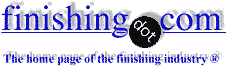
-----
Treating plating wastewater then re-using it
Q. Dear Sir/Madam,
What methods are there to recycle treated water from Electroplating process. Is it reliable to put it back on production? Our plating process requires De-Ionised Water.
What method is the most reliable in terms of initial installation cost and operation cost?
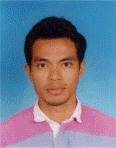
Ali Mahyuddin
Johor, Malaysia
2002
A. Your question is rather general, cousin Ali, but recycling of end-of-pipe wastewater is generally impractical. It is usually better to recycle the individual streams, often with de-ionizing systems, rather than mixing them together.
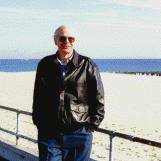
Ted Mooney, P.E.
Striving to live Aloha
finishing.com - Pine Beach, New Jersey
2002
Q. Dear Sir,
We have treatment plant system, and discharge of treated water from WWTP is about 12 gallons per minute. Is it possible to re-use the discharged water for electroplating. We are using deionized water for the plating process.
What methods can be used for re-use of that discharged water. What is the most reliable method in terms of initial installation cost and operation cost.
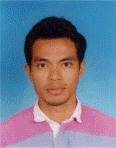
Ali Mahyuddin
Johor, Malaysia
2002
A. Hi again, Ali. I doubt that this treated water is going to be recyclable by any practical method. The usual way to proceed is to instead deionize and recycle at each individual process step, not after neutralizing the batch with gallons of soluble salts like sulfuric acid and sodium hydroxide. To de-ionize this wastewater will probably take as much water in regen and backwash as you will have saved :-(
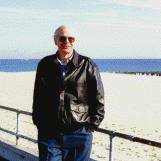
Ted Mooney, P.E.
Striving to live Aloha
finishing.com - Pine Beach, New Jersey
2002
A. Tsk, Tsk Ted!
It will not take anywhere near as much water as you say to regen and backwash! And it is not necessary to deionize water at every step! Most of their streams are probably compatible to be combined into a single feed stream to be fed to a common water recycling system. Unless they have cyanides, most acid and alkali streams can be combined with little or no issues, as "typically", the water still tends to be on the acidic side which keeps particulates and hydroxides, etc down. Equalization is a key here.
You can usually expect to have about a 94-98% reuse factor of the water. A counterflow packed bed design eliminates the backwash cycle, so there is a further savings in required water. We usually use 3.5 - 5 bed volumes or less in our systems per column (a bed volume is a comparative measure of the ion exchange resin used in the process - 1 cubic foot equals 7.43 gallons, so if you have 3.5 cubic feet of resin in each column, you have a total of 7 cubic feet for regen x 7.43 gallons, you get 52 gallons x 5 = 250 gallons total regen waste. Comparably, that would probably need regen on average every 3 days, so you generate 250 gallons of waste for every 17,280 gallons of water recycled on a 12 GPM/8 hr/day basis. That's 98.5% in my book.
End of pipe water can be recycled too using a well filtered RO system - usually a ultrafilter up front of the RO or even the replacement of a conventional treatment with a microfiltration system will make excellent pre-treated water for an RO, which can return 60-75% of the water back as low TDS recycle water. Feed that to a DI system and you can get extremely high quality water for a fraction of the cost of running city water through it.
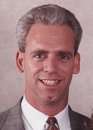
Tom Baker
wastewater treatment specialist - Warminster, Pennsylvania
2002
A. Dilute rinses that are chemically compatible are easily recycled from a wide variety of plating processes. We've done hundreds of them. This is usually much more practical and economical than trying to recycle after conventional treatment. One of the best reasons to recycle before conventional treatment is that it saves more money.
Since it is fairly expensive to operate a conventional treatment system (chemicals, labor and sludge disposal), there can be a considerable savings in addition to the cost savings for water and DI system costs. Various sources estimate this cost to be $8-15 per thousand gallons treated. Typical operating costs for a recycling system are only $2-4 per thousand gallons.
In order to assess the potential for recycling at your facility, you need to do a little homework. A description of the process chemistries and rinse flows is needed as well as either a dragout estimate, or actual pH and conductivity measurements of each rinse. For flows that are less than 600 mg/l of TDS (total dissolved solids), a DI recycling system is usually the best choice. For higher TDS concentrations, an RO system (with pretreatment) may be a better choice, with the RO permeate feeding your existing DI equipment.
If you post more information about your plating processes, it will be easier to be more specific.
