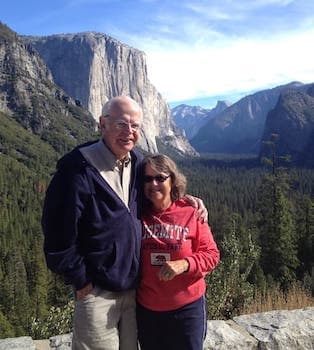
Curated with aloha by
Ted Mooney, P.E. RET
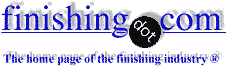
The authoritative public forum
for Metal Finishing 1989-2025
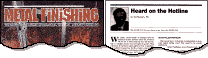
-----
Arcing, Popping, & Hydrogen "Explosions" in Plating, Anodizing, & Electropolishing
Quickstart:
Electroplating works via the rectifier or other power supply pulling electrons from the anode, and pumping them over to the cathode through the copper wiring, forcing the atoms of metal at the anode to become positively charged metal ions, dissolve into the electroplating solution, migrate through the solution over to the cathode, and recombine with those electrons to become metal again.
In the course of this reaction, some portion of the electricity works inefficiently, separating the water in the solution into hydrogen and hydroxide or oxygen. In addition "electrocleaning" tanks deliberately generate hydrogen bubbles to assist in the cleaning, whereas anodizing tanks generate hydrogen in the course of releasing oxygen to accomplish their purpose of anodizing aluminum.
This hydrogen can "pop" when ignited by a spark, similar to what you may have seen back in science glass.In the old days of 50 years ago it was common for electrified cleaning tanks to not have local exhaust ventilation and such "pops" might happen several times an hour. These days most tanks have local lip-style exhaust ventilation systems which mix that hydrogen into the exhaust air such that it never reaches the lower explosive limit.
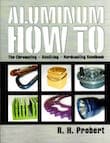
Aluminum How-To
"Chromating - Anodizing - Hardcoating"
by Robert Probert
Also available in Spanish
You'll love this book. Finishing.com has sold almost a thousand copies without a single return request :-)
Q. Hi, We are in a process of installing a pilot scale anodizing facility with cleaner, caustic etch, acid etch, anodizing and E-coloring process. Each tank size is ~ 90 lit and we are providing exhaust system over all chemical tanks. So, please let us know how much is the Hydrogen gas getting liberated during caustic etch reaction and anodizing reaction while processing 30 cm X 5 cm Al profile?. Does this need any special hydrogen detection instrument?
Atul Karpe- Pune, India
February 6, 2023
A. Hi Atul. You should be able to easily estimate the amount of hydrogen generated in the anodize tank from Faraday's Law. I've never attempted calculating the amount of hydrogen chemically generated in pre-treatment tanks though.
If the tanks are ventilated I can't imagine hydrogen accumulating to anything close to its lower explosive limit'; sorry, I've personally never heard of anyone ever employing a hydrogen detector.
Luck & Regards,
Ted Mooney, P.E. RET
Striving to live Aloha
finishing.com - Pine Beach, New Jersey
Q. Hello I have a small 25 gallon nickel acetate tank for hobby purposes. I've used it in a large open room with good air exchange. The largest item I've plated drew 100 Watts at 5V. Should I be concerned about hydrogen production and possible ignition?
Bill Davis- Rochester New York
August 27, 2024
A. Hi Bill.
Never say never, but in a career in electroplating and anodizing going back to 1967, I personally have never heard of any damage or anyone ever hurt due to this hydrogen generation, and many nickel plating installations are 100X - 1000X bigger than yours.
Luck & Regards,
Ted Mooney, P.E. RET
Striving to live Aloha
finishing.com - Pine Beach, New Jersey
⇩ Related postings, oldest first ⇩
Q. During operation of an electropolish bath (S.S. 60P/20S/20W) an operator inadvertently bridged the polarities and created an arc. This has happened before, however the arc was never as explosive as it was today. It created a big boom that the whole plant heard. I checked the ripple on the rectifier, and that was a normal 5%. We changed the diodes too. Is there anything I am missing here? The rectifier is 40v, 750 amp DC output.
