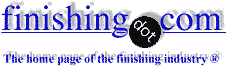
-----
Stability of 420F Stainless
We are currently machining high precision parts out of 416 SS. We machine all of the features of the parts and then harden them and then finish grind critical surfaces. The problem we are having is that after hardening holes will move out of specified position tolerances. Would 420F be a better choice of material?
John Spiegel- Fairport, New York
I can't answer that question. Your part shape and the exact heat treatment process are probably going to effect it more than the metallurgical choice.
James Watts- Navarre, Florida
John, the 420F will give you higher hardness due to the higher carbon content, but not necessarily higher hardenability. And it sounds to me that hardenability is the more relevant issue. Your holes are moving due to (most likely) residual stresses being generated, or being relieved, during the hardening treatment. So you want to do one or both of two things:
1 You want to make sure you are machining in a manner that leaves as little stress as possible from the machining. That means sharp tools, lower feeds, and sometimes lower speeds. Yeah, that'll reduce your productivity, but it's cheaper to make it once than to make it over, isn't it? This should help if your problem is the residual stresses relieving themselves when you heat the parts up to about
1900F during the hardening.
2 You want to quench the parts as gently as possible, which might mean for you to use a gas quench, from say a vacuum furnace, rather than an oil quench. You can get 416 with enough hardenability that you can achieve HRC 40 after a gas quench- we do it all the time. Our final hardness for the 416 is about 35 to 38 HRC. If you need to get harder, I would go with the 420F.
Good luck!

Lee Gearhart
metallurgist - E. Aurora, New York
John,
Mold makers face your situation every single day. Besides what Lee recommended you, there's also the possibility to make those elusive holes "after" the hardening. That's one of the reasons why EDM
(Electric Discharge Machining) has evolved so rapidly. It will obviously depend on pros and cons costwise.
Good luck.
Monterrey, NL, Mexico
Q, A, or Comment on THIS thread -or- Start a NEW Thread