Lyle Kirmanconsultant - Cleveland Heights, Ohio
2002
![]() |
A. Tsk, tsk yourself, Tom. Part of the basis of my response was YOUR lecture of last week :-) Ali has a treatment plant and he's talking about passing its salty effluent through ion-exchange to re-use it. It's silly to collect everything end-of-pipe, then treat it with caustic and acid to precipitate the metals, putting soluble Na and Cl ions in their place ... then passing this effluent to ion exchange resin to remove the Na and Cl ions from the effluent so it can be recycled ... then regenerating the cylinders, putting new Na and Cl in to drive out the old ... then treating the regenerate with Na and Cl to neutralize it. And after adding Na and Cl four times in sequence to remove the previous Na and Cl, he hasn't recovered a gram of plating metal yet. I don't take issue with the solutions you proposed, they're just not quite responsive to his question, except of course the idea of possibly adding an end of pipe RO system and being able to reuse the permeate. :-) ![]() Ted Mooney, P.E. Striving to live Aloha finishing.com - Pine Beach, New Jersey 2002 2002
Shame on me - and thanks for listening last week - nice to know someone wasn't asleep after that filling dinner! :-) ![]() Tom Baker wastewater treatment specialist - Warminster, Pennsylvania |
Q. Dear Sir,
Thank you for your support. I have an interest in Lyle Kirman's advice. Our plating process has Nickel and Sn-Pb drag out which is recycled back into plating tank. The WWTP is only treating rinsing water. General info for our Plating process sequence:
1)Acid wash, 2)Rinsing X 1, 3)Nickel Plating, 4)Nickel Drag out, 5)Rinsing X 3, 6)Acid wash, 7)Rinsing X 1, 8)Sn-Pb Plating, 9)Sn-Pb Drag out, 10)Rinsing X 2, 11)Neutralizer, 12)Rinsing X 2, 13)Hot Rinsing X 2, 14)Washing
Rinse water discharge is approx. 2 gallons per minute for Nickel and Sn-Pb.
Final rinsing is manual wash, estimated discharge is 2 gallons per minute
Nickel rinsing water, pH = 2.5 and Nickel = 6.6 mg/ltr. and Solder rinsing water, pH = 2.6 and Tin = 4.21 mg/ltr, Pb = 9.2 mg/ltr.
Please tell me other required data. Thank you.
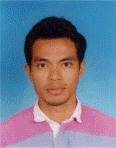
Ali Mahyuddin
Johor, Malaysia
2002
A. Some possibilities include:
1. The acid wash rinse water from step 7 can probably flow to step 2.
2. The washing water from step 14 can probably flow to step 12, and possibly from there to step 7.
3. A rather simple evaporator can probably be installed on the nickel tank which will allow all of the rinse water and dragout to be returned to the nickel tank. However, to avoid build up of contaminants, this requires using DI water on those rinses.
4. An electrolytic recovery cell could probably be put on the Sn-Pb dragout tank, allowing lower flow rates in the rinses.
5. The most important thing of all in trying to reduce water usage, however, is sweating the details with regard to the counterflow rinses. A properly designed 100% effective 3-stage counterflow rinse can reduce the required flow rate by an incredible 100:1 factor (each rinse cutting the contamination level by 10:1 in series). With metering pumps and level controls to effect the counterflow, such a thing may be possible; but real-world designs that allow slosh-back and other divergences from the ideal can quickly destroy a large portion of the benefit.
Regards,
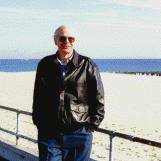
Ted Mooney, P.E.
Striving to live Aloha
finishing.com - Pine Beach, New Jersey
Q. Thanks to all. I am very interested about water pollution. Personally I research about how to make a treatment of water and how to choose the best product which gives more advantages, low cost and makes good to health. Anybody have more information about this?
Che Hasnida bt ab Hamid- Kuantan,Pahang, Malaysia
2004
A. Hi cousin Che. A local university surely has courses and probably even degree programs in water treatment & pollution covering the general issues.
But if your interest is specific to water pollution from plating wastes, you could start with any one of these:
Clarence Roy's "Operation and Maintenance of Surface Finishing Wastewater Treatment Systems" ⇦[this on
eBay,
Amazon, or
AbeBooks affil links],
Kenneth Cherry's "Plating Waste Treatment" ⇦[this on
eBay,
Amazon, or
AbeBooks affil links], or
Kushner's "Water and Waste Control for the Plating Shop" ⇦[this on
eBay,
Amazon,
AbeBooks affil links].
As you can see from the above dialogs, many people have spent decades studying wastewater treatment for electroplating wastes -- and they will surely be happy to clarify any questions you pose as your learning progresses. Good luck.
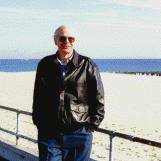
Ted Mooney, P.E.
Striving to live Aloha
finishing.com - Pine Beach, New Jersey
2004
Q. We have an ETP. TDS of final output of water is 4000 ppm. We use RO after this process. TDS of water is 60-70 ppm. if we use this water afterwards in plating again what will be the disadvantage on plating.
Dharmendra ChauhanElectroplating - Ludhiana, Punjab, India
July 16, 2014
A. Hi cousin Dharmendra. The ideal water for use in plating is DI, but it is usually not actually necessary except perhaps in a final rinse to avoid staining. City water is often used, and even high-minerals well water. So, applying RO after chemical treatment of your effluent, and using the permeate for plating use is often okay (although many plating processes are very sensitive to excess chlorides) ... but if you do a balance I'm quite sure you will find that chemically treating effluent water then applying RO and re-using it won't make as much sense as using the water to the max before treatment instead. Ideally, apply DI or RO to each individual process rinse rather than creating a witch's brew and asking DI/RO to sort it out. Good luck.