Any suggestions will be appreciated.
Thanks,
David Bernardini- Elmira, New York
2002
A. Hi David. What may be missing is effective corrective action -- you don't want to damage parts, racks, and rectifiers via short circuits like this.
You should add some preventative measure -- perhaps perforated PVC, fiberglass or polypropylene sheets that will prevent a recurrence of the operator bridging the polarities. Fiberglass grating hung vertically should work but it is quite expensive; perhaps the thinnest open-est grating you can find; a very light duty corrosion resistant grating is used in fume scrubbers to hold the "wiffle balls" in pace -- maybe you can try to locate some sheets of it.
For normal operation, your exhaust system is apparently adequate to keep hydrogen concentration below the lower explosive limit.
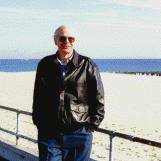
Ted Mooney, P.E.
Striving to live Aloha
finishing.com - Pine Beach, New Jersey
You dunce! (said good naturedly with smile on face).
On previous occasions your operator bridged the rectifier with a low impedance path. (Very bad practice and sometimes very costly) This causes flashes and crackles and may damage the rectifier. On the latest occasion when you heard the loud report (like a cannon going off) you ignited the gasses being given off by the process but most probably did not bridge the rectifier and did no damage to the rectifier.
Let me guess, the acid was 120 to 130 degrees. The load on the tank was quite large, probably over 1000 amps and your iron content is above 3.4%. You probably developed a pretty good size foam blanket over the top of your bath and your cathodes were only a few inches from the parts you were running. In addition, you had poor connections between the bars on the top of your tank and the cathodes/parts or your polishing technician was loading/unloading parts with the rectifier turned on.
You can do this again in a controlled manner. Put on ear defenders and make sure you are wearing safety glasses (just in case). Warn everyone in the vicinity that there is going to be a LOUD noise. Light a piece of paper and apply the torch paper to the foam blanket. It will detonate with a loud report.
The cure is as simple as the explanation. Your acid is approaching the end of its useful life. Change the acid!
The reason is quite simple. Oxygen is given off at the cathodes and hydrogen at the anodes. These gasses collect in the foam blanket. Oxygen and hydrogen will combine explosively, if there is a spark, producing water. The noise can be quite spectacular.
The explosion is usually quite benign and the only side effects are ringing ears and an increase in the laundry bill.
In the old days before we properly understood how to control the foam my technicians have been known to make paper aeroplanes, light them and launch them into the foam blanket. Of course they end the flight with a spectacular explosion and laughs and guffaws all round. Whilst I frown on the practice I could not help a small inward smile when I caught them at it. Come to think of it they have not done that in a few years now and we have that new kid on tank 2. Mmmm... Naw. I am far too mature for that kind of behaviour. Teehee.
John Holroyd- Elkhorn, Wisconsin
A. David,
I think what happened is that the gas from the anode and cathode were ignited. The oxygen and hydrogen can build on the surface of the tank, especially if the tank has a little grease or oil layer then the "magic bubbles" go off with a most startling effect when an arc ignites them. Tributylphosphate is a good defoamer. Handle with care it has safety issues, like most chemicals.
Jon Quirt- Fridley, Minnesota
Q. Thank you for the responses. I understand that oxygen, and hydrogen are given off from the operation, however we run three electropolish tanks, all the same chemistry, and ventilated from the same fan. In addition this tank was only in operation for a week. I thought of this situation, but this has not happened in the last eight years (as far back as we can go) so why all of a sudden? This is why I looked at the power source. (there was nothing wrong with it) The operators typically move the racks back and forth on the bar, creating little sparks, and have never had an "explosion". Not disagreeing with the responses, just want to make sure I am not missing anything. - Dunce
David Bernardini [returning]- Elmira, New York
A. Hey,
Just joking around with the dunce thing. We all did the exploding tank trick at least once. I guess that makes you a graduate too.
The only question left for you to answer is "Was the tank blanketed with foam or otherwise covered when it detonated?"
