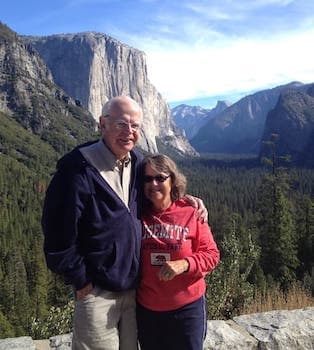
Curated with aloha by
Ted Mooney, P.E. RET
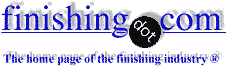
The authoritative public forum
for Metal Finishing 1989-2025
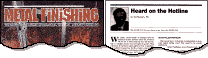
-----
Electrolytic cleaning
Q. In anodic electrocleaning does the surface area of the cathodes have an effect as to the current required?
I normally only supposed the work to be cleaned, e.g., that the positive charge is being applied to, has an effect on the surface area required.
- Perth, Western Australia
June 2, 2022
A. Hi Boris. In most electroplating-related operations the recommended anode-to-cathode ratio is between 1/2:1 and 2:1 depending on the operation. In electrocleaning I think you can be anywhere in that range without it being critical.
The only 'incident' I ever saw in the realm of poor cathode arrangement for electrocleaning was de-zincification of the brass when electrocleaning brass due to a very very poor cathode setup in anodic cleaning: The tank was designed with 1" x 3" submerged steel anode rods, but the operator decided not to buy and hang any anodes from those bars ... which concentrated all of the current onto the very top row of parts on the plating racks and badly etched them.
Luck & Regards,
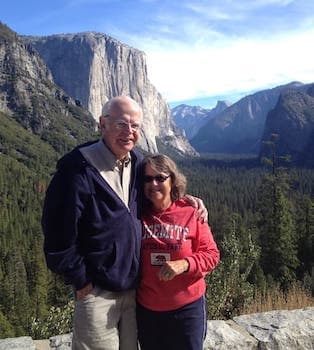
Ted Mooney, P.E. RET
Striving to live Aloha
finishing.com - Pine Beach, New Jersey
⇩ Related postings, oldest first ⇩
Q. How does cleaning take place in anodic cleaning & cathodic cleaning?
P. BHALAJEEbicycle mfgr. - Chennai, India
2002
A. Well, in anodic cleaning, oxygen is released at the workpiece; in cathodic cleaning, hydrogen is released at the workpiece. In either case this results in a good scrubbing action because the gas bubbles form right at the surface of the part.
As far as the polarity is concerned, cathodic cleaning generates twice as many bubbles because the water which is being electrolyzed into gas is H2O -- two parts hydrogen to one part oxygen -- and it does not lead to tarnish or attack on sensitive non-ferrous metals, but it can cause hydrogen embrittlement and deposition of a smut on the parts. There is a great chapter in The Garden State Branch AESF Electroplating Course Manual entitled "Fundamentals of Metal Cleaning" that covers all the implications of anodic vs, cathodic electrocleaning. See our "must have" booklist.
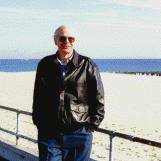
Ted Mooney, P.E.
Striving to live Aloha
finishing.com - Pine Beach, New Jersey
Your question is a little vague. What is it you want to clean? Why do you want it cleaned? Give us a little more to work with and I am sure you will get some useful answers.
- Elkhorn, Wisconsin
A. Electrolytic cleaning: means metal cleaning with the aid of an applied voltage potential in the presence of a medium which conducts electricity, wherein the metal is one electrode submerged in the electrolyte.
Cathodic cleaning: when the metal is connected as the negative electrode wherein it will be having an oxidation potential greater than the other electrode (viz. platinum). So we can clean steel by making it the cathode in an electrolytic cell where the anode is platinum and the electrolyte should be any current conducting solvent like CaCO3.
Anodic cleaning: when same steel is cleaned by connecting it as anode and cathode is copper which is having higher oxidation potential than steel in the same electrolyte (CaCO3).
Even for arresting corrosion they make the corroding element as the cathode by inserting another element as anode with a higher oxidation potential, and the corrosion of pipeline is averted and newly inserted anode will start corroding. This is termed as anodic protection.
metal processors - Chennai, Tamilnadu, India
2006
Q: Required amperage for an electrolytic cleaning tank with two cells to clean steel strip at process speed of 600 FPM, using reverse polarity rectifier 5000 amps with output of 24 VDC. Input voltage = 480 volts/3ph/60 Hz
maximum strip width = 60"
- IRVING Texas USA
October 27, 2015
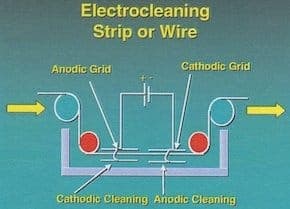
A. Hi Jorge. The general guideline I always used/heard was 50 Amps/square foot minimum, but my experience was in rack plating where several minutes of immersion was practical rather than high speed strip lines. Your strip is five foot wide and presumably two-sided such that there is 10 square feet of surface for every linear foot. If your strip line uses cathodes 10 foot long (in the direction of travel of the strip), you would need 5000 Amps minimum per the standards I am familiar with.
