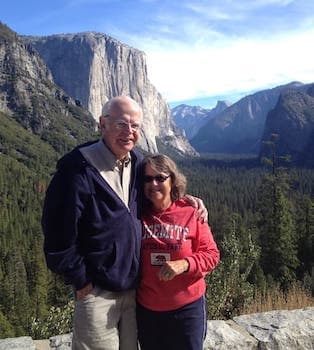
Curated with aloha by
Ted Mooney, P.E. RET
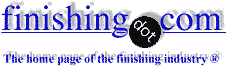
The authoritative public forum
for Metal Finishing 1989-2025
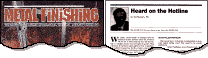
-----
Burnt Plating
Good day, it's me again.
This time my inquiry is regarding burnt plating. Recently we've encountered burning in the lower rail part of two of our products. One is a matrix type and one is standard IC type.
We employ strip-to-strip plating process, and there's ramp-up period, so we use dummy units before and after the production lots.
I've checked factors that I've read on books which may result to burning, such as:
1. Excessive current density - the current/voltage setting is ok.
2. Incorrect amount of Additives - the bath components are within specs, except for one additive with a reading of 3.9 ml/l (the specs is 4 -8 m/l). Is this significant?
3. No rectifier problem was raised during that time, the units were plated.
4. As for the shield height at the plating section, only one out of the 5 plating cells are off-specs, the entry point is off-specs by 9 mm.
5. In terms of anodes, daily replenishment is regularly performed. BTW, how do I know that they are already passivated?
Again, hope you could help us with this problem. What other areas should I check?
Again, Thank you very much.
Nats Pogi- Pasay City, Philippines
Nats:
Try increasing your plating metal concentration. You can evaluate your bath chemistry off-line in a hull cell. Bath pH is another factor you can adjust. Also, try increasing your distance between your anodes and your work.
Karl Weyermann- Lebanon, Kentucky
Q, A, or Comment on THIS thread -or- Start a NEW Thread