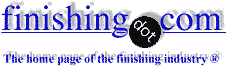
-----
Applied basics of sodium cyanide case hardening for steel.
Q. I work as a managing engineer at a concrete block plant located in central Mexico. My degree is in industrial engineering and I did some graduate studies in the US in mechanical engineering.
Right now I am facing the problem of having to make our own block molds in order to save money. All our molds come from developed nations and are expensive. The block is sold here for about half the price. The basic structure of the molds represents no problem, structural steel can be found here easily. My problem is that there is no quality white cast iron for the wear parts. To get around the problem, we are looking at what is available concerning materials and hardening processes. There is available 4140, 8620 and 9840 steel in plates in the area and we would like to use a case hardening process to replace the stock white cast iron wear parts. If our own made parts last half the time as the stock parts I think it still would be a bargain. We thought of using nitrogen gas or carbon monoxide gas but the small oven we have access to does not have an inlet port for gas and we don't know much about the process. We decided that the sodium cyanide process would be the easiest way but still we don't know how to actually do it. Specifically, we don't know wether to dissolve the cyanide in water and immerse our red hot parts in it or to splatter the cyanide on top of the parts before placing them in the oven or maybe splatter the parts with the cyanide after being in the oven.
I understand this requires a lot of experimenting with temperatures and times and we are most excited about it, but I would like to ask the audience for some tips and short cuts that can save a little time. Is the sodium cyanide process the best for us? Could we put a nitrogen gas tube or carbon monoxide tube through a partially open oven door with the parts inside?
Our main problem has been access to books and literature. What we have is related to materials science and does mention the process but without any specifics. I plan to order a couple of books from ASM but they are expensive and take a few weeks to clear customs. I've also looked on the web and found a few good things but still I'm missing the basics of the process.
Thanks for having this page and thanks in advance for the help.
- Toluca, Edomex, Mexico
A. Good afternoon, Mr Velasco:
Carburizing steel is a process where you diffuse carbon into the surface of the steel. It is highly temperature dependent. At temperatures below 1500 °F, the carbon diffusion into the steel will be so slow that it won't be practical. Immersing red hot parts in an aqueous cyanide solution won't provide a carburized surface and sounds like a dangerous practice. At one time, molten cyanide salt processes were a popular method of carburizing, but safety and environmental issues forced almost all heat treaters to get rid of them. If you are still interested in fabricating your own molds, I would recommend trying to find a reputable heat treat shop to do the carburizing for you. Heat treating, like plating, is not as simple as it looks on paper.
- St Louis, Missouri
April 24, 2009
A. Heat treatment is relatively easy using carburizing salts (mixture-70% sodium cyanide to 30% barium chloride by weight)
The process
1. Never allow water to come anywhere near heat treatment plane or carburizing salts (extremely dangerous).
2. Make absolutely certain there is no moisture whatsoever on the parts to be immersed in the bath (preheat is a good idea).
3. The salts must be heated to 850 °C and kept there until all the salts have liquified.
4. When salts are completely liquified, raise the temperature to 950 °C (working temperature).
5. Immerse the part into the bath and allow to soak for 1 hour; bigger thickness of steel will of course need longer.
6. Allow 3 hours for the carburization process. This usually gives about 1 mm to 2 mm of case hardening.
7. 4140 cannot be carburized using this method. You need to use steel made for the purpose: EN36A, etc.
8. After 1 hour soak and 3 hours treatment remove the work piece and immerse it into QUENCHING oil. You must make sure there is at least 300 mm covering the workpiece and plenty of oil to take the heat out of the steel quickly. If the oil becomes too hot the proper crystallization will not take place and your steel will not have attained the hardness required usually around 50 to 60 Rc.
9. After cooling, lift out of the oil and suspend it over the oil tank to allow oil to drip into the tank.
10. Clean (usually sand blast) and then ready for use or to be ground to correct size.
11. Water dripped into the bath will immediately explode. Even a drop of sweat from your forehead will cause a loud explosion and may blast out some or the molten salts onto workers.
12. Used correctly this method of treating steel is both economical and reliable. Common sense and a steady pace makes a safe work place. Never rush. Ever...
Steven
- Mataram, Indonesia
Alternate to HCl acid for removing Barium Carbonate heat treating salts
Q. We are using HCl acid to remove salt after heat treatment. The molten barium chloride sticking to HSS bits are first rinsed in hot water and then dipped in hydrochloric acid (10%). We want to eliminate the use of acid. Can you suggest some alternative?
gokul ramanujachari- Chennai, tamilnadu, India
August 6, 2016
A. You might try a solution of sodium gluconate, or disodium EDTA.
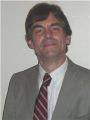
Dave Wichern
Consultant - The Bronx, New York
Q, A, or Comment on THIS thread -or- Start a NEW Thread