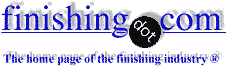
-----
How To Prepare Mill Finish Aluminum for a One Part Acrylic Lacquer?
Hello,
I run a sign shop and we make many of our signs in aluminum. Presently we prepare the surface of the aluminum in the following way:
1) Bondo
⇦ on
eBay
or
Amazon [affil links]
of unsandable scratches,
2) sanding out of light scratches,
3) sanding of entire surface with 150 grit aluminum oxide on a 5" PSA disc air orbital sander,
4) clean surface with denatured alcohol,
5) self etching two part primer (and then either an alkyd high gloss or more typically a one part acrylic lacquer as the finish/top coat - flat or gloss).
My question for anyone that can help me is this: how can I speed the process of general surface preparation, most notably at step # 3 above. I've been told that we don't need to sand our panels but experience has shown that this is not the case. Sure, a "self etching" primer is supposed to be "self etching" and therefore no surface "etching" such as sanding is supposed to be necessary. However, when we have skipped the sanding step we've had adhesion problems, at times disastrous ones. I don't like the sound of using a chemical pre-etching agent because of all the safety and toxicity concerns. What else can we do?
wood graphics - Raleigh, North Carolina
Chromate Conversion Coating
Patrick Patton- Westlake, Ohio
I'm sorry, maybe there was a misunderstanding. I don't want chromate conversion coating. As stated in the original post "I don't like the sound of using a chemical pre-etching agent because of all the safety and toxicity concerns". Maybe a chromate free conversion coating.
Thanks,
wood graphics - Raleigh, North Carolina
Hi There,
Good to see someone who does a good job on their products. I am looking for a smart coloured finish for aluminium frames and am considering lacquers so was interested to see your questions on ally finishing.We would have gone for anodising but that can't be done on castings I understand. Did you ever get a satisfactory answer to the problem? I thought that some sort of electrical etching might work - but sounds like it might take a bit of R&D.; I can imagine a spark erosion type of process with the sparks emitted by a traveling arm similar to a CNC cutting set up but instead of a cutting head you put in a sparking device.
We're product developers so I do tend to get carried away by ideas a bit!. Sandblasting?
Regards
Miles Blackwood
blackwood-eddy p/l - Buderim, Queensland Australia
August 12, 2009
Hi, Dean. Yes, there are conversion coatings that are free of hexavalent chrome. Search our site for "TCP".
But as for your concern about step 3, I think the sanding process is the right idea, but that you could do it in one quick "scritch" with a Timesaver-style flat bed sander instead of spending a lot of time with an orbital sander. Good luck.
Hello, Miles. Some castings can be satisfactorily anodized. It depends on how much aluminum is in them, and what the other materials are. But if you want vibrant colors, you are right that you're unlikely to get them from anodized castings, and might be better off considering electrophoretic lacquering.
Regards,
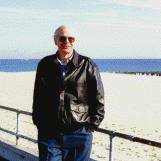
Ted Mooney, P.E.
Striving to live Aloha
finishing.com - Pine Beach, New Jersey
Q, A, or Comment on THIS thread -or- Start a NEW Thread