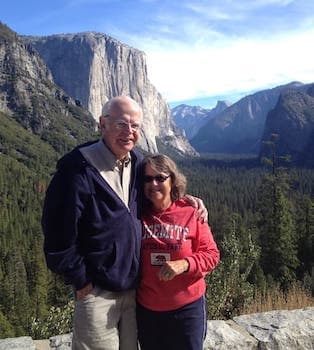
Curated with aloha by
Ted Mooney, P.E. RET
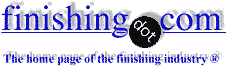
The authoritative public forum
for Metal Finishing 1989-2025
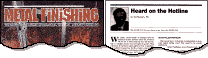
-----
Avoiding/Fixing Hydrogen Embrittlement from Electroplating
Q. We make a small fastener out of C1050 steel hardened to RC41. Would very thin (.0002") zinc electroplating at a modern facility induce hydrogen embrittlement? The unplated fastener never fails because it pulls mounting screws out of wood long before it would break. The market is very price sensitive and we would like to avoid baking due to the expense.
Skip Westmaasfurniture hardware
1997
by Polyanskiy & Belyaev
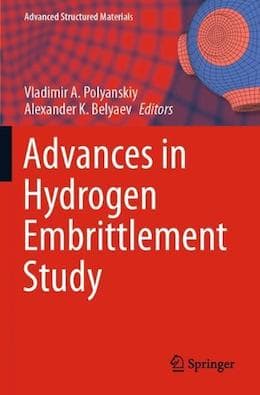
on AbeBooks
or eBay or
Amazon
(affil links)
A. With the fastener scandal of a few years ago, and that Fastener Purity Act, and the liability, I would not try to rationalize about which would fail first. Is baking all that expensive, compared to the plating?
Also, 2 tenths is not thin, that is the spec called out most often for zinc plating. If by modern facility you mean the latest plating solutions, the chemical supplier industry hasn't solved the embrittlement problem, yet.
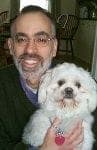

Tom Pullizzi
Falls Township, Pennsylvania
Q. For some reason I have not heard of HE related to zinc plating. However, there are possibilities in eliminating hydrogen embrittlement (HE). What volume and price are you currently talking about? I doubt that just a bake will eliminate HE from a bright zinc bath. Would like to hear more about this HE though.
Mandar Sunthankar- Fort Collins, Colorado
1997
A. Any plating process can induce hydrogen embrittlement. the more inefficient, the more H2 is generated and thus the more embrittlement. The acid dip can cause more problem than the actual plating. You can cyanide cad plate to your hearts content in a regular bath, not a LHE (Low Hydrogen Embrittlement) one, by simply using a short acid dip and getting the parts into the bake as soon as they come out of the final rinse. Even on RC 45 4350.
James Watts- Navarre, Florida
1997
Avoiding Hydrogen Embrittlement in racecar suspension
Q. I am trying to nickel/cobalt plate the mild steel suspension pieces of a race car to eliminate corrosion and to provide a hard long lasting finish impervious to the blasting effect of other cars on the track. I am concerned about Hydrogen embrittlement in the plating process. The suppliers of the plating supplies have not been very helpful and I'm tuning to this forum. I'll be removing the remnants of an original zinc plate on the parts in a Hydrogen or Sulfuric acid pickle. Based upon my own devices, I assume that I should bake the parts (275 °F for 3 hours) after pickling and prior to degreasing, electro-cleansing and plating. The suspension parts manufacture also suggests post-plating bake out (275 °F for 4 hours). Any suggestions?