Regards,
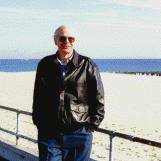
Ted Mooney, P.E.
Striving to live Aloha
finishing.com - Pine Beach, New Jersey
July 2014
Q. How to treat electroplated rinse water? After, can it be used for gardening purposes?
Please answer to my question sir.
I like your guidelines regarding electroplating.
Thank you
electroplating - Karnataka, hoskote, India
May 23, 2016
May 2016
(affil links)
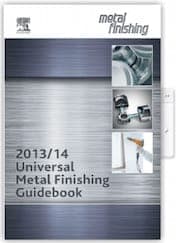
free pdf is currently available from academia.edu
A. Hi Nethra. People generally spend about a decade in the specific field of treatment of electroplating waste control before they attempt to independently design a system without supervision. So asking the general question of how to treat electroplated rinse water is very broad -- but readily available free books like the Metal Finishing Guidebook have a 100-page section on Environmental Controls that you will find interesting.
Please don't discharge electroplating rinse water to a garden until an experienced waste treatment consultant has evaluated the idea; there are probably specific plating wastes that can be safely discharged in this way, and others which should never be. Even if an experienced designer feels that it can be safely done, I personally would not do it with a continuous treatment system, but only with a batch treatment system where every batch can be monitored before discharge, so that no poorly treated waste is discharged to the garden. Good luck.
Regards,
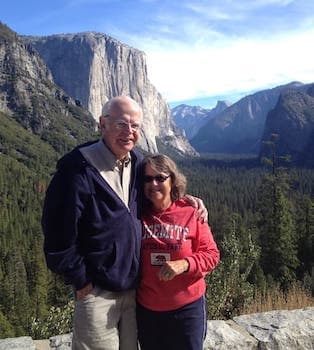
Ted Mooney, P.E. RET
Striving to live Aloha
finishing.com - Pine Beach, New Jersey
A. This is a question that has been posed to me previously. The major issue, as I see it, is that contamination levels may be acceptable for discharge, but they will build up in the irrigated soil. Perhaps they will reach a level that is unacceptable by today's standards. Or perhaps the standards will be lowered to render the soil hazardous waste. (Not that this isn't true of the soil or ground underneath a lot of legacy plating shops.)
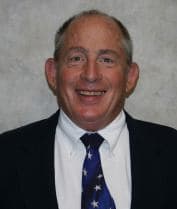
Tom Rochester
CTO - Jackson, Michigan, USA
Plating Systems & Technologies, Inc.

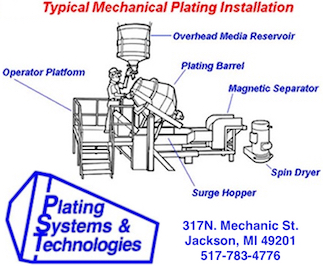
May 23, 2016
Hi,
Currently We do alkaline zinc - non cyanide in our plating shop. I wonder if waste water from rinses can be reused for any purpose within our shop. Please share your knowledge and experience.
- Karnataka, India.
March 27, 2020
A. Hi Abhi. Unless you are highly versed in the various technologies -- and usually even if you are -- my personal opinion is that focusing on truly effective counterflow rinsing so that you can reduce the volume of wastewater will be the most productive use of your time :-)
Regards, and good luck!
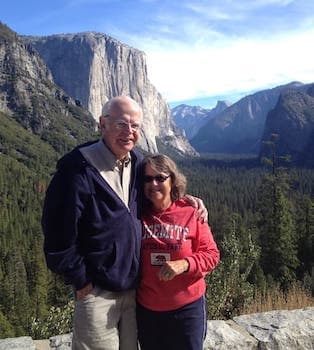
Ted Mooney, P.E. RET
Striving to live Aloha
finishing.com - Pine Beach, New Jersey
March 2020
Q. Hi Ted Mooney,
If it's possible to reuse the waste water from rinses by adopting some simple treatment methods (which needs small investment) rather than sending it to ETP, please let me know the details.
- Karnataka, India
March 31, 2020
A. Hi Abhi. I just finished answering you :-(
Focus on minimizing the use of rinse water with multiple rinses between each process, and the water flowing from the clean rinse to the dirty rinse. Also try to flow water from the final rinse after plating to the pretreatment rinses, and within the pretreatment section, from the acid rinse to the alkaline cleaner rinse.
If you carefully detail exactly how you are set up, it may be possible that specific improvements can be suggested. Good luck.
Regards,
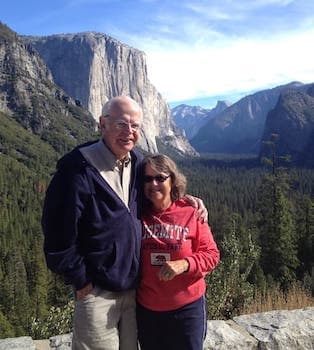
Ted Mooney, P.E. RET
Striving to live Aloha
finishing.com - Pine Beach, New Jersey
April 2020
Q, A, or Comment on THIS thread -or- Start a NEW Thread