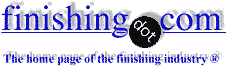
-----
Solutions to Annealing Problems: Stainless Steel types 303, 304, 316, 202

this text gets replaced with bannerText
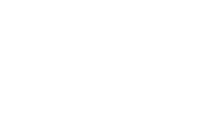
Q. Annealed & passivated stainless parts fail water immersion test.
We had two sets of 316SS parts go to finishing for passivation:
AMS2700 Method I, Type II
The first batch was the same material, but different geometry and they came out great. No issues.
The second batch was a little smaller, same material, but failed the 24-hour water immersion test. They showed signs of rust afterwards. These failed parts were annealed prior to passivating. I can't help but think the annealing process had something to do with the failure. I know the annealing is supposed to increase corrosion resistance.
Any help or insight to why this happened would be greatly appreciated.
Thanks,
- Santa Pula, California
May 9, 2022
A. Hi Geoff,
If the only difference was the annealing, I would look very closely at the quality of the annealing. Particularly cleanliness (parts, part handling and oven itself) and atmosphere.
Are the failures consistent across all parts, or random? All across parts or localised?
- Melbourne, Australia
May 10, 2022
![]() |
Q. Hi Jenna, - Santa Paula, California May 10, 2022 A. Hi Geoff, ![]() Rachel Mackintosh lab rat - Greenfield, Vermont May 12, 2022 |
⇩ Related postings, oldest first ⇩
Q. During intermediate annealing in a Wekllman batch furnace during deep drawing sinks, the 304 2B stainless material corrodes so heavily in some places that pickling doesn't help. The black oxides look like rinsing stains. On non-annealed blanks we found copper contamination. Can copper cause corrosion at high temperatures (1000°C) when present on the surface of stainless steels?
Please help.
- Hasselt, Belgium
2001
A. Copper will certainly oxidized to a black scale at 1000 °C and if there is enough copper there to form a molten metal state, the melted copper will probably penetrate into the stainless steel along the grain boundaries. If this occurs, relatively little copper on the surface could cause damage deep into the stainless steel. Metallographic examination could confirm this condition (or help identify other problems).
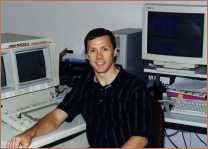
Larry Hanke
Minneapolis, Minnesota
2001
Q. We manufacture humidifier tanks out of 304 stainless and anneal these tanks for use with D.I. or R.O. water. Will we get the same enhancements to the chromium oxide layer with annealing as with passivation? The appearance of the material, after annealing, is bright, though warped from the annealing process. If appearance is not an issue, would we be better off passivating instead?
Alan Garnaat- Three Rivers, Michigan
2002
A. Alan:
Annealing is a totally different process than passivation and will not give you the chromium enriched surface you need to be corrosion resistant, especially in DI and RO water.
After annealing you still need to passivate the surface and welds or you could have corrosion and leaking. Passivation is easy now with the new citric acid formulations available on the market. There are various ways to passivate tanks, depending on size and configuration. You can fill the tank with solution, spray the tank with a spray ball or similar or you can spray on a gelled product.
adv.
It is easy, safe and economical. Contact us for help.
Best regards,
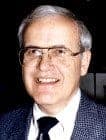

Lee Kremer
Stellar Solutions, Inc.

McHenry, Illinois
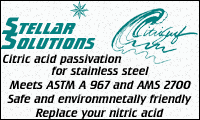
2002
316 stainless preparation/cleaning prior to annealing
Q. Hello,
What are some of the preferred methods for cleaning / washing 316 stainless steel prior to annealing? I am using a mild citric acid wash and rinse to help deburr my parts. Then I use a degreaser and rinse prior to annealing. However, I am getting contaminants which seem to bake onto the steel during annealing and this prevents me from getting the desired finish from electropolishing (non-annealed parts consistently polish to an excellent finish). My parts are typically a couple of inches long, so they're reasonably small.
