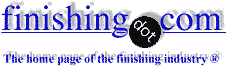
-----
Zinc electroplating for hobbyists and school projects
Current question and answers:
QUICKSTART:
In electroplating you connect a rectifier or battery to two electrodes in a plating solution, and that power supply device will make electrons flow from the anode to the cathode through the wiring. As a result the atoms on the electrode connected to the positive side (the anode) will be stripped of their electrons and become positively charged ions which dissolve into the solution. These positively charged ions will migrate through the plating solution towards the negatively charged electrode (the cathode, i.e., the item you want to plate). When the ions get there they rejoin their electrons and become neutral solid metal again.
So how much metal is deposited is essentially directly proportional to the current, as covered by Faraday's Law.
But some areas of the part, like protuberances will receive more current, and other areas like deep recesses will receive less, so the result will be very uneven plating thickness. 'Throwing power' refers to the ability of a plating solution to work a little magic via things such as addition agents which somewhat shield the high current density areas to somewhat make up for this problem, and help the metal deposit deposit at a more even thickness and even in the low current density areas.
Q. Is there such a thing as TOO MUCH throwing power?
Hi, I am a hobby plater using acid zinc plating.
I recently had contamination in my bath with poor plating results, poor throw and shadowing, so I decontaminated my acid zinc bath by means of decant & polypropylene filtration.
After decontamination the plating results were very good, with good hcd and lcd coverage, brightness seemed fair, but brightness not where I needed it to be. I added additional brightener 1/2 tspn at a time until I realized there was a difference in results.
I decided possibly too much brightener was the reason for the dullness, so I carbon filtered the solution.
Now, i am getting too much "power" in the plating bath, e.g., my dummy piece prior to carbon filtering would plate @ 2amps for 15 minutes with very good results, after carbon filtering, plating @ 2amps within one minute it is bright zinc plated and afterwards starts to burn.
I am not sure what would be the cause of this substantial increase in "power" after carbon filtering.
Please advise
Thank you
- Port of Spain, Trinidad
A. Hi Joshua. 'Throwing power' is a term already reserved with another meaning, so let's not use that one.
You cannot defeat Faraday's Law, so you are not getting a super thickness in a short time at a low current. What you are probably seeing is that without brightener you can't get a bright deposit and you instead get burning. As a wild guess, the reason the very thin one-minute deposit is bright anyway has to do with some surface condition of the substrate.
The best tool for figuring out what is going on is a Hull Cell ⇦ huh? .
Luck & Regards,
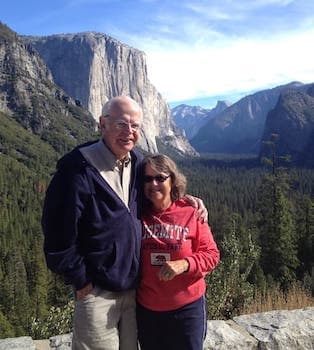
Ted Mooney, P.E. RET
Striving to live Aloha
finishing.com - Pine Beach, New Jersey
January 2021
Q. Can I assume then there is an issue with my power supply?
After decant, filtering and carbon filtering, my test piece which plated at 2 amps for 15 mins with pretty good results went to 1 min @ 2amps and burning.
Or, could this be an issue with plating solution balance?
- Port of Spain, Trinidad
January 23, 2021
Q. So I have solved the issue of plating on exterior surfaces with good bright finish after chromate, although in my opinion the zinc plate looks a bit brown after the bath.
I still have an issue plating coverage inside holes or a recess. I have attached some photos of brownish after bath, and hole issue.
- Port of Spain, Trinidad
January 26, 2021
A. Hi Josua. Your pictures seem to show two different components, a long pipe flange sort of part and a part shaped like a hex nut with incorporated flat washer. You should get I.D. coverage on the hex nut shaped part unless the picture deceives me, but for the part with the pipe & flange it seems quite unlikely. Poor coverage of I.D.s is typical because the current density in there in very low, plus the difficulty in reliably cleaning & activating the area, plus the possibility of depleting the solution of zinc ions within the stagnant solution in an I.D.
Please consider trying to hook up an internal anode, plus keeping the part moving back and forth to being fresh solution to the I.D.
Luck & Regards,
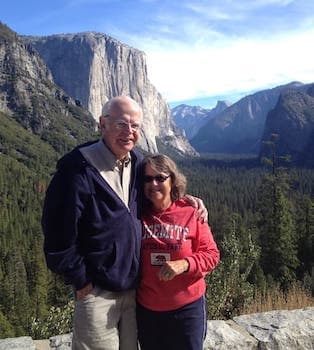
Ted Mooney, P.E. RET
Striving to live Aloha
finishing.com - Pine Beach, New Jersey
January 2021
Q. Thanks Ted, the first photo was to show the color of the zinc coming out of tank. Does it look ok? I found it looked brownish. Prior to all of my issues I used to get a nice bright grey color and also got good zinc deposit inside of tubes or in e.g. the hole in the nut.
I have tried anodes positioned inside the holes with almost no noticeable improvement.
