcomponents - Moon River, Arkansas
2003
A. I am working on a very similar problem for my company. Our compressive stress requirement is lower, 8,000 to 12,000 psi. I know of an application using tungsten carbide coating on carbon steel against non-coated carbon steel that is in the 10,000 to 12,000 psi range. It does not slip or damage the mating surfaces.
Michael Italiano- Salem, Ohio, USA
June 13, 2009
Q. I'm not sure what kind of material to use that has high friction force and no slip when rubbed together?
Samuel BensonBrunel - UK
February 4, 2010
Q. I am in need of a similar substance/process as Mr. Potter above. Basically I need a surface finish/treatment/film that will result in a coefficient of friction between two metal surfaces that is much greater than 1. The surfaces should be easily separable, but when a normal force is applied, they must not slip.
Any ideas or leads?
- Asheville, North Carolina USA
March 17, 2011
A. Hi, Jim.
As a semantics issue, I don't know if there is anything with an actual Coefficient of Friction greater than 1.0. While a rack and pinion set can drive a force greater than the normal force between the two gears, it would not work at all if the actual coefficient approached 1.0. Similarly, there are all sorts of small scale and micro-scale interlocking arrangements, including things as low-tech as duct tape and Velcro :-)
One interesting item I recently heard of, and that Messrs. Chaw and Stevenson allude to, is "friction shims" for flanged connections, where the shims are electroless nickel plated with occluded diamond or other hard particles. The tiny hard particles dig into the opposing surface and can thus transmit torque with a coefficient of .6 and above even when the surfaces may be oily. Perhaps you could either use such shims between the mating parts, or plate one of the mating parts with the composite electroless nickel? Even then, for your needs you'd probably require a keyway, or tapered joint, or something like that since a coefficient "much greater than 1" sounds extremely unlikely. Good luck.
Regards,
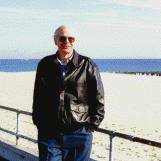
Ted Mooney, P.E.
Striving to live Aloha
finishing.com - Pine Beach, New Jersey
March 18, 2011
Q. I have a requirement which is very similar to Steven and Jim but it also needs to be non-marking. Any ideas?
Benson Thomas- Hannover, Germany
September 2, 2011
High friction rubber?
Q. Hello Everyone.
I am looking for a high friction material that has a a high coefficient of friction. And since rubbers tend to have most friction, I wonder what kind of rubber would be better. The thickness of the material I plan to use doesn't exceed 2 mm. The surface with which the material will be in contact with is organic and smooth.
I would really appreciate any suggestions in this matter.
Thank you
- St louis, Missouri,USA
February 17, 2015
February 21, 2015
No one can respond to that question until and unless you provide some better Information.
Your question is akin to asking "What is the best spice?" There's no one answer.
What is the "organic" surface?
Speed?
Pressure?
Service conditions? Dry, wet, lubricated. None or all of the above?
Temperature?
Expected life?
Optimum coefficient of friction?
Give us some information and then, maybe, we can help.
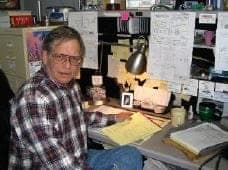
Jeffrey Holmes, CEF
Spartanburg, South Carolina
A. Regarding (static) Coefficient of Friction greater than 1.0... yes, it is easy to see many material combinations with 1.0+.
Rubber on Rubber (dry), Aluminum on Aluminum (dry), Silver on Silver (dry), Platinum on Platinum (dry) are all greater than 1.0. Not to mention thousands of coatings combinations. Note that these are all "like material" combinations, where the surface molecules have greatest "stick" (cohesion).
1.0 is not a welded joint. It is the "slope" upon which (45 degrees) an object at rest under normal gravity will be right at the threshold of "slip".
- New Smyrna Beach, Florida USA
August 27, 2015
Thanks David. The coefficient of friction is the ratio between the parallel force needed to move an object and the normal force on it, and your illustration of a 45 degree angle for a coefficient of friction of 1 is the typical one and a good one. I find the subject an intriguing one because I think a combination of surface profile interlocking and/or cold welding is what we simplify and call "coefficient of friction".