Thank you,
- Vancouver, BC, Canada
2002
A. I presume you need to anneal the stainless steel because of work hardening, as 300 series stainless steels cannot be heat treated to make them harder. You do not give much information about the process, such as annealing temperature, time, type of degreaser etc. How is the annealing done - is there a possibility of contamination coming from the annealing oven, or is the hot atmosphere causing corrosion of the steel? I also wonder why you are giving it a citric acid treatment prior to electropolishing. I wonder if the citric acid is putting down a passivating film that is not removed prior to annealing and the high (?) temperature is breaking this down to carbonaceous surface contamination. Try eliminating the citric acid treatment. By the way, electropolishing with sulfuric acid/phosphoric acid will give the stainless steel an excellent passive film. I know there is also a citric acid based electropolishing solution, but I have very little experience of it, so if you really want to give the stainless a citrate treatment, perhaps you could try that.
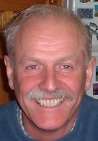
Trevor Crichton
R&D practical scientist
Chesham, Bucks, UK
2002
2002
Q. Thanks for the response Trevor.
We are annealing 3/4 hard 316L steel in a dry hydrogen atmosphere at 1850 °F for 30 minutes. We are pretty sure that the annealing oven is not the source of contamination, as this has been looked into (we don't do the annealing ourselves). I can't say much more about the annealing other than this, as I'm not terribly familiar with the process.
We do a ultrasonic citric acid wash after laser cutting to remove very fine burrs. The citric acid (by itself) is not the source of contamination, as we electropolish non-annealed steel perfectly. As well, if we start with annealed steel (which obviously doesn't need to be annealed again) we also achieve excellent electropolishing.
We have done some EDX studies, and one contaminant that showed up was sulfur. We did not see an increase in Carbon after annealing. We're trying to contact the manufacturer of our degreaser to see if it has sulfur in it.
I like your idea of trying this process without the citric acid wash. Forgetting the citric acid for the moment, assume that we have a un-washed part that we would like as clean as possible prior to annealing: can you suggest a suitable cleaner?
Thank you,
- Vancouver, BC, Canada
A. There is no such thing as the best cleaner -- it depends on what the contaminant is. However, saying that, for the removal of general machining oils and greases, one of the best was trichloroethane, but as you will know this was banned under the Montreal Protocol. The metal finishing industry has been looking for a replacement for many years and there are a lot around. If you want to stick with chlorinated solvents, you could try perchloroethylene or trichloroethylene, but these too have environmental and health issues. There is an increasing interest in brominated solvents and it is claimed they are very effective. Alternatively, you can use aqueous or semi-aqueous based systems that can be very effective, especially with ultrasonics. I would suggest you talk to your supply house and seek their advice as they will be able to match their products to your needs.
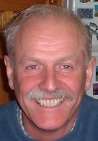
Trevor Crichton
R&D practical scientist
Chesham, Bucks, UK
2002
2002
A. Hello fellow tank jockeys:
This article may be of help:
www.swagelok.com/downloads/webcatalogs/stainlessforsemiconductors.pdf
[updated by editor Nov. 2014]: www.swagelok.com/downloads/WebCatalogs/EN/STAINLESSFORSEMICONDUCTORS.PDF
[updated by editor April 2016]: Swagelok does not seem to offer a technical library of that sort anymore. Storage costs nothing these days: if you see an interesting article on the internet, download it while you can :-)
It confirms that sulfur as sulfide can foul the electropolish process by causing pitting. I believe Sulfide can be formed from more oxidized states in hot Hydrogen, which is your anneal gas. This may or may not be the source of your problem.
Q. I am experiencing a unique pitting problem as well on 316L cold-rolled/annealed. I have a cube, all six sides are identically machined & prepped, yet two sides, front & back pit up to 1200 ASF then polish above that, while the other four sides polish down as low as 200 ASF, no matter how I hang them in the tank or clean them, or what polish formula is used. See my question posted on this site (thread 15893).
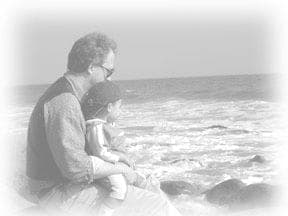
Dave Kinghorn
Chemical Engineer
SUNNYvale, California
A. If your problem is sulfur, try soaking the parts in 5% NaOH for a few hours (elevated temp. helps), rinse well and then go into your EP Process.
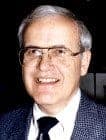

Lee Kremer
Stellar Solutions, Inc.

