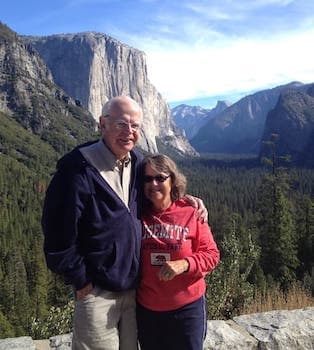
Curated with aloha by
Ted Mooney, P.E. RET
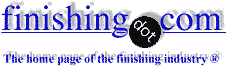
The authoritative public forum
for Metal Finishing 1989-2025
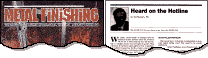
-----
"Bondable" coating on really hard metal
We often bond metal "hard points" to composite automotive parts we manufacture. Some of these are machined out of "Roc Tuff" which I believe is a proprietary name for this grade 8.8 steel. We the have it cadmium plated but have found rather weak adhesion between the cadmium and the parent metal, (in tests the plating comes off before the adhesive). It almost seems as if the parent metal is too "hard" for the plating to stick to, is this possible & does someone have an alternative to cadmium plating which will give the necessary protection yet be "bondable", (using epoxy or modified acrylic adhesive). The client is a really high profile automotive manufacturer, so the quality and "look" is almost of equal importance.
Willem Kleinschmidt- Cape Town, South Africa
I am not familiar with this metal but I doubt that it is too hard. Rather, it may have so much carbon or something else that the cadmium plating doesn't start everywhere, but only in spots. Or it may have enough passive materials like nickel and chrome that the surface is not activated by your process. Can you try a Wood's nickel strike before the cadmium plating?
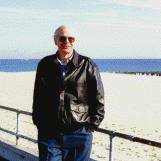
Ted Mooney, P.E.
Striving to live Aloha
finishing.com - Pine Beach, New Jersey
This is opinions, not gospel. Some alloys are very hard to activate. I do not know what is a 8-8 steel. I have never seen a bolt higher than a grade 6.
Really hard steel is frequently high carbon which tends to leave a minute trace of carbon on the surface which lowers the adhesion of the plate. The aircraft builders tend to use sulfuric-hydrofluoric anodic etch which on some steels the resultant smut does not reduce the bond that bad. Your plater would almost have to set aside an etch tank just for your parts, which they probably can not afford to do.
Another thing might be to do a periodic reverse in an alkaline cyanide cleaner after the etch. Tough problem as some of the epoxies have excellent adhesion and internal strength.
James Watts- Navarre, Florida
I suggest you try Zinc plating from an Chloride Zinc Solution , I suspect that you are getting the Cadmium plated from a cyanide solution. It really is not suitable for plating onto steel with carbon rich surfaces. Cadmium is really only better than Zinc for corrosion protection in some specialized circumstances and it should be a lot cheaper. Ask for Zinc plated to 10 - 12 microns with a yellow chromate conversion coating.
Regards,

John Tenison - Woods
- Victoria Australia
In the May 2002 issue of Metal Finishing, letters section, there was a question about bonding grade 8.8 steel to a composite.
Grade 8.8 is one of several ISO designations for the strength of metric fasteners. The ISO system is similar to the US system of fastener grades, grade 2, grade 5, grade 8, etc.. In the US system all socket head products ( socket head cap screws & socket head set screws ) and some hex head bolts are grade 8. There are several ISO grades for socket head products. In the metric system, grade 8.8 is approximately equivalent to grade 8 in the US system. Any steel that meets the specifications for grade 8.8 can be used. These specs are available from various fastener manufacturers. I'm guessing, but perhaps the letter writer was using grade 8.8, cone point, socket set screws for their "hard points". These probably would have a black iron oxide protective coating with an oil film.
I enjoy reading Metal Finishing, especially the letters section.
Sincerely,
Joe CoehloQ, A, or Comment on THIS thread -or- Start a NEW Thread