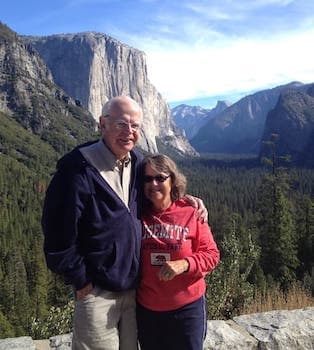
Curated with aloha by
Ted Mooney, P.E. RET
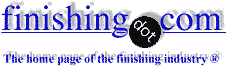
The authoritative public forum
for Metal Finishing 1989-2025
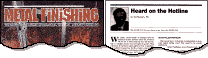
-----
Suggested ASF for hardcoat anodizing
Q. Is anyone aware of a publication that can give suggested ASF ranges for different series aluminum substrates when hardcoat anodizing (conventional 32 °F bath).
Cheryl Bolduc- Gorham, Maine
2002
A. One reference you may find useful information is ASM Handbook Vol. 5 Surface Engineering. The Anodizing chapter contains various references to alloys and processing parameters.
Best of Luck.
Kansas City, Missouri
2002
A. Generally for MIL-A-8625 / MIL-PRF-8625 [⇦ this spec on DLA] type III 30-35 ASF with a ramp time of 1.5 to 3 min for all alloys except for 2000 & 7000 which should run 20-24 ASF with a longer ramp time of 8-12 min
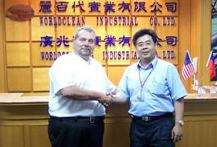
Drew Nosti, CEF
Anodize USA

Ladson, South Carolina
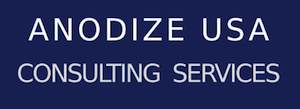
October 13, 2009
Q. Hi,
Can 6061 be successfully hard anodized at 45 ASF to decrease time of production runs and still maintain great parts and thickness requirements?
Anodizer - Sun Valley, California
March 12, 2013
A. Hi David. I am not familiar with such technology. Surprisingly, it looks like that topic has never come up in this forum in all these years . . . so thanks.
But please don't cast it in the abstract like that. Tell us what you have achieved and how, and then people may be able to point to what the next limiting factor will be, and whether they think it is addressable or a hard limit. My bet is that there is a need for extreme agitation to remove the heat and provide fresh solution. 24 ASF is conventional, 30-36 ASF is sometimes achievable, but I wouldn't build a line that counts on 45 ASF for conventionally racked parts without pre-proving it.
A question I'd like to add to the thread is how much time this will save? Although it's easy to see that plating at 45 ASF instead of 30 ASF will reduce plating time by a third, do we think that this will hold for anodizing?
Regards,
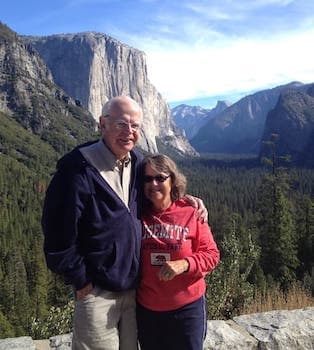
Ted Mooney, P.E. RET
Striving to live Aloha
finishing.com - Pine Beach, New Jersey
March 13, 2013
A. In 2010, the International Hard Anodizing Association (IHAA) conducted a series benchmarking studies of it's worldwide membership of leading hardcoat anodizers. The results of these surveys were presented at the IHAA 13th Technical Symposium in Las Vegas. One of the benchmarking studies was on the current density most used for hardcoating in their facilities. The average current density for all members was 33A/ft2 (3.3A/dm2) with a high of 40A/ft2 and a low of 20A/ft2.
Note: I am now a Past-President of the IHAA and a Board Member and Treasurer.
Luke Engineering & Mfg. Co. Inc.