Jack Wilson- Pittsburgh, Pennsylvania, USA
by Polyanskiy & Belyaev
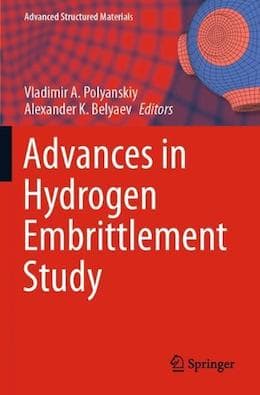
on AbeBooks
or eBay or
Amazon
(affil links)
A. If the parts manufacturer specifies 275 deg. °F. maximum, I wouldn't go any hotter than that, although it sounds low to me by quite a bit. I think 450 °F is more typical -- maybe what you read was a suggestion of temperature in Centigrade? It probably wouldn't hurt to bake in the ovens a few hours longer though.
I don't think I agree that nickel-cobalt plating would be an improvement over zinc for this application. Did you perhaps mean zinc-nickel or zinc-cobalt?
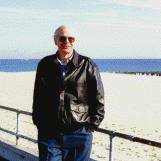
Ted Mooney, P.E.
Striving to live Aloha
finishing.com - Pine Beach, New Jersey
A. Hello Jack!
The temperature used for baking, and for that matter the necessity of baking at all, strongly depends on the hardness of your mild steel parts. Any idea what it is? Generally one doesn't need to worry when under Rockwell C 30 to 35, and the most common temperature of baking is about 375 °F -- you use 275 °F, or lower, if the temperature is too much to maintain the hardness of your part.
In the conservative Aerospace industry, we also tend to use 23 hour bakes -- it's usually easy for a commercial plater, since it's a little less than a day.
Hope this helps!

Lee Gearhart
metallurgist - E. Aurora, New York
Q. Thanks for the responses.
A couple of clarifications: I misspoke in my original post. The bake temperature recommended by the suspension parts manufacturer is 375 °F. I'll use this temp for pre and post plate bake out. I talked with the manufacturer of the parts and there is no Rockwell harness spec. They use mild 1020 steel, zinc plate and then bake at 375 °F for 4 hours. I chose the nickel cobalt because zinc plate always eventually oxidizes (at least on my stuff). I also plan to plate some miscellaneous brackets, so I tried to make a single investment in one set of plating supplies for all of my applications.
Fundamentally, my question is whether a pre-plating bake out is required. I understand the post plate process (and will extend the time based upon your suggestion). But, does the acid / electrostripping process prior to plating induce Hydrogen impregnation that may be 'sealed in' the parts after plating? If so, is 375 °F for 3 hours sufficient to bake of the Hydrogen prior to plating? Or, is this not a concern at all?
Thanks again for your help.
Jack Wilson [returning]- Pittsburgh, Pennsylvania
A. The answer to one of your questions is that pre-plate bakeout is specified for some critical parts because plating can indeed "seal-in" hydrogen. (But if the parts are soft, no baking was needed at all anyway).
Baking times are usually specified to be on the safe side, based on some guesses, rather than actually determined to be necessary. So 3 or 4 hours might actually be adequate; and I've also heard of 6 hours, 12 hours, and 24 hours.
The problem may be that if you pre-plate bake, and then have to electroclean again anyway, what do you do, bake again? Ad infinitum? One thing you might do is blast clean the parts instead of pickling and electrocleaning.
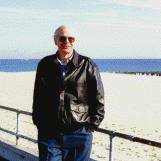
Ted Mooney, P.E.
Striving to live Aloha
finishing.com - Pine Beach, New Jersey
Thanks very much for your help!
- Pittsburgh, Pennsylvania, USA
Multiple threads merged: please forgive chronology errors and repetition 🙂
Can case hardened low carbon steel be embrittled?
Q. Can anyone provide any input on the effects of hydrogen embrittlement associated with low carbon steels that have been case hardened to improve wear characteristics of parts. Specifically, if the parts have been zinc plated, but the baking process was omitted for hydrogen embrittlement relief what are the possible consequences.