I will keep trying different things.
- Port of Spain, Trinidad
January 27, 2021
A. Hi again. Zinc plating should look like zinc plating not like bare steel. Just to make sure we're clear here, I said "hook up an internal anode" and you said "tried anodes inside the holes" ... you're not talking about just putting a chunk of zinc in the hole, you did hook it up to the power supply?
You can pre-clean, scrubbing that I.D. with a scrub brush ⇦ on eBay or Amazon [affil links] and pumice ⇦ on eBay or Amazon [affil links] powder, and see if it makes a difference; but you have so many unknowns, and probably very limited ability to analyze the zinc plating solution, such that I feel a Hull Cell would be a great help.
Luck & Regards,
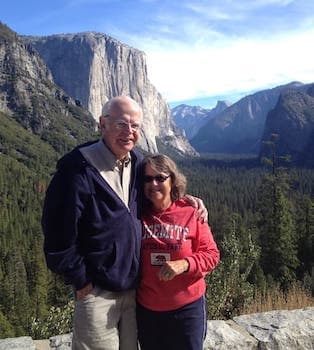
Ted Mooney, P.E. RET
Striving to live Aloha
finishing.com - Pine Beach, New Jersey
January 2021
What defect is this and possible cause?
March 3, 2021Q. Hi
I am having a defect mostly on larger flat surfaces in small spots per pictures attached:
The defect is very bright in contrast as if no zinc is forming over the clean steel compared to the more dullish areas that are getting zinc, almost as if the metal is 'skipping' certain spots but brightening up at the skipped spots.
Also I do notice sometimes one or two very small copper colored marks, they only come off if i wire wheel them.
All of my other small pieces like, bolts, nuts & small brackets come out very good, nice and bright with no issues.
Things that I have done to troubleshoot are: decant and filter, plate a dummy to reduce brightener & remove any impurities. Tried different plating amps and time.
I did notice the longer I leave the piece in the smaller the skipped spots become.
pH is never lower than 4.8 or higher than 5.8, temp is 82 °C.
I may also try carbon filtering, depending.
Any advice is appreciated, thank you !
- Port of Spain
A. Hi again, Joshua. As a hobbyist you probably have no analytical equipment beyond your pH paper and thermometer, which obviously limits your troubleshooting ability. You probably don't have a thickness tester but you should be able to calculate the anticipated average plating thickness (assuming 100% plating efficiency) from the amperage, plating time, and estimated surface area of the part.
I think one of the problems is that your plating thickness is barely nothing, and that the copper marks are evidence not just of copper contamination but the power being off or too low while parts are in the bucket. You also note that small parts come out right, which may be further evidence of insufficient power for the larger parts.
Luck & Regards,
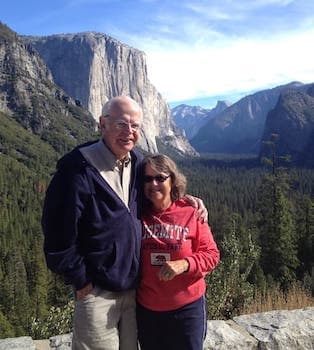
Ted Mooney, P.E. RET
Striving to live Aloha
finishing.com - Pine Beach, New Jersey
March 2021
⇩ Related postings, oldest first ⇩
Q. I am a 6th grader and I want to zinc plate a penny for a science project. I really need some help though! I think I have all the materials, but most explanations of this topic seem vague or extremely scientific. I'd like a simple explanation of how to do it and how it works. Please help! Thanks a lot.
Angelina C [last name deleted for privacy by Editor]- London Derry, New Hampshire
2002
A. A good place to start is with our FAQ "How Electroplating Works"). But in brief: fill a pyrex desert bowl half way with vinegar ⇦in bulk on eBay or Amazon [affil links] . Stir in a teaspoon of salt and a teaspoon of sugar. This is your 'plating solution' although it doesn't have any metal in it yet.
Find three new pennies. Put the shiniest one aside to be the one you will do your plating onto. Sandpaper most of the copper plating off of both sides of the other two pennies to reveal their zinc plated core and drop one of them into your plating solution; some of the zinc will dissolve so you now have a plating solution with metal dissolved into it. Leave the penny in solution for a couple of hours, then remove it and throw it away.
Take the shiny penny and clean it as good as you can with a toothbrush and toothpaste, and wear rubber gloves so you don't touch it again after you start cleaning it (it needs to be spotlessly clean with no fingerprints). Find some copper wire; it doesn't matter too much what kind. Find a 1-1/2 volt D-cell battery. Using the wire, connect the negative end of the battery to the shiny penny; connect the positive end to the other sanded penny--never allowing a short circuit of the two wires or pennies touching.
Put the two pennies into your solution (again not letting them touch). You will see some small amount of fizz as the zinc begins to dissolve into the vinegar solution. The copper penny will start to turn grey or silver colored as the zinc plates out onto it. Plate for a long time, preferably an hour or more. Shine up the greyish coating with the toothbrush and toothpaste if necessary. Good luck!