Why is the coefficient of kinetic friction usually lower than the coefficient of static friction? Could it be because we're bumping along with the two surfaces not having time to seat and interlock, like a poorly meshed gear? Why is the highest friction always between identical materials if not due to cold welding or like molecules mechanically interlocking? Why does a little liquid reduce the friction -- is it because it keeps the surfaces from interlocking? I never studied friction after graduation, and wish I had :-)
Regards,
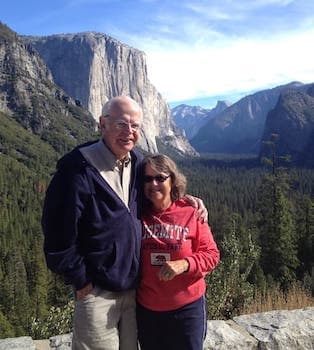
Ted Mooney, P.E. RET
Striving to live Aloha
finishing.com - Pine Beach, New Jersey
August 2015
A. Hello Ted,
Spent lots of hours dealing with friction problems as a young design engineer. Here's the best problem I ever had and solved... a pliable part was being automatically inserted into an automotive assembly, with lubricant. The parts were tearing about once in 10,000 operations, a disaster in the auto industry, a recall was pending. The company asked me to come in and solve after the corporate engineering black belts had about given up after 3 months of DOE.
Took about 5 minutes for me to find the problem... a small force couple due to mis-designed tooling (geometry was wrong) was just enough to stress the material obliquely (shear and tension combined). Every so often the mold line on the part wasn't totally clean... so the stress was just enough to pinch and tear.
The black belts had attacked the problem by throwing different lubricants at it... but the root cause was faulty geometry. Pythagoras and Newton, not some chemists, were the solution.
- NEW SMYRNA BEACH, Florida
February 8, 2016
High friction coating for aluminum or SS rod
Q. I'm looking for a coating on SS or aluminum that will increase its friction with a rubber wheel drive device. I'm getting pretty good results with a carbon steel rod, but SS tends to slip at higher loads. I’m not quite sure why the carbon steel rod performs so much better since the surface roughness does not appear to be significantly different from the other rods. Any ideas?
Conor McNamara- NYC, New York
October 7, 2017
A. Hi Conor,
Hard Anodizing the Aluminum seems the obvious choice; am I missing something?
It's not just the roughness factor that is the difference between steel and SS: SS is lousy for bonding rubber, Steel does bond very well on rubber with or without Chemlock or equivalent bonding products.
A simple CED coating on the steel will also aid the bonding of rubber on steel or aluminum.
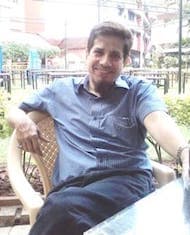
Khozem Vahaanwala
Saify Ind

Bengaluru, India
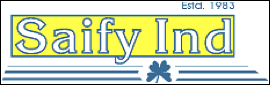
December 14, 2017
Need very high friction non-pneumatic wheel coating for Bonneville Salt Flats car
Q. Hello everyone, I have another friction need. I'm looking for a coating that behaves like the rubber of drag racing slicks. It will be applied to either a 7075 Aluminum or Carbon/Kevlar wheel that will get up to 10,000 RPM with a load of up to 1,000#. It is a non-pneumatic drive wheel for land speed record use on the Bonneville Salt Flats. Durability is open - it only has to last up to 15 minutes if it can be easily reapplied, otherwise 2 hours would be a good lifetime. Miracle coating? Please let me know your thoughts! Thank you!
Leif RideoutLeif Rideout Architect - Scotts Valley, California
October 20, 2018
A.
I have no idea what coating might do what you want, but, AFAIK, all wheel driven Land Speed records have been set on pneumatic tires, provided by one of the major tire companies.
If you're running a jet car, then the apparent go-to material is high strength aluminum. Wheel steering doesn't count for nearly as much as aerodynamics.
But, if you're trying to reinvent the wheel, I have no clue.
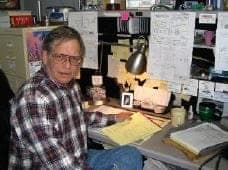
Jeffrey Holmes, CEF
Spartanburg, South Carolina
March 8, 2019
March 2019
A. Hi. You're beyond my depth, but it would seem to me that embedded strands of glass, carbon, or steel fibre would be necessary towards holding any thick elastomer coating onto wheels rotating at 10,000 RPM.
Regards,
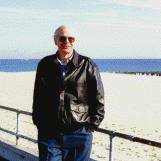
Ted Mooney, P.E.
Striving to live Aloha
finishing.com - Pine Beach, New Jersey
Q. Good day
What coating can be used on a face plate and clutch friction material to minimize wear?
- palles Muritius
August 14, 2020
A. Hi Julio!
Looks like no one has chimed in so far but if you state the exact alloys you are trying to put a coating on, as well as your current challenge and what you would like to see improved, this crew will come up with answers much easier!
Cheers!
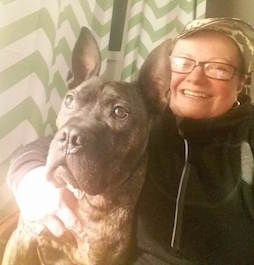
Rachel Mackintosh
lab rat - Greenfield, Vermont
August 27, 2020
Q, A, or Comment on THIS thread -or- Start a NEW Thread