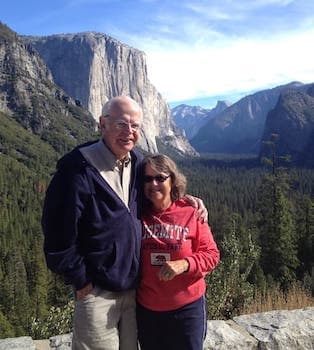
Curated with aloha by
Ted Mooney, P.E. RET
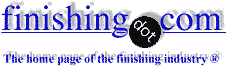
The authoritative public forum
for Metal Finishing 1989-2025
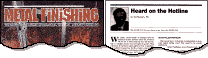
-----
How do I chrome
How can I learn to chrome and is it a difficult process? I need to learn for a course in the higher school certificate.
Harris Barrington- Sydney, Australia
I would not suggest actually doing it. Chrome plating requires very hazardous chemicals that must be handled and disposed of properly. If you need to learn about the process for school, I would start with the Metal Finishing Guidebook published by Metal Finishing Magazine. Also, see if there is a chrome plating shop near you. Maybe you can convince somebody to give you a tour.

Tim Neveau
Rochester Hills, Michigan
I would agree that trying to chrome plate is not for the amateur and definitely not for the home. However, the principles are reasonably straightforward. Depending on what the chrome is for, the precoating is important. In general, chrome plating is mainly done for decorative purposes, although there is a quite big market for engineering coatings. In decorative coatings the layer is very thin and often needs sub-layers to protect the substrate from corrosion. In thicker engineering coatings, a sublayer is needed to promote adhesion. Chromium deposits tend to be very highly stressed and therefore do not always stick to the substrate very well. For decorative purposes, the substrate, say mild steel, should be coated first in copper, preferably using cyanide copper as that gives the best adhesion. This is then coated with nickel. Depending on the end-use, it can be a single of double layer. For best results, use a double layer, or duplex nickel. This comprises one layer of columnar nickel and one layer lamellar nickel. The lamellar nickel gives a better surface finish but is not as corrosion resistant. These layers need to be reasonably thick to ensure no corrosion takes place. The nickel is then plated with chromium.
Chromium plating can be done from two types of system, trivalent and hexavalent. Trivalent chromium was the first system to be used back in the C19th, but it can only put down very thin layers and is not very consistent in colour. However, a lot of work is being done to solve this problem and many supply houses now offer good systems, but they are not really suitable for thicker, engineering, uses. The current densities are much lower than for hexavalent chromium (40-150ASF).
Hexavalent chromium was developed in 1926 and uses a mixture of 100:1 chromic acid (CrO3): H2SO4. This ratio is very critical and if it is out, the system does not work. Typical current densities are quite high (150-300ASF) and the baths operate at about 50 C. The efficiency is quite low, being about 20-25%, but there are additives that can improve this slightly. Hexavalent chromium salts are very nasty; they can attack the septum in the nose and destroy it, a bit like cocaine does. There is also some evidence that hexavalent chromium can cause cancer, but this is not fully substantiated. The solutions are extremely acidic and will attack almost anything. When electrodepositing chromium, it is usual to use lead anodes, which are not really attacked, although they do develop a yellow lead chromate layer on them. Again, this is regarded as being very toxic, both from the chromium and lead standpoint, but it is very insoluble in water.
There are some excellent reviews of chromium plating around, so I would suggest you trawl the Internet for further information. One good source is the Metal Finishing handbook (Metal Finishing Guidebook and Directory Issue), or of course the Canning Handbook on electroplating.
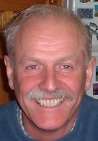
Trevor Crichton
R&D practical scientist
Chesham, Bucks, UK
Q, A, or Comment on THIS thread -or- Start a NEW Thread