Greg RidgeMachining - Xenia, Ohio
2003
A. The most severe consequence is that the parts are indeed embrittled by hydrogen, and will suffer from delayed fracture during service. It doesn't matter that the steel is a low-carbon steel and only surface hardened-- if the hardness is greater than 350 HV on the surface or greater than 320 HV in the core, then the part should have been baked, typically for 4 hours at 200 ± 5 °C. Some microstructures are more susceptible than others, with untempered martensite being the worst. You and your customer should agree upon a standard by which to avoid embrittlement. SAE USCAR 5 and ASTM B850-98 are two such standards.
Toby PadfieldAutomotive module supplier - Michigan
2003
Zinc plated part Failures! Hydrogen embrittlement testing
2004Q. We are doing plating on zinc plated steel parts of greater than 40-48 HRC hardness levels (Medium Carbon Steel).
The parts after plating are immediately baked for nearly 16 hrs at 190 °C.
The parts undergo interference fit with its mating components and have dynamic loads in application.
The embrittlement cracks occur after assembly but not Immediately after assembly.
Due to this heavy material loss occurs.
My question is:
1) Is there any method of checking this induced hydrogen levels after plating?
2) How to reduce this embrittlement risk?
UMASHANKAR.SDESIGN ENGR. - COIMBATORE, TAMILNADU, INDIA
A. 1 - see ASTM F519
2 -ACID, ALKALI, ZINC, OR ANY PLATING CAN CREATE HYDROGEN EMBRITTLEMENT. DE-EMBRITTLEMENT WITHIN FOUR HOURS OR SOONER AFTER PLATING AT 375 °F -- BETTER 400 °F OR HIGHER.
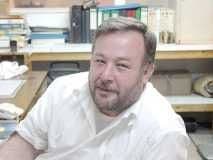
Khair Shishani
aircraft maintenance - Al Ain, UAE
July 3, 2009
A. UMASHANKAR.S
It is difficult to avoid introducing hydrogen when plating zinc due to the over-potential used. Additionally, the typical zinc plating thickness is such that it is difficult to bake-out the hydrogen although a 16 hour bake-out at 190 °C should be sufficient. The previous poster suggested a slightly higher bake-out, and as long as the temperature is not so high as to damage the zinc coating or above the tempering temperature, a higher bake-out temperature is better.
Baking out the parts is an attempt to remove hydrogen. Any cracking that has occurred due to residual stresses and hydrogen (perhaps in the plating bath) will not be repaired. However, you said that the cracks don't appear until after the parts have been in service -- so it is unlikely that your problem is due to any delay in bake-out after plating.
Medium carbon steels with a hardness greater than 38 HRC like yours (hardness of 40 to 48 HRC) are susceptible to hydrogen embrittlement, more so as the hardness increases. I would try tempering so that the hardness is close to the minimum, 40 to 42 HRC. If that is not sufficient, I would look into switching to a lower hardness steel (38 HRC or lower) if possible in the design. Alternatively, zinc coatings that are not plated, such as vapor deposited coatings can be used.
Also -- it is possible that the bake-out is working fine and the hydrogen is being introduced in service. Zinc has a large galvanic relative to steel (this is what protects the steel from corrosion), and in the presence of water (or just high humidity) and a holiday (scratch or break in the plating) zinc will introduce hydrogen into the steel. You might consider plating that has a lower galvanic to steel. In the past an alternative would be cadmium, but cadmium is being outlawed around the world. There is a lot of research presently being done to create plating that has a galvanic couple close to steel (because the stand-by was cadmium plating and RoHS is eliminating cadmium). You might benefit from all this research by finding a plating bath vendor that supplies a cadmium alternative that you can use.
Bill
- Anaheim, California, USA
Q. We are doing a descaling process for removing the scale deposited during the stress relieving done at a temperature of around 550 °C.
For this we are dipping the component in hydrochloric acid for scale removal process -- would it create hydrogen embrittlement in our component? If so, how we can this embrittlement be disposed?
Can you please suggest any other process for scale removal apart from acid dipping.
