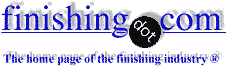
-----
1000 hours salt spray resistance on hardware
Q. We are building generator sets for commercial / industrial use and have a specification of 1000+ hours for salt spray testing for the powder coating on the exterior surfaces. However, we are looking for hardware that will perform to these standards, also. I haven't been able to find any data on plating finishes or using stainless steel for the external bolts. Does anyone have documented figures for materials / plating for hardware that will exceed 1000 hours?
- Springfield, Missouri, USA
A. Stainless bolts and fasteners will easily give you 1000 hours salt spray. Unfortunately they are very weak and will snap and break off in many applications. I have been involved with the "hardening" of heavy equipment for corrosive mining environments. High phosphorous electroless nickel or cadmium works for this application. Neither plating is likely to pass the 1000 hour salt spray. That's not the real purpose is it? The purpose is to be able to use a steel bolt of appropriate strength and hardness and provide enough corrosion protection to be unfastened for repairs and maintenance.
Todd Osmolski- Charlotte, North Carolina, USA
A. Cathodic Electrocoating easily meets the 1000 hours salt spray test specs when tested in accordance to the test standard ASTM B117.
However, you will have to check for its applicability on your components.
Mohali, Punjab, India
A. Electroplated zinc-nickel alloys will exceed 1200 hours salt spray. The coating can be used under powder coating and/or on bolts that are not powder coated. The nickel content should be about 15% and a chromate post treatment used. If nickel is higher than 10% it is difficult to impossible to chromate. Lower than 8% nickel results in less salt spray resistance.
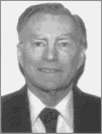
Don Baudrand
Consultant - Poulsbo, Washington
(Don is co-author of "Plating on Plastics" [on Amazon or AbeBooks affil links]
and "Plating ABS Plastics" [on Amazon or eBay or AbeBooks affil links])
A. Zinc-Nickel alloy plating should give you what you are looking for. A deposit of 8 microns with a chromate conversion coating and 5 - 9% nickel in the alloy should give you 1000+ hours to red corrosion.
An alloy of 8 - 12% Nickel should give you substantially more corrosion resistance. I tend to shy away from 15% or more nickel in the alloy, due to a "flip-flop," phenomenon. With this phenomenon, over 15% nickel, it has been noted that the base metal can corrode first. It acts sacrificially with regard to the plated coating.
Another possibility if your part tolerances can stand it, would be to plate 0.0005 inches of Zinc-Nickel. I know of one shop that got over 5000 hours with that thickness and a 5 - 9% nickel.
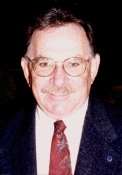

Ed Budman [dec]
- Pennsylvania
With deep sadness we advise that our good friend Ed passed away Nov. 24, 2018
A. Hi Rick. Sorry, but this is a common misapplication of salt spray test requirements. The most robust hardware finish available is hot dip galvanizing, which often survives 75 years or more on such difficult applications as electrical transmission towers which receive little or no maintenance.
This terrific corrosion resistance results from the interaction of the zinc with the carbon dioxide in the air over time, forming impervious and glassy zinc carbonate surfaces which slow corrosion while still offering sacrificial protection to the underlying steel. But these corrosion products will not form in a salt spray cabinet, so lesser finishes outperform it. Salt spray testing is a QA measure to insure that a process has not gone out of control ... it should not be used to try to predict the real-world life of one finish versus another because it can, as in this case, steer you in the wrong direction. Good luck.
Regards,
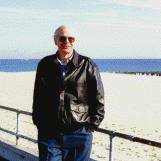
Ted Mooney, P.E.
Striving to live Aloha
finishing.com - Pine Beach, New Jersey
Q. Hi,
I've been told that a 70% tin/ 30% zinc with a yellow chromate has very good corrosion protection. Yet I keep seeing suggestions for other zinc alloys (not tin). Can anyone comment on how the tin/zinc alloy compares to the other zinc alloys in terms of corrosion resistance?
Thanks,
- Bartlett, Illinois
A. Hi Joe. It's conventional to list the predominant metal in the alloy first. Thus zinc-cobalt, zinc-iron, and zinc-nickel, are predominantly zinc (cheap), whereas tin-zinc is primarily tin (about 10x as expensive). So one reason it's often not mentioned in the same breath, although it offers very good corrosion resistance, is that it's significantly more expensive. Tin-zinc is soft and offers lubricity and malleability, so it can be a good choice for critical fasteners that were formerly cadmium plated.
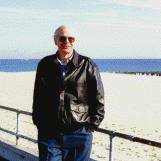
Ted Mooney, P.E.
Striving to live Aloha
finishing.com - Pine Beach, New Jersey
A. Un acabado que cumpliria con sus expectativas seria una aleación Zn/Ni 12/15% cromatada en amarillo de espesor 08 micras + 20 micras de pintura epoxi (aplicada en polvo o Kataforesis).
Un Saludo,
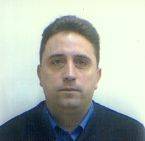
Miguel Angel Martín
surface finishing shop
Madrid, Spain
Ed. note: please follow up in English, gentle readers. We apologize but can no longer post messages except in English. Sorry.
Q, A, or Comment on THIS thread -or- Start a NEW Thread