If the answer is yes to the foam and you had fresh acid then, as Jon Quirt suggested, you probably had oil on the surface of your tank. If your tank is not foaming the gasses dissipate quite quickly. It is only when you get the foam blanket or cover the tank in some way that you could see the problem.
As you have not had this problem in the eight or so years you have been around this process then you probably change your acid in a timely manner or you do not run with big loads on the tanks. We often run for months or even for years without having a "noisy incident". Recently we ran hundreds of large trays without incident but a new operator had a poof on the first part he ran. He was using a slightly different sequence on his procedure and this caused a tiny spark. The result was a very rapid education in flammable gasses and electricity.
I am 99% sure that your operator ignited the gasses. The act of shorting a power supply that can pass 750 amps steady and probably ten times that in a pulse would cause some damage that you would be able to find. A melted rack or a welded spot on a bus bar, that sort of thing. Even then shorting across the bus bars does not tend to cause the detonation that lighting the gasses off does.
John Holroyd- Elkhorn, Wisconsin
I realize you were kidding on the dunce thing. I don't recall the tank having a layer of foam on it, but it could have been overlooked. I did run it myself, with only one rack (I cranked the amps, but we are only talking 200 amps) and got the "boom". I really don't think it foamed much. It is certainly possible that we could have had oil in tank that prevented the hydrogen from escaping, and I will take that stance. I will have the operators keep aware of the foam/oil and its potential.
Thanks for all the help.
Dave the graduate
David Bernardini- Elmira, New York
Multiple threads merged: please forgive chronology errors and repetition 🙂
Arcing in barrel plating
Q. How does arcing occur in barrel plating (Zinc & Clear Chromate)? How can it be prevented? I have parts that tangle quite a bit and have suggested smaller lot sizes so the parts do not ball up. My plating supplier does not think this will fix the problem. Help!
Joe Cammarataspring maker - St. Charles, Illinois, USA
2004
? I think the parts balling up and the arcing are not really closely related; and I doubt that your plating shop is very receptive to reducing the load sizes. The hydrogen pops are probably more closely related to your ventilation system and the 'foam blanket' on the tanks than to the size of the load. But please expound a bit more for us if you don't agree. Thanks!
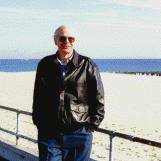
Ted Mooney, P.E.
Striving to live Aloha
finishing.com - Pine Beach, New Jersey
A. We have this problem on our Barrel Plating line (zinc tank). What we found out was we had a bad tumbler in one of our barrels. So we got that fixed and one of our vendors suggested using this smaller scale version of a barrel. So in actuality you have a barrel inside of a barrel, we use this for our smaller parts of course, because you can't fit anything with any size to it inside of these "mini" barrels, and they plate just as well as a part not inside of the "mini" barrel. You also have to watch when that barrel is arcing that is does not cause a hydrogen explosion.
Brian GayletsMcKinney Products - Scranton, Pennsylvania, U.S.A.
QUICKSTART:
The mneumonic, "andode & canthode", helps some of us remember that the anode is positive, the cathode negative :-)
Q. Hi!
I have a problem with electrolytic cleaning. Our process in non-cyanide alkaline zinc plating. During electrolytic cleaning (as I know we have anodic cleaning) too much hydrogen is produced. Due to this we have cyclic mini-explosions which are more and more often. The anode rail is connected to the "-" of the rectifier. Traverse with details is suspended rail which is plugged into a "+" rectifier.
What we can improve to prevent them?
Thank you for your help in advance!
- Poland, Lower Silesia
March 1, 2021
A. Hi Justyna. In the dark ages when I entered this industry, hydrogen pops were a constant occurrence everywhere and no one worried about them at all. Today, at least in the USA, we are far more risk adverse and people worry about starting a fire, splashing an operator with caustic, etc., but at the same time hydrogen explosions have become more of a rarity.