- FARIDABAD, INDIA
2006
A. Hydrochloric acid pickling will almost certainly cause hydrogen embrittlement.
It is normally considered that if the steel strength is above 1100MPa (approx. 71 ton/in2, 330HV) that it will need de-embrittlement.
Exact times and temperatures will depend on the strength of the material and its heat treatment state (if it has been nitrided, carburised or induction hardened then the temperature will be lower).
This site has huge amounts of information about hydrogen embrittlement and embrittlement relief.
Aerospace - Yeovil, Somerset, UK
2006
A. Also, using a proper pickling inhibitor will reduce hydrogen absorption. Check with chemical suppliers.
Ken Vlach [deceased]- Goleta, California

Rest in peace, Ken. Thank you for your hard work which the finishing world, and we at finishing.com, continue to benefit from.
2006
Q. We are a manufacturer of spring pinch clips, located in Shanghai. We are using zinc barrel plating. Our material is heat treated with 42-47 HRC. Plating parameter is 25% vol. HCl, 6% vol. soak cleaner, 7-10 V in plating, 5 amps/sq ft. HCl time is 10 seconds.
We are using acid inhibitor, but still we are facing the HE problem. How to avoid this problem? I am seeking help from plating experts.
V.R.Sankarprecision components - Shanghai , China
2006
A. Bake at 375 °F for 3 hours immediately after the final rinse and blow dry. The acid tank is the main source of the problem. Can you use a lower percentage?
James Watts- Navarre, Florida
2006
Black Oxide or Mechanical Plating as an alternative to electroplating
Q. I have been advised to stress relieve case hardened parts at 120 - 140 degrees within two hours of zinc plating them to avoid hydrogen embrittlement and subsequent chances of breakage/ failure of the part. Is there any other method of corrosion resistant plating which is economical and will avoid above problem permanently? These are small Hinge Pins which are subsequently painted.
Dilip Bhagwat- Belgaum, Karnataka, India
2005
A. Mr Bhagwat,
It is possible to have the pins black oxide treated.
However,
It is preferable to acid zinc plate, rinse, Nitric acid dip 1% solution Rinse , dry. De-embrittle as advised and then cool to room temp naturally before passivating.
The second suggestion will keep the part corrosion resistant much longer.
Regards
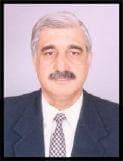
Asif Nurie [deceased]
- New Delhi, India
With deep regret we sadly advise that Asif passed away on Jan 24, 2016
2005
A. Case hardened parts are generally considered more susceptible to hydrogen embrittlement than through-hardened parts. Heat treatment has been used for a long time to reduce the risk of hydrogen embrittlement. The old standard used to be 4 hours at 400 °F. Lower temperatures are considerably less effective. Today, the recommended times are higher; see ASTM B850-98 for details. However, ASTM says "The heat treatment does not guarantee complete freedom from the adverse effects of hydrogen degradation." - In other words, the risk is reduced but not eliminated. For that reason, mechanical plating is an excellent choice for plating zinc on heat-treated parts. For 50+ years mechanical plating has been accepted as a hydrogen-embrittlement-free process. It is capable of plating thicknesses from 0.0001" to over 0.002". Many people, including myself, believe that it is hydrogen-embrittlement-free because the porous nature of the zinc deposit. Black oxide is a nice-looking finish, but it is cosmetic rather than protective.
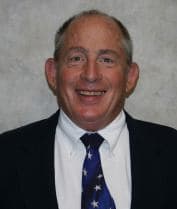
Tom Rochester
CTO - Jackson, Michigan, USA
Plating Systems & Technologies, Inc.

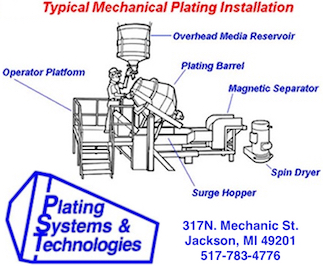
2005
Q. Mr. Tom,
What do you mean by Mechanical Plating?