A question back to you: I thought it was conventional to use both an anode and a cathode in strip cleaning, per the attached graphic from the AESF Electroplating & Surface Finishing course.
Regards,
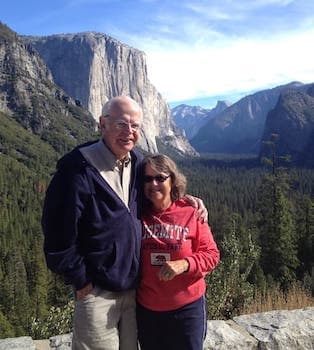
Ted Mooney, P.E. RET
Striving to live Aloha
finishing.com - Pine Beach, New Jersey
October 2015
Should I use nozzles for turbulent flow in electrolytic tank?
Q. Hello Gentlemen,
I have a question. In electrolytic tank, I want to install some nozzles to make turbulent flow for removing iron oxide easier. Is that correct? Please advise me.
Thank you so much.
Hoa Sen Group - Ho chi minh city, Vietnam
February 10, 2018
A. Hi Dinh. When I started in the electroplating industry decades ago, power washers of various sorts were a commonplace process step; today they seem to be a true rarity in the USA but I'm not exactly what changed. Perhaps, either with the development of ultrasonics, the widespread use of electrocleaning, or changes in cleaning chemistry, that process step is simply deemed not worth the extra cost anymore.
If you will tell us what chemistry you are employing (is it rust removal or is it actually degreasing/cleaning, and is it acid or alkaline), what kind of parts you are speaking of, and what your feelings are about ultrasonic cleaning, we can probably talk about it more deeply. Good luck.
Regards,
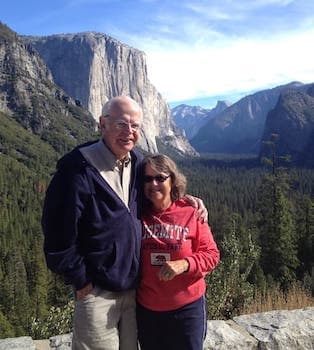
Ted Mooney, P.E. RET
Striving to live Aloha
finishing.com - Pine Beach, New Jersey
Q. Dear Mr.Mooney,
I'm very thankful for your support.
I'm using Alkaline for our electrolytic tank at cleaning section of continuous galvanizing line, and I'm carrying out Galvalume and Galvanize (FH and CQ grade).
Please advise me if I increase turbulent flow in my electrolytic tank, then efficiency of cleaning will increase or not?
And please give me more information about ultrasonic cleaning, I have never seen that method. Is that method used in continuous galvanizing lines?
Thank you so much.
Hoa Sen Group - Ho chi minh city, Vietnam
A. Hello again, Dinh. Although I've seen continuous coil lines a few times, it's not really an area that I've worked much in; sorry.
Ultrasonics are often applied to more complex shapes, but can be applied to coil; they produce scrubbing bubbles like electrolytic cleaning except that do it through ultrasonic vibration of the cleaning solution which causes cavitation rather than electrolysis. Usually ultrasonics would be applied in an alkaline cleaning station which is not electrolytic, and they've very often used on cleaning lines for aluminum because electrolytic cleaning cannot be used on aluminum.
It seems to me that cleaning time is usually quite limited in a coil processing line, so I would think that turbulent flow might gainfully be applied ... but again I have no actual experience with this.
Regards,
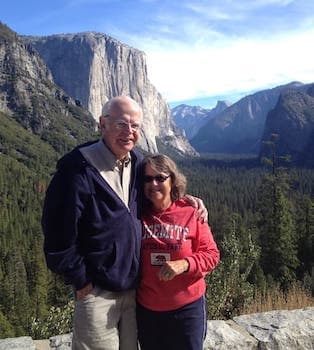
Ted Mooney, P.E. RET
Striving to live Aloha
finishing.com - Pine Beach, New Jersey
A. This would depend on whether the movement of the solution gives any potential benefit.
In an electrocleaning tank that is worked often I wouldn't imagine it would benefit, as it's the evolution of oxygen at the part that creates a scrubbing action to push the smut off.
However in an electrocleaning tank that is used also as a degreaser or soak cleaner, e.g to pre-clean old parts, solution agitation I imagine would help the cleaner penetrate further into the part. In fact on my soak cleaner, solution agitation is a recommendation.
In the 2nd example, one would believe that the evolution of oxygen from the electrocleaning action gives somewhat of a solution agitation itself.
- Western Australia
March 9, 2023
Q, A, or Comment on THIS thread -or- Start a NEW Thread