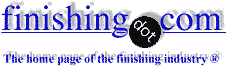
-----
Nickel sulfamate electro forming
Q. I am a student in northern New York researching the nanocrystal structure obtained from Nickel Sulfamate electroforming. I am electroplating on a nickel wire to produce test specimens. My problem is that I keep encountering large pits in my samples. I am using an anti pit agent (SNAP), and I am using cathode agitation. Could this be caused from the hydrogen gas being formed in the bath? Any help would be appreciated.
Gregory WahlClarkson University - Potsdam, New York, USA
A. Do you have enough snap in the bath? You can check quickly by forming a 5 inch diameter wire ring and dipping into the bath and slowly withdrawing. You should be able to hold a bubble at least 15 seconds. Is the bath agitated? It should have mild to moderate agitation. How about the boric acid concentration, if it's low you'll get pitting also. Is the part completely water break free when you load it? And finally organic contamination can cause pits but if you have a new bath I doubt this is the problem unless you neglected to leach your anode bags.
Russell Richter- Danbury, Connecticut, USA
A. Hydrogen pits (gas pits) are recognizable from their smooth, shiny, hemispherical appearance which is the direct result of what they are. But there are other problems which can lead to gas pits besides not enough wetter.
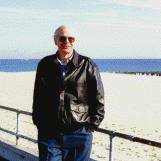
Ted Mooney, P.E.
Striving to live Aloha
finishing.com - Pine Beach, New Jersey
A. Cathode agitation is marginal. Add some air agitation. If you are plating in the lab, a fish tank air pump is enough. Use a red hot paperclip to put holes in the tubing. Seal or plug the end. Weight it down with some stainless steel and stainless wire. Place under the part. Should raise waves about 1/2 inch high. You will need to switch to SNAP/AM or you will have mounds of green bubbles.
James Watts- Navarre, Florida
Q. I realize there are many factors involved and maybe I should have included them in my original post. I am using SNAP A/M 0.3% by volume, as for boric acid concentration, I used 4.25 oz/gal (31.9g/L) @ 90F (32C) and 6.5 oz/gal (49g/L) @ 140 °F (60 °C). As for agitation the bath was well agitated and I also used cathode agitation. As for the part being water break free, I am not familiar with this term. Does this mean removing contaminants prior to loading? I do decontaminate everything in a SNAC mixture for 24 hours prior to plating. I do not believe the anode bags are responsible, I'm not using one! I an using Ni-290 anodes because purity is very important for what I am doing, and my process is very small small, so anode crumbling doesn't seem to be a problem. Could these small nickel particles cause these pits? Also, I am keeping my bath at a pH (electrometric) of 3.5 to 4.5.
Thanks for your time.
Greg WahlClarkson University - Potsdam, New York
A. Greg,there are a variety of reasons for pitting.....in the main it is the formation of H2 due to the water in the bath disassociation of water causing Hydrogen pitting ( if too much current is applied causing an overpotential at either cathode or anode), this also could be the case of a weak electrolyte and of course a pH that is too low <3.8 in the case of Ni sulphamate. If you experience nodules(lumps on the surface) this could also be a hydrogen pit that has failed to "burst" and electro-plated over.....
Steve Duncan- Cambridgeshire, UK
Q. I new for nickel electroforming and I am electroforming nickel letters. I am using a 12 inch x 16 inch Stainless Steel Plate and I do expose only 8.5 in x 11.5 in area of it using photo resist. I am using 8% sulphamate bath, antipit (as per recommended by supplier), nickel brightener (as per recommended by supplier), leveling agent (as per recommended by supplier), boric acid 34 g/l, temperature range 55-60 °C, and solution has pH of 4.1-4.2, 20 minute tank turnover filtration and mechanical cathode movement. I am doing it on 2 volt.
Electroformed nickel letters are good enough but have thickness variation like on an a4 sheet top corners are on 70 micron, center has only 35-40 micron and bottom has 100. I am unable to understand how to control overall thickness with 10-20 micron variation.
Do over loaded anodes cause thickness variation as my anodes are titanium baskets of 4" x 18" and I hang 4 of them full of nickel pellets but I hang only 1 mandrel at a time for electroforming ?
It takes 90 minutes for 70-80 micron deposit. Increasing voltage from 2 to 2.3 causes corner burning. My rectifier doesn't have any setting for amps. Increasing the voltage increases the amps.
Also letters do not easily peel off. I use pregum transfer sheet to pickup letters and than I hammer from back of the SS plate. Sometimes hammering does not work. Should I use sodium dichromate. I also passivate my mandrel in H2SO4 and then wash with DM water and than I dip it into sulfamic acid
⇦ on
eBay
or
Amazon [affil links] .
Kindly suggest me what and where should I make improvements for better quality and easy operation so I can save my metal wastage and time.
- Kanpur, UP, INDIA
April 30, 2013
A. First get an rectifier where you can set the current not the voltage. If you work just on voltage you will not be able to get reproducible results in thickness on different plates. After this you can start to learn about Anode Cathode ratio, Shielding , proper bath chemistry and analysis. Electroforming with a good distribution of nickel over the mandrel is not an easy thing you can setup in a few days.
Marcus Hahn- Zug, Switzerland
May 7, 2013
Q, A, or Comment on THIS thread -or- Start a NEW Thread