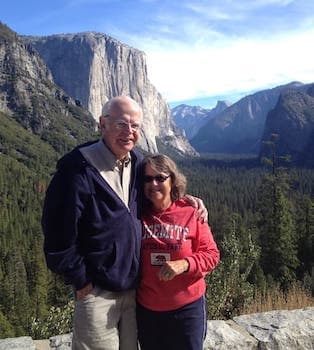
Curated with aloha by
Ted Mooney, P.E. RET
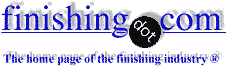
The authoritative public forum
for Metal Finishing 1989-2025
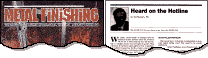
-----
How to pickle, clean, passivate, electropolish Hastelloy for ultrahigh purity
Q. I am currently working on a project investigating a Hastelloy C dryer in a pharmaceutical plant. The problem is that in the first batch of product through it, a lot of grey/black particles are noticed, but subsequent batches have only trace amounts of these particles. The particles have been analysed and are of the same composition as the Hastelloy dryer. It is thought that after the first batch the dryer is passivated. The project is to come up with some way of protecting the first batch. Some sort of passivation technique seems like the best option?. Does anyone out there have any ideas on this one? Please help me!
Barre BrowneU.C.D. - Dublin, Ireland
2000
Q. How should Hastelloy surfaces be prepared for ultrahigh purity applications?
I am using Hastelloy C276 reservoirs to hold a fluorinated polymer for in an ultrahigh purity application. We have had the wetted surfaces mechanically polished to about 10 micro-inch Ra. We then had the wetted surfaces electropolished in an electropolishing solution (formulated for 300-series stainless). Then the reservoirs were rinsed in concentrated nitric acid (to remove electropolishing residues), followed by multiple rinses in DI water. Finally, the reservoirs were moved into a class 100 cleanroom while still wet, and washed down with ultrapure DI water. They were blown dry with filtered nitrogen and bagged in the clean room.
Despite all of this we are still seeing contamination by iron-containing particles, and possibly by organics. Can anybody tell me what we're doing wrong?
Thanks,
- Murray Hill, New Jersey
2002
A. Whitney,
I suggest you electropolish them to Ra less than 0.1 micron. This alloy can be electropolished to such a level of smoothness, since the amount of carbon in the composition is not high.
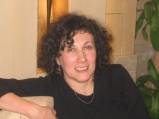
Anna Berkovich
Russamer Lab

Pittsburgh, Pennsylvania
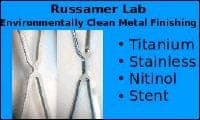
2002
Q. What's the most important parameter in Electropolishing Hastelloy C-22? Is it the Acid (300 series), amps, voltage, temp., cathode(material) and/or distance of part to cathode?
Manuel robas- Ventura, California, USA
2003
A. If you buy a commercial electropolishing solution, the vendor will run a sample for you in their laboratory and furnish the information. See Chemical suppliers below.
Ken Vlach [deceased]- Goleta, California

Rest in peace, Ken. Thank you for your hard work which the finishing world, and we at finishing.com, continue to benefit from.
2003
Multiple threads merged: please forgive chronology errors and repetition 🙂
and Chemical Polishing
of Metals in
Research and Industry"
by W.J. Tegart
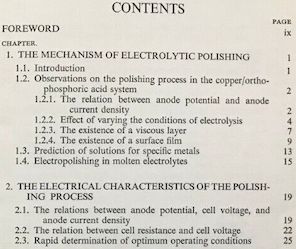
on eBay or
AbeBooks
or Amazon
(affil links)
Q. Could you please advise what acid and mixture would you use to pickle and passivate Hastelloy C-276. We are using the normal chemicals used for for 304L and 316L. The Hastelloy however seems to stain a little dark.
RUSSELL FINLAYMANUFACTURER - KRUGERSDORP, GAUTENG, SOUTH AFRICA
2004
A. Hastelloy C-276 is a nickel alloy, not a ferrous alloy, and therefore does not respond to cold acid pickling/descaling. Haynes International is the maker of Hastelloy, and has a very informative guide available on their website entitled "FABRICATION OF HASTELLOY CORROSION-RESISTANT ALLOYS". Pages 32-33 list several methods for pickling/descaling Hastelloy C-276.
Toby PadfieldAutomotive module supplier - Michigan
2004
Q. How does one know the chemistry concentrations and times required to passivate Hastelloy S, X, or Inco 600 series alloys? I see thatASTM A380
is geared towards CRES alloys, but may be useful for "other metals". We would like to do this in-house and want to get it right.
Thanks!
Machining House - Lakeside, California
2007
A. These nickel-based alloys aren't chemically passivated like stainless steels (passivation solutions are also nickel stripping solutions). However, these alloys must be cleaned of any zinc, lead, tin, bismuth, sulfur & phosphorus contamination before heat treatment or high temperature use. A combination of alkaline cleaning and flash pickling is used. Similarly, embedded iron particles are removed by pickling for the minimum time possible. Iron contamination can be detected by either a 12-24 hour soak in 1% NaCl (rust appears) or the ferroxyl test (blue stain appears). A dilute solution of hydrochloric acid + ferric chloride
⇦ this on
eBay or
Amazon [affil links] (30 mls & 11 grams per liter, respectively) is used for the minimum time possible. Formulas for pickling solutions are given in 'Fabricating' from Special Metals Corporation (Inconel® 600 manufacturer) www.specialmetals.com
For descaling and pickling of Hastelloys® S & X, see 'FABRICATION OF HAYNES® AND HASTELLOY® SOLID-SOLUTION-STRENGTHENED HIGH-TEMPERATURE ALLOYS' available from Haynes Int. www.haynesintl.com
See also the chapter 'Surface Engineering of Nickel and Nickel Alloys' in ASM Handbook Volume 5 Surface Engineering.
- Goleta, California