I think the explanation is actually simple. Hydrogen, like all flammable gasses, has a "lower explosive limit" (it's about 4%). It can't/won't explode at a lower concentration than that ... and most plating shops today have more & better ventilation than in the old days. You should have good exhaust ventilation hoods on that electrolytic cleaner, try to minimize any foam layer on the tanks and I think it will end the hydrogen explosions.
Luck & Regards,
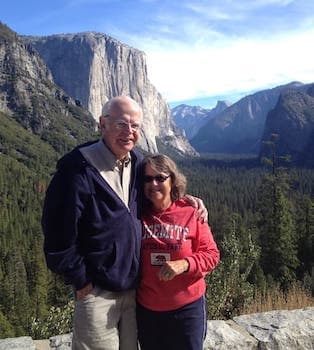
Ted Mooney, P.E. RET
Striving to live Aloha
finishing.com - Pine Beach, New Jersey
A. Ted is right. Electrocleaners used to not be ventilated and people just accepted the small pops that occasionally occurred. New lines nowadays will typically include a hood with a mist eliminator. There is a sweet spot, where you can keep the ventilation flow pretty low and avoid the need for a mist eliminator- just great enough to remove the hydrogen gas, but not so great that it pulls alkaline mist along with it which gunks up the hood. I would think that would probably be around 50 cfm/ft2 and a slot velocity of around 1000 fpm of tank surface area, but that is just an educated guess.
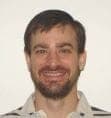
Jon Barrows, MSF, EHSSC
Independence, Missouri
Q. Rebuilding a chem film and anodizing line (post-fire) in California. Sent my proposed chemical inventory to a HAZMAT engineering group and they classified our building as H3/4 Occupancy as a result of the chemicals/inventory levels, very few of which are actually flammable. We have been working with another engineering group to produce the electrical drawings for the building/equipment and are being told that we must meet "explosion proof" requirements throughout the building - meaning sealed conduits and explosion proof enclosures/control panels/etc. because the anodize tank generates hydrogen. The local air quality board is already requiring us to have exhaust ventilation over the anodizing tanks at a rate of 4180 SCFM per tank. I have not seen any other plating facilities with those requirements (in electrical parlance, Class 1, Division I of the NEC code). About half the facilities I have been to here in the SOCAL area actually have very little tank-specific ventilation - only building ventilation. Does anyone have any experience with this issue. Just how bad is the hydrogen generation during anodize, and in the presence of 4180 SCFM direct-over-tank exhaust ventilation, would it be any kind of an explosive hazard?
Mike Palatas- Gardena California
May 3, 2021
A. Hi Mike. I designed hundreds of plating & anodizing installations in my career and visited & studied probably several thousand, and never heard or saw one required to use explosion proof wiring & fixtures due to hydrogen (although a few did due to use of flammable solvents).
The lower explosive limit for hydrogen is 4%, so, while 'pops' can happen right at the tank surface on non-ventilated tanks or tanks with a lot of foam, it's hard to imagine a significant accumulation of air with 4% hydrogen in it from an anodizing line.
For several years I was "the plating shop guy" for a service firm that did fire investigations for the insurance industry. Virtually every shop fire is caused by electric heaters in polypropylene tanks ... so it bothers me when we are instructed to mis-focus and concentrate on things that have never happened and probably never will, diverting attention from the real & present dangers we should be hammering home ... especially at a time when more and more shops are moving to polypropylene tanks, while being pressured to heating them with electricity :-(
Lots of anodizing tanks have local ventilation, but whether 4180 SCFM is appropriate is hard to say without knowing the surface area of the tanks and other details.
Luck & Regards,
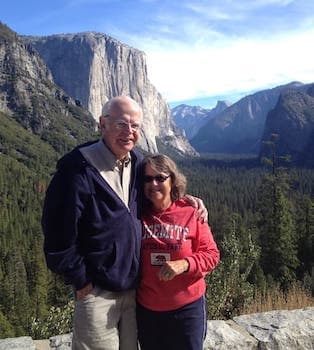
Ted Mooney, P.E. RET
Striving to live Aloha
finishing.com - Pine Beach, New Jersey
Q, A, or Comment on THIS thread -or- Start a NEW Thread