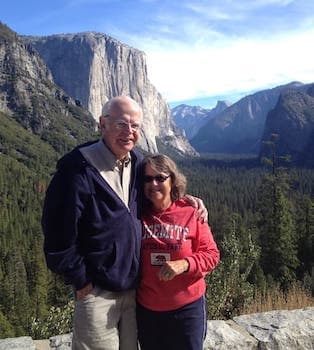
Curated with aloha by
Ted Mooney, P.E. RET
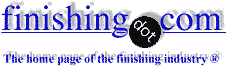
The authoritative public forum
for Metal Finishing 1989-2025
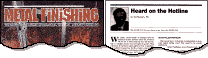
-----
Corrosion Problem on Ductile Iron Castings
We have been having corrosion problems with our ductile iron castings. They are exposed to environments where salt water spray is constantly present (i.e., fishing boats). They are currently powder coated with a polyester type coating and a zinc phosphate primer ⇦ this on eBay or Amazon [affil links] . We are testing our parts in a CASS (copper accelerated salt spray) test. In just 60 hours we have found major corrosion to all surfaces.
The corrosion appears to be pitting (little dots of rust scattered on the surfaces) but upon closer inspection we see that there are tiny peaks sticking up which are rusting. Any machined surfaces have absolutely no corrosion present. We cannot machine all faces nor grind the faces because of time, cost constraints and complex geometry. I'm wondering if there are any coatings that will be able to cover these peaks evenly without making the coating too thick. We have tried E-coating and multilayer coating as well.
Any hints or ideas would be greatly appreciated.
Thanks,
Dave VanLaar- Delta, BC, Canada
Perhaps the castings were blasted using steel shot/grit, and you are seeing corrosion of small particles of the blasting medium stuck in the casting surface.
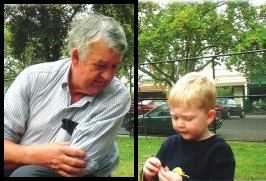
Bill Reynolds [deceased]
consultant metallurgist - Ballarat, Victoria, Australia
We sadly relate the news that Bill passed away on Jan. 29, 2010.
Check the pretreatment prior to phosphate. Blasting with Aluminum Oxide #180 grit and using an immersion heavy zinc phosphate should eliminate the contaminants which are probably entrapped during the phosphate and being released at the time the polyester coating is baked on. If the phosphate is spray applied at the powder coater it may be the culprit for entrapment in the casting.
Wayne McKee- Mississauga, Ont, Canada
Dave,
I was never in the 'coating' field but strictly in the solid (thermo)plastics but I ask myself the question, 'is what you have the RIGHT coating'?
Perhaps the bond 'tween the polyester and the primer is not good enough. Certainly, polyesters are not nearly as good on adhesion as epoxies.
What about an ABS coating (does that exist?)as it would be more abrasion resistant than a polyester, as anyhow would all good thermoplastics ... and you could touch up and build up depth very easily with ABS. ... ABS being a more resilient plastic than, say, PVC and better on temperature and impact.
Finally, what does your competition use?
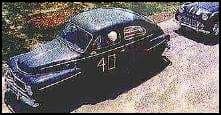
Freeman Newton [deceased]
(It is our sad duty to advise that Freeman passed away
April 21, 2012. R.I.P. old friend).
Casting are inherently porous. The rust comes from the unprotected pores left after coating. The pores must be filled or sealed prior to powder coating. Vacuum impregnation may provide filling of the pores. If that is not economical enough, Prior to the phosphate process, prior to any cleaning steps or acid dips, Dip the casting in very hot water. The metal will expand drawing water (use DI) into the pores. Then phosphate using a heavy zinc phosphate process. The phosphate solution should replace the water in the pores and coat the holes. Some protection of the holes will be imparted , but not nearly as good as the vacuum impregnation.
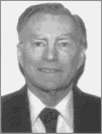
Don Baudrand
Consultant - Poulsbo, Washington
(Don is co-author of "Plating on Plastics" [on Amazon or AbeBooks affil links]
and "Plating ABS Plastics" [on Amazon or eBay or AbeBooks affil links])
I understand preheating the parts can help prevent outgassing of the pores during the powder coat bake curing cycle. As the part is heated during the bake cycle, if the temperature at which the pores outgas is higher than the glass transition temperature of the powder the outgassing can literally blow holes in the coating, thus producing the effect you are experiencing. I posted a request for advice in a similar area yesterday. Has anyone tried salt bath nitriding or nitrocarburizing as a pretreatment for powder coating? I am not familiar enough with the process to know if it will lower the peaks of a rough casting or assist in the pretreatment of pores. I am planning on conducting some tests. Might be an option...?
Malcolm Fleming- Syracuse, New York
Impregnation of the iron casting with a thermosetting epoxy resin will indeed cut down on the corrosion originating at the pores in the casting. The way to determine if this would be beneficial is to examine the as-cast surface vs. that where machining has been done. In general, porosity is more pronounced beneath the outer skin of the casting, thus, if the machined areas are far worse, your problem is simply the pores inherent to the casting process.
Vacuum impregnation is a process used by many finishers, platers, painters and the likes to overcome this all to familiar problem.
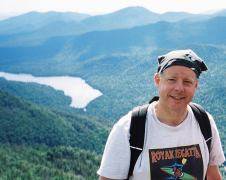
Milt Stevenson, Jr.
Syracuse, New York
Hi,
I have two mating parts. One is steel and coated with zinc and chromated. The mating part is SG iron. The application site has severe salty fluid.
The SG iron mating surface is getting corrosion and uniform wear due to corrosion.
Any possible hints?
Thanks and regards,
- Mysore, Karnataka, India
March 12, 2012
Q, A, or Comment on THIS thread -or- Start a NEW Thread