Regards,
Plating - Ludhiana, Punjab, India
2005
A. In mechanical plating, a coating of zinc (or other ductile metal such as tin) is formed on a ferrous substrate by tumbling the parts with zinc dust ⇦ this on eBay or Amazon [affil links] (5 micron) or other metal powder in the presence of water, glass beads, proprietary chemicals, and dilute or weak acids. The process in industrial practice is a little more complex than this simplified description. Coatings can be as thin as electroplate or as thick as hot dip galvanizing. Applicable standards include ASTM B695.
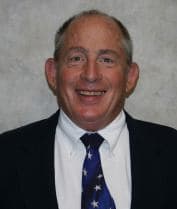
Tom Rochester
CTO - Jackson, Michigan, USA
Plating Systems & Technologies, Inc.

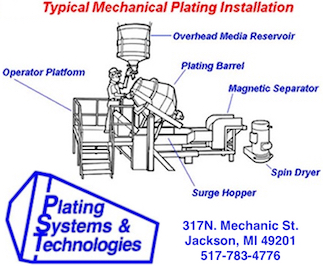
2005
How to avoid hydrogen embrittlement in plating spring steel?
Q. We are purchasing coiled springs which are made of spring steel and are plated to avoid rusting. Kindly let us know if the process of hydrogen de-embrittlement needs to be done for the same and if yes, then how can we check if that process is carried out or not. What is the duration within which this process should be done after the manufacturing process?
Vaishali Shahdie-casters - Ahmedabad, Gujarat, India
2006
A. Yes it does need to be baked, and that bake needs to be as soon as possible after plating. Analytical testing for hydrogen embrittlement is expensive. A simple test is a bend test. Be sure to wear protective eye wear.
James Watts- Navarre, Florida
2006
A. Spring steel, typically AISI 1090 in Q&T condition, is sensitive to hydrogen embrittlement. Hydrogen absorption must be minimized during pickling and other pretreatments. See ASTM B242, 'Standard Guide for Preparation of High-Carbon Steel for Electroplating' or ASTM B849-02, 'Standard Specification for Pretreatments of Iron or Steel for Reducing Risk of Hydrogen Embrittlement.'
Bake-out ('de-embrittlement') of hydrogen absorbed during plating must begin within a short time (preferably within 1 hour) of plating. See your plating specification for details. E.g., ASTM B633, 'Standard Specification for Electrodeposited Coatings of Zinc on Iron and Steel.'
ASTM B850-98 / ISO 9588], 'Post-Coating Treatments of Steel for Reducing the Risk of Hydrogen Embrittlement' gives more hydrogen bake-out details.
A commonly used test is ASTM F519, 'Standard Test Method for Mechanical Hydrogen Embrittlement Evaluation of Plating/Coating Processes and Service Environments.' Tensile specimens of heat treated AISI 4340, obtained from a metallurgical testing lab, are processed identically and with production parts. The specimens are returned to the lab for testing IAW ASTM F519.
Searching this site for 'hydrogen embrittlement' turns up 184 results for further reading.
Survey the plating shop and examine production procedures and QA records.
- Goleta, California

Rest in peace, Ken. Thank you for your hard work which the finishing world, and we at finishing.com, continue to benefit from.
2006
A. Best if done within one hour of plating. Leaves no residue, besides a slight discoloration depending on the particular plating. There are many articles, books and specifications covering the issue.
Guillermo MarrufoMonterrey, NL, Mexico
2006
A. What if you use electroless nickel? Good luck
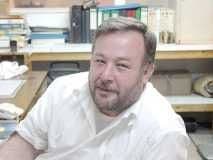
Khair Shishani
aircraft maintenance - Al Ain, UAE
2007

Q, A, or Comment on THIS thread -or- Start a NEW Thread