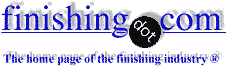
-----
Inconsistent Rusting on 316L Welds
Recently our company provided 316L fabricated products to a site located on an island in the Pacific Northwest. The products have been on site for approximately 2 weeks and now about 15% of the welds are showing rust at the seams. Our procedure for weld cleanup was to use a SS wire brush followed with a citric acid passivation. We really are at a loss as to why this happened.
We are concerned that with the following possibilities...
Our supplier may have mistakenly supplied carbon brushes
Our use of SS wire brushes was not 316L
Our big question is how to fix this problem. We are considering field cleanup and passivation of the welds. Can there reasonable assurance of the integrity of the product after field correction.
Looking forward to hearing from the community...
Thanks...
- Oak Harbor, Ohio, USA
First thing you have got to do is to eliminate the usual suspects. Get some nitric acid and soak your brushes in it. If they go black quickly then they are not stainless steel. Next try your weld wire with the same test. If you do not have any nitric acid available then try testing the weld seams and the brushes with a magnet.
The pictures you submitted were scary but if your problem turns out to be bad brushes then the job will clean up with mechanical cleaning of the welds and a good field re-passivation. The quality of the job will not have been jeopardized and apart from the delay while you do a clean up job everyone will be happy.
If, on the other hand, it turns out to be the weld wire then you have got a great big problem. You could grind out the offending welds but removing all traces of carbon steel would be a mammoth undertaking, it will probably be more cost effective to start over with fresh material. If you find it is the weld material and you decide to redo the welds then please contact me directly as I have some suggestions as to how you can most efficiently remove all traces of carbon steel.
I am very suspicious of the weld wire because even if you did use carbon steel brushes and then passivated with citric you should not have seen this kind of problem unless your passivation was not properly performed.
Good luck and I hope it is a poor passivation job on top of steel brushes.
Let me know if I can help in any way. We can provide passivation services plus we can positively identify materials using our portable x-ray fluorescent spectrometer. Not only could we tell you if your brushes or weld seams are the wrong material but we could tell you exactly what the material is.
- Elkhorn, Wisconsin
This very interesting for me, we had a similar problem on 304L structures for a blast freezer. It turned out to be from the use of a 302ss powered brushing operation. We had a company come in, that is listed on this web site, to apply pickling gel to the damaged areas. It works! The reason I don't believe you had a carbon steel brush in use, is citric acid treatments will remove that, and will not remove contamination from 302 and 304 powered brushing. Nitric/Hydrofluoric and brush electropolishing is the only thing we have found to remove this. I have confirmed all the above with salt spray testing 24 hr 5% solution. One other thing the larger the bristle diameter the worse the contamination. I recommend in the future 316L brushes or Scotch-brite type abrasives for your clean up, this works.
Hope this helps,
- Northfield, Minnesota, USA
What was the procedure for passivating the parts and after passivation were the parts tested with either copper sulphate ⇦ on eBay or Amazon [affil links] or potassium_ferricyanide [affil links] solution to ensure they were passive?
Jim Struck- Lancaster, Pennsylvania, USA
I have seen this before. The wire brush was SS, but it was 410 SS. That is mostly iron with a little chrome. The wire breaks off in the 316L in very very tiny pieces. We passivated the part in several nitric and chromic mil spec passivation tanks for literally days and it still would not pass salt spray. I therefore doubt if citric can fix the problem. Abrasive removal of the "skin" or possibly brush electropolish are probably the only things that will work. I would certainly use scotchbrite wheels the next time.
James Watts- Navarre, Florida
The photos are indeed scary.
The advice you have had so far is pretty good. From the photos the extent of the rusting leads me to suggest that the problem is not derived from the wire brush. Start with the magnet to see if the weld seam is strongly magnetic or not. If it is, you probably have some problems. Take a sample of the same stainless and perform a test weld using the same weld wire. Clean it with a real SS wire brush and immerse the welded area for about 6 hours in a 20 weight percent nitric acid solution. If the weld material is etched (eaten) away, the weld wire is not stainless steel and you will have to start over, with all the consequences. If it is still fully intact, you can breathe a sigh of relief. In this case, take a an all-plastic brush and apply a nitric/HF based pickling gel to the rusty welded area and leave it for 15 minutes. Wash off the bulk with a plastic sponge and wash again with a clean sponge soaked in DI water. Then jet the area with DI water. Keep it wet with DI water for 24 hours to see if the rust recurs. If the weld wire was OK, the rust should not recur. I've seen this on several occasions before and in each case, reworking was the only answer.
- Singapore
Kevin:
I have seen this situation a number of times. I agree with Brad Maas, that the wire brush is the problem. You put so much imbedded iron in the surface that it required a longer passivation process. There are a number of ways that the situation can be rectified. It is harder in the field, but you can get it fixed with a hot citric acid gel or with nitric/HF gels (if you can handle the hazard).
After re-passivation you can easily test the welds to verify that the free iron, ferrites, etc. are gone.
You can also use an electric wand to effectively clean it up, but this may be slow.
We would be happy to work with you on this.
Regards,
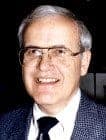

Lee Kremer
Stellar Solutions, Inc.

McHenry, Illinois
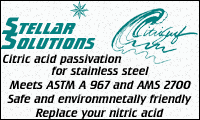
Is it advisable to go for CO2 welding after passivation?
Sandeep PatilDesigner - Pune, Maharashtra, India
February 4, 2008
Sir
I was in the South Pacific (Guam) in the Navy working on Nuclear Submarines for years. Yes, assure the electrode is correct (outside analysis), the use of a qualified welder and procedure and most importantly what is the base material correct traceable to the ingot?
Have your welder use the same base material and filler metal, subject it to salt spray test and then bisect the weld and see what side of the HAZ the corrosion is coming from. If the 316L, procedure and cleaning is correct my bet is cheap/china plate.
lean quality systems - Dana Point, California
September 9, 2011
Q, A, or Comment on THIS thread -or- Start a NEW Thread