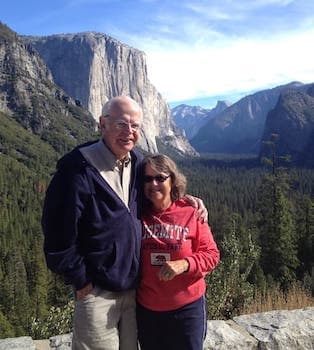
Curated with aloha by
Ted Mooney, P.E. RET
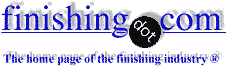
The authoritative public forum
for Metal Finishing 1989-2025
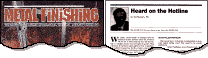
-----
Finish for Al-Alloy to Meet Corrosion and Contact Resistance Requirements
I am looking for a finish over 6061-T6 aluminum that meets the following requirements.
1. Corrosion resistance to meet 48 hrs salt fog (ASTM B117 )
2. Surface contact resistance <1.0 ohm (Class S grounding)
3. Thickness uniformity to hold 3 mil flatness over corners
4. Scratch resistant not to expose Al-alloy in service: article will be bumped and scraped by metal flange during frequent installation and removal
5. Favorable galvanic couple with stainless steel
Right now we are using 1.0 mil minimum of low phosphorous electroless nickel
(AMS2405B) but are have a porosity problem with the nickel plate that fails salt fog.
Thanks, Steve Gonya
aerospace company - Endicott, NY, US
Low Phosphorous electroless nickel is a fussy bath to work with.It will be subject to porosity and or pitting unless it is very tightly controlled. There is a medium phosphorous bath available that has the hardness of the low phosphorous and is not prone to porosity or pitting.Another alternative I have used is to duplex the low phosphorous with a high phosphorous electroless nickel . The addition of an undercoat of high phosphorous provides a pore free corrosion barrier.
Todd Osmolski- Charlotte, North Carolina, USA
A type II chromate conversion coating would meet your requirements
( Such as Iridite 14-2) The T-6 heat treat condition is difficult to chromate due to the higher copper content in the surface from the heat-treating operation. To prepare for chromating, use a deoxidizer containing nitric -ammonium bifluoride, or proprietary equivalent. (If no color develops, deoxidize more to remove copper from the surface.) Copper accelerates the chromate reaction so fast that it sometimes dissolves as fast as it is formed, leaving little of no conversion coating.
There are low phosphorus electroless nickel solutions that are not hard to use. Contact the suppliers. The contact resistance increases with time using low p EN. Hi Phos En has a resistivity of 100-150 micro-ohm cm, but changes only a little on aging.
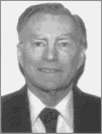
Don Baudrand
Consultant - Poulsbo, Washington
(Don is co-author of "Plating on Plastics" [on Amazon or AbeBooks affil links]
and "Plating ABS Plastics" [on Amazon or eBay or AbeBooks affil links])
Q, A, or Comment on THIS thread -or- Start a NEW Thread