McHenry, Illinois
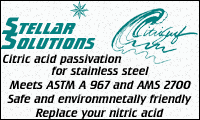
2002
A. Two sources of the sulfur on your stainless could be from an extreme pressure additive in a metal working lubricant that has contacted the stainless and from sulphates in the rinse water just prior to annealing. My experience has shown deionized or low dissolved solids water is best for rinsing prior to annealing.
Roy NussTrevose, Pennsylvania, USA
2002
Multiple threads merged: please forgive chronology errors and repetition 🙂
Bright annealing of stainless steel
Q. I am an Indian Stainless Steel Manufacturer, producing Stainless Steel Sheets. The process of sheet manufacture is quite labour intensive. The sheets are mostly of 200 series and are rolled in hand mills. Of the total Stainless Steel produced in India, more than 70 % is produced by this process. The process is viable primarily because of cheap Indian labour costs. The problem that such units, including mine, is facing is the increasing pressure of Pollution prevention methods.
My question to all is whether it is possible to Bright Anneal Stainless Steel sheets (as SS coils worldwide are bright annealed).
BA finish on sheets would save acid used in re-rolling and mechanical finishing at the end user's end.
Would request all you to give it a thought. The dimensions of the sheets mostly produced are : Thickness 0.25 to 3.00 mm Width : Max 700 mm, Length : Max 3600 mm
Regards,
- Hisar (Haryana), India
2002
A. 0.25 mm to 2.0 mm in BA sheets shouldn't be a problem. Anything thicker than 2.0mm is going to be 2B finish. Depending on your quality standards for mirror polishing this can get expensive (as compared to BA sheets). Good luck!
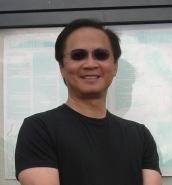
Michael Liu Taylor
specialty stainless steel distributor - Dallas, Texas
2002
A. Sure, you can bright anneal sheets made in a hand mill. The surface finish will not be any better than it is before the anneal. That is, bright annealing doesn't make a bright surface; it only preserves the same surface you have before annealing.
Caution! Sheets may weld together during anneal if they're in contact. Oxide's can form in bright annealing during heat up and cool down. It is much easier to do bright anneal on coils with a continuous anneal than in batch. If pickling acid is the problem, you may want to experiment with abrading the oxide off, especially if you are eventually going to apply a #3 or #4 polish.
- Pittsburgh, Pennsylvania, USA
2002
Q. Dr Michael McGuire- Pittsburgh, PA, USA and Michael Liu Taylor:
Many thanks for your reply. Would like your help further. For bright annealing of SS sheets, what type of furnace would you suggest?
Regards,
- Hisar, Haryana, India
2002
A. Dear Mr. Rajeev
This kind of BA line is very common in china. The only difference is they anneal the coils and your requirement is for strips up to 3600 mm length. On my last visit, I have seen the BA lines which serve this purpose also. The flip side is the initial investment is too high, but it is worth it considering the pollution problem.
import - New Delhi, India
April 10, 2012
Q. My machinist told me I don't have to spec 303 Stainless Steel rod as "annealed". He said all 303 SS rod is annealed. Is that true? Is "non-annealed" 303 SS rod an option when ordering?
Ed Downsbakery machinery - Grass Valley, California, USA
2004
A. ASTM A582 is the North American standard for free-machining stainless steel bars, and Types 303 & 303Se are only available in the annealed condition (Condition A). In fact, only the martensitic grades Type 416, 416Se, and XM-6 are available in anything other than the annealed condition, namely the intermediate temper (Condition T) or the hard temper (Condition H).
Toby Padfieldautomotive module supplier - Michigan
2004
A. The normal supply condition for the 300 series austenitic stainless steels is annealed, but it can also be supplied in the cold drawn condition with increased mechanical properties if required when specifically ordered. Tensile properties increase from around 500N/mm2 to 650 to 865 and above depending on thickness.
Martin Richship repair - UK
2004
Q. I am currently trying to write a validation protocol on a process we currently have in place to stress relief anneal type 301 stainless on some parts we stamp and form that are at the thinnest of the steel spec.
We have been doing this at 600 °F for 30 min (our method is placing them in a cold oven, allowing the oven 60 min to get up to temp and letting them bake for an additional 30 min, then a slow cool)
I am having difficulty finding data to support the timing. I did find a temperature range for stress relief annealing 301 stainless from 500-900 °F.
I need to challenge our operating temperature and our time in the oven and I'm not sure how wide of a range I should use or even where to start.