Wadsworth, Ohio
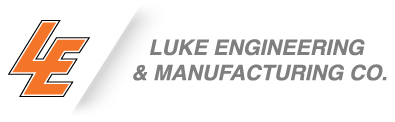
March 19, 2013
A. In theory, you would cut your process time by 33% if you raise your CD from 30 ASF to 45 ASF. If you are processing the same part all the time, you could likely make 45 ASF work.
If you raise your CD from 30 to 45, your heat input will increase more than 50%, all other parameters constant. As Ted mentioned, keeping the part surface refreshed with electrolyte would be the biggest challenge, followed by removing the heat from the bath itself; you're likely going to need a bigger chiller. Unless you're running your tank partially loaded and use the balance of the solution as a heat sink.
Might be cheaper to put in a bigger tank, or an additional tank to increase throughput, if that's what you're after.
- Colorado Springs, Colorado
March 22, 2013
A. Thanks for the insight, Willie -- I think you nailed it.
Transistors beat vacuum tubes every time; so were there a new enabling technology to allow hardcoat anodizing to be done faster and in a smaller space, then we should go for it. But when people just want to increase their production rate without that new type of technology, then simply adding an extra anodizing cell will probably be simpler, less expensive, and much more reliable than trying to tweak the current density beyond established standards.
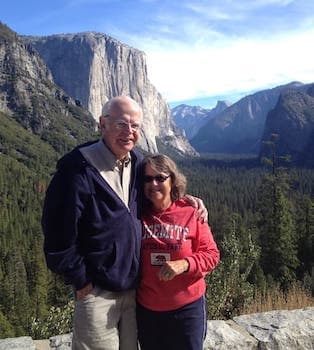
Ted Mooney, P.E. RET
Striving to live Aloha
finishing.com - Pine Beach, New Jersey
March 27, 2013
April 15, 2015
Q. How to use ASF Hard coat?
I am trying to learn the use of new equipment and how to use ASF for Hard coat?
So I have calculated my surface area in square feet and created a parallel circuit (thanks R.H. Probert "Aluminum How To") to read current as it ran. The Bath is 28-30 °F degrees the Sulfuric Acid is 170 g/l. The rectifier is 75V 5000A so I have some power to use.
I put in the load ramped it for 4 minutes to reach 28 ASF; my parallel circuit reads 28 ASF. I calculated my time to be 51.4 minutes plus 4 min ramp (55.4 minutes.) I also tried the pulse feature with 120 sec pulse on and 30 sec pulse base.
We are a Job shop
The questions :
The Parallel circuit read 28 ASF then continued to drop as hard coat was developed over time. Do I continue to increase the current amperage as the parallel circuit current amperage reads a drop in amperage? -- or is this typical and leave the current the same.
Does the pulse here help or any suggestions on pulse?
Plating shop employee - Muskego, Wisconsin USA
A. Hi Casey. Although you want/need to hold the current constant on your actual load, I am not seeing what would allow the current on the actual load to remain constant at 28 ASF while it is dropping on the parallel/dummy load. Are you sure your 1 square foot parallel/dummy load is the same alloy and condition as the actual load?
Regarding pulse anodizing, I offer the same caution as for pulse plating: it is no doubt useful, but it represents yet another variable to tame. Don't fool with it until you solve mysteries like why current is dropping on the dummy load when you are continuously increasing voltage to maintain the ASF on the actual load. For more on pulse anodizing, start with letter 52350, "Hardcoat Anodizing Voltage" which includes entries by Dr. Anne Deacon Juhl, who earned her PhD in pulse anodizing. Good luck.
Regards,
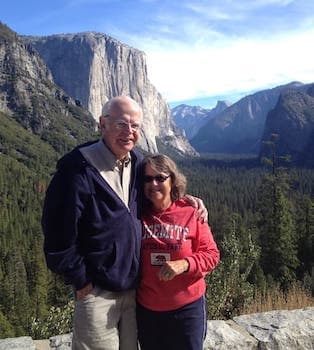
Ted Mooney, P.E. RET
Striving to live Aloha
finishing.com - Pine Beach, New Jersey
April 2015
Q. My parallel circuit is 6061 plate .5" thick by 6" X 10.5" giving me surface area of 143 sq/in. The aluminum rack (6061) is fully masked so only the plate is exposed in the bath. I am reading the load on the dummy as 28 amps (so 28 ASF?) in the cycle time 5 minutes in. Then about 10 minutes later I am now reading the amps on the dummy as 20 amps. I have set the Rectifier to constant current and variable voltage. I can turn up the Current but I do not want to burn the parts. Any suggestions or ideas.
I have read about pulse but am not super familiar with the use of pulse, just wanted to try it on the run.
- Muskego, Wisconsin USA
April 20, 2015
![]() |
A. Casey - Colorado Springs, Colorado April 22, 2015 A. How many volts is your rectifier capable of? You're going to want a min of 75 volts for hardcoat. At 28 ASF, on 6061, your starting voltage should be around 27 or so, and slowly climb to around 55-60 to maintain your current setting (assuming a .002" coating). These #'s may vary depending on your bath parameters, and level of contaminants in the bath. ![]() Marc Green anodizer - Boise, Idaho April 23, 2015 |
Q. I am back at it again!
So, I ran a Parallel circuit with a test plate of one square foot plate again. I have multiple various parts on the bar to H/C anodize with the test plate with goal of .002" total thickness. I set the ramp for 4 minutes 0 start point to current 1450 and when I hit the cycle time at 4 minutes my amps were a little high. I dropped the current to 1240 to read 28 ASF on the test plate. The voltage was set to variable with it running from 26.5 in beginning and it climbed to 45.9 in the time cycle.
The Current amperage on the test plate dropped continuously over the run. The voltage climbed slow to hold current to 1240 but the test plate amperage dropped slowly from 28 ASF down to 14.4 ASF. Near the end of the time cycle the test climbed slowly back up to 23 ASF with voltage climbing to 45.9V. I calculated time for run for 28 ASF to 51.43 plus 4 minutes cycle time to 55.43 min.
I did not get the thickness or outcome I was looking for. Rectifier 5000A Voltage 75- NO pulse done, just a straight run.
What should I try or am I missing something?
- Muskego, Wisconsin USA
July 1, 2015
A. The thing that jumps out at me here is "I have multiple various parts on the bar".
Are all of these parts from the same lot of material? It sounds to me as if you have some current robbing going on here to where the other parts, if not from the same lot, or are not of the same alloy, are robbing current from your test panel.
Even if they are all of the same alloy (6061), different heat lots, or material from different manufacturers can rob current from other parts.
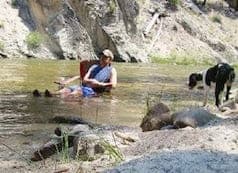
Marc Green
anodizer - Boise, Idaho
July 3, 2015
Type III Anodizing with Constant Current
Q. Does anyone run hardcoat type III anodizing using constant current and running the load with set-amps for set-amp hours derived from surface area calculations?
Example: I have a load of parts that equal 120.6 sq in of surface area and there are 50 parts. So a total of 6030 sq in or 41.875 sq ft. and for example to run the parts at 1465 amps for 936 amp hours to achieve 2 mils of coating?
anodizer - Dexter Michigan USA
September 25, 2015
A. Chad
All day long.
Your amp-hour calculation is off a bit; I get 1005.
- Colorado Springs, Colorado
September 28, 2015

Q, A, or Comment on THIS thread -or- Start a NEW Thread