Rest in peace, Ken. Thank you for your hard work which the finishing world, and we at finishing.com, continue to benefit from.
2007
A. Another method is to electropolish Hastelloy S, X, or Inco 600 series alloys. Thus you will eliminate pickling, cleaning and passivation steps.
adv.
Contact us for more information.
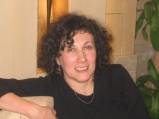
Anna Berkovich
Russamer Lab

Pittsburgh, Pennsylvania
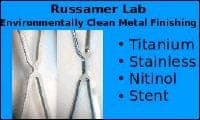
2007
Q. How about the acid inhibitor to be used? I've seen the Haynes data sheet for Hastelloy. I need some idea what could we combine with HNO3-HF mixture for pickling/passivation of c2000 as an inhibitor -- or is it really necessary?
Geofrey Cruz- Doha, Qatar
June 7, 2011
Q. We are getting a bluish discoloration on Hastelloy C-22 parts after electropolishing. Any ideas as to the cause? Our EP shop doesn't know.
Ken Anderson- San Jose, California USA
March 5, 2013
adv.
Send us few samples for testing. If you like the results we would suggest to replace the electropolishing solution.
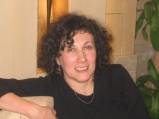
Anna Berkovich
Russamer Lab

Pittsburgh, Pennsylvania
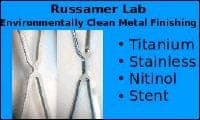
March 8, 2013
Q. I am having a residue left on my electropolished Hastelloy surface after E.P. and doing a 15 minute cleaning procedure to assure no acid is left on the surface. I am using Accomplish Detergent and D.I. 145 °F water. HELP!
Tom Muehlbauer- St Cloud, Minnesota, USA
October 24, 2013
A. Tom, are you saying the yellow film remains on the surface after your workpiece has been thoroughly rinsed and dried? If so, it is the result of surface contamination (statement of the obvious!).
My first thought is that it is caused by the electropolishing solution being laden with metals from previous polishing operations, so have you checked the solution composition for contamination and being outside the operating specification? Hastelloy is based on nickel, with various amounts of chromium, molybdenum and iron in it. Hastelloy G also has copper in it, so any of these metals could produce a yellow(ish) film. Do you remove the workpiece with or without an applied current? If you remove it "dead", you could well get an immersion coating on your workpiece although it would most probably be copper.
You could also be producing surface that is rich in iron - this will appear OK until it goes into the water, where it will from a thin layer of iron oxide - initially this will be green (FeO) but will quickly turn yellow/brown as the ferrous iron is oxidised to ferric iron (Fe2O3/ Fe3O4/FeO(OH) etc) . Anyway, I would start by checking the electropolishing composition for excess metals content and then look at the rinsing solutions and check them for metals.
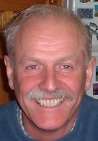
Trevor Crichton
R&D practical scientist
Chesham, Bucks, UK
November 11, 2013
Effect of surface composition of Hastelloy C-276 on electropolishing
Q. Hello,
We are a company that electropolishes Hastelloy C-276 (thickness varying from 30 - 100 micron, 12 mm wide and kilometers in length). We have noticed that different thicknesses polish differently under the same EP conditions, as the thickness increases the grain boundaries get etched more. I have read several letters in this forum that mention that a compositional change (sulfur content etc.) can cause various EP effects. My questions is 1. HOW to different compositions effect EP?
2. Does a change in Ni, Fe, Cr, Mo cause variations in etch rates? Is there some other element that we must be looking for?
3. What kind of surface compositional analysis is recommended to detect differences in composition - XPS/AES?
Any feedback would be appreciated!
Thanks!
- Albany, New York, USA
January 26, 2016
Electropolishing Hastelloy
Q. We are electropolishing Hastelloy and having a problem with a haze/discoloration on the ID of bores and tubing about 3 thousandths inside. Nice polish up to that point, then it gets cloudy.
Tried putting some wire thru the part connected to the anode, didn't seem to help.
R&D - Austin, Texas, USA
January 19, 2018
Q, A, or Comment on THIS thread -or- Start a NEW Thread