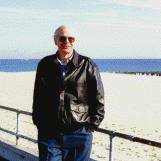
Ted Mooney, P.E.
Striving to live Aloha
finishing.com - Pine Beach, New Jersey
2002
Multiple threads merged: please forgive chronology errors and repetition 🙂
Zinc plating for the newbie/amateur
Q. All,
I'm restoring and old bike and decided to go DIY to electroplate bolts, nuts and washers. I know that I should leave it to the pros but I was enthused by the challenge and, don't worry I won't run platers out of work any time soon.
I did my research and decided to go for an alkaline process using household items: vinegar (5 liters), epsom salt (2 cups) and anti-freeze (6 tablespoons). For power source I'm using a cellphone charger and resistors I bought at an electronics store to adjust the amps so I can get around 100 mA per square inch. Results are good and consistent, however I'm obtaining a pewter finish rather than a chrome-like finish. I understand that this is due, in part, by the type of process I use.
My questions are: can I use brightener or chromate bath to improve the finish? If I want to keep the pewter look, do I need to apply any coating to it to prevent from future rust?
Thanks for the help and I apologize if my questions are too dumb, just learning.
Bike Restorer - Jacksonville, Florida
October 12, 2010
A. Hi, Alex. vinegar is a mild acid. so this is actually an acid process not an alkaline process. Even the professionals have stopped using hexavalent chromates, so you should probably not use them, but Alodine 1201
⇦ on
eBay
or
Amazon [affil links] is available to consumers. Trivalent chromates are all proprietary, so you'd have to buy them, probably in an impractical volume from a major plating supply distributor unless a hobby plating supplier has them. If you want something on top of the zinc, a clearcoat like Everbrite [a finishing.com supporting advertiser] might be best.
These clearcoats help make faded paint look fresher by wetting and smoothing the surface, so they may marginally improve the brightness. But if you want more brightness, buff the parts before you clearcoat them.
For a marginal step up in quality, you can get a simple tin-zinc plating system from Eastwood for $50 or $60.Good luck.
Regards,
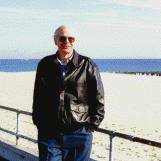
Ted Mooney, P.E.
Striving to live Aloha
finishing.com - Pine Beach, New Jersey
October 13, 2010
Q. Ted,
I stand corrected, it's been a while since I graduated from engineering school. Thanks for your response. Two follow-up questions: what's the risk if I don't apply a coating to the zinc? and what thickness should I seek for the zinc layer? I did some research and see that people uses 8-12 microns.
Thanks again.
Alex
Bike Restorer - Jacksonville, Florida
October 18, 2010
A. Hi again Alex. Zinc is very prone to 'white rust. if not protected. You are correct that 8-12 microns would be ideal, corresponding to corrosion-resistance ratings of "moderate" and "severe". But I think you'll have a difficult time getting that kind of thickness from vinegar-based zinc plating.
Luck & Regards,
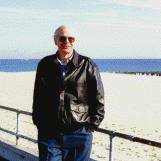
Ted Mooney, P.E.
Striving to live Aloha
finishing.com - Pine Beach, New Jersey
Multiple threads merged: please forgive chronology errors and repetition 🙂
What is zinc electroplating solution?
Q. Hi
I want to know the solution that is used for zinc electroplating.
I think it is sodium cyanide and other chemicals.
thanks
- Egypt
May 1, 2012
A. Hi, Alaa
Please introduce yourself so we understand your situation. School projects of electroplating of zinc for science should be done from safe vinegar solutions per our FAQ, "How Electroplating Works", whereas hobbyists may wish to use an acid zinc process, of which there are different formulations and are best purchased from a hobby plating supplier.
Yes, there are also cyanide-based and alkaline non-cyanide based zinc plating processes, but cyanide should never be used except in a proper industrial facility by people wearing the correct equipment and trained in hazardous materials. Even then, cyanide based zinc plating is declining in popularity because of the hazards and environmental impact.
Books are written about the many formulations, so it's difficult to answer until we understand your particular situation. Thanks!
Regards,
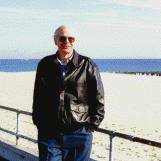
Ted Mooney, P.E.
Striving to live Aloha
finishing.com - Pine Beach, New Jersey
Q. Hi Ted.
I need zinc electroplating for hobbyists.
What is the formula for acid zinc process?
Thanks
- Egypt
May 2, 2012
A. Hi Alex. Hobbyists should probably buy their acid zinc plating solutions from hobby plating suppliers; some are listed on Amazon. But Parthasahardy says 45 g/l Zn, 225 g/l Ammonium Chloride, 1 g/l licorice, By analysis: 21 g/l Zn, 180 g/l Cl, pH 3-4.
Luck & Regards,
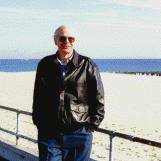
Ted Mooney, P.E.
Striving to live Aloha
finishing.com - Pine Beach, New Jersey
Q, A, or Comment on THIS thread -or- Start a NEW Thread