I thought perhaps someone might have some experience with this or might be able to start me down a path that will not dead end on me as so many websites have done.
OEM Quality / Operations Support Technician - Sterling, Illinois,USA
January 8, 2009
A. SS301 is 16 Cr stainless steel if it is heated through a temperature range exceeding 427 °C without subsequent annealing, it will undergo carbide precipitation and will contribute to intergranular corrosion as such if you are Stress relieving SS 301 I will keep the temperature below 427 °C and extend the holding temperature (this can be varied from 1/2 hour to an hour dependent of the extent of cold working) and then air cool it slowly.
Vijay Vijayaraghavan- Adelaide, South Australia, Australia
February 16, 2009
Q. Is there a possibility of Bright Annealing (in which the surface of SS sheet does not oxidize, i.e., become black or blackish) of SS sheet having 300 mm-650 mm width and 1000 mm to 5000 mm length?
Prakash Nangiabusinessman - Delhi, India
June 23, 2009
Q. Our company manufactures stainless steel tube by cold rolling or cold drawing. We have bright annealing furnace but color of stainless steel tube after B/A is not bright.
Could you give advise for me?
- Busan, South Korea
October 11, 2010
Annealing 205 stainless steel tubes
Q. Working on a project focusing on the annealing of stainless steel; what would be the process required to anneal 205 tubing.
Please include any information such as temperature, time, etc.
Thank you.
- coventry, west midlands, england
November 25, 2014
Q. Hello,
Can anyone explain how to do annealing of 303 SS rod?
Aircraft Instruments - San Antonio, Texas
April 18, 2016
A. Hi folks.
An old volume of the ASM Metals Handbook says for 303SS: "Annealing temperature 1700 to 1750 °F; Cool rapidly from 1850 to 2050."; www.azom.com/article.aspx?ArticleID=8210 compares type 205 to type 304.
Please look up the annealing procedure in a more recent book like ASM Metals Handbook vol. 4: "Heat Treating".
While this public forum can perhaps suggest books & educational organizations in that discipline, and our readers may be able to offer an experience-based response to a carefully delineated shop problem ... internet responses should never substitute for looking up data in a textbook (some posters are unknown to both you & me; some might be incompetent, and others might even deliberately try to mislead). This site focuses on metal finishing rather than on heat treatment, so it's an especially big issue on this thread about annealing because the moderator has no expertise to be able to even warn about bad advise. Sorry :-(
Good Luck and Regards,
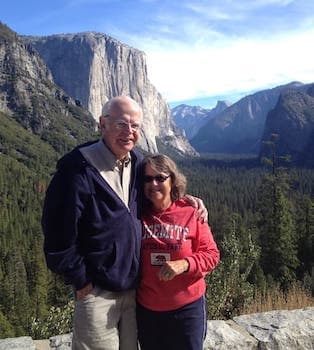
Ted Mooney, P.E. RET
Striving to live Aloha
finishing.com - Pine Beach, New Jersey
April 2016
Q. We are selling stainless steel 202 coil with 4 % nickel for fencing purposes. We first buy s.s. coil and than cut to 3.2 mm width and 0.55 mm thickness.
But for some time now we are receiving complaints from customers that the s.s. strip is breaking after use for fencing purposes.
Please advise what is a reason for the breaking of this strip.
- Rajkot,Gujarat, India
June 16, 2016
Q. What time and temp do I need to fully anneal .091" 303 SS?
Jeff PattersonWytech - Rahway, New Jersey
January 16, 2018
A. Hello Jeff!
According to AMS2759/4, the aerospace specification for heat treating austenitic stainless steel, a setpoint of 1950 °F for 20 minutes at temperature followed by a forced air cool will work.
Good luck!

Lee Gearhart
metallurgist - E. Aurora, New York
February 3, 2018
Annealing 316 stainless steel 0.125 diameter wire
Q. Hello,
We are trying to make some rings out of .125" 316 stainless steel wire. We are cutting The wire to length and "D" bending the ends to weld. The wire is very stiff and does not want to conform to a circle as we need it to. Is there a way to anneal this wire to make it softer, therefore, easier to work with?
Shop employee - Mount Vernon, Ohio, USA
September 11, 2019
Q, A, or Comment on THIS thread -or- Start a NEW Thread