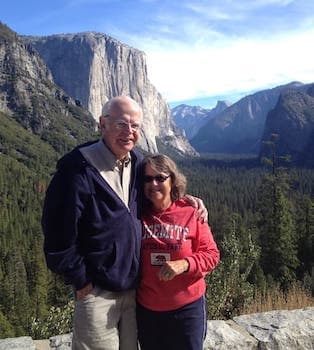
Curated with aloha by
Ted Mooney, P.E. RET
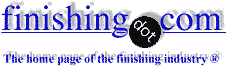
The authoritative public forum
for Metal Finishing 1989-2025
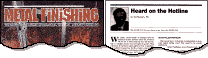
-----
Black Anodize Problems. Can MIL-A-8625 Class II help?
We are having problems with a number of platers that are located on Long Island. We indicate on our drawings to plate our alum. parts to MIL-A-8625 / MIL-PRF-8625 [⇦ this spec on DLA] Class II as it applies to Black Anodize. These are our issues. We receive parts that once exposed to ultra-violet light, within a couple of days the parts start to fade. We also receive parts that are blue and not black as required.
Question: Can this spec be used to enforce that are requirements are met? If so, which paragraphs will apply? How is the problem with fading controlled, eliminated all together or increase the life span. How can we stipulate that the color be black and not blue. What about the quality of dyes used and internal controls used by platers. Is this spec sufficiently worded to control these problems?
Bill Velazquez- Hauppauge, New York
I'd like to comment on the last query regarding the parts you received which are supposed to be black but are rather blueish. If you specified black, I think whatever MIL specs you agreed on, the parts simply do not meet your requirement. By the way, that blue color is more often caused by inadequate coating thickness. To get a good black color, thicker coating (relative to other colors) is required.
Dado Macapagal- Toronto, Ontario
I concur with the last comment. If the black that is being used is a quality product and kept to manufactures spec, then variable coating thickness is the answer. In my opinion it is the answer most of the time when dying parts. Inconsistent coating thickness will always vary the end dye color. Coating thickness can be controlled in a properly designed and controlled anodizing system.Tell your supplier to tighten up his procedures or you'll move on. By the way if your always beating on him to lower his price that could be part of it.
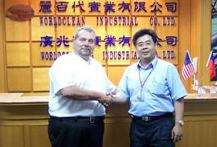
Drew Nosti, CEF
Anodize USA

Ladson, South Carolina
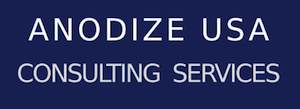
Drew,
While I agree with your technical assessment of the potential causes of his inconsistent looking anodized parts, I have to take issue with your last comment regarding pricing. Nowhere in his letter did I see any mention of pricing issues. We live in a very competitive world, and pricing will always be a concern, but it is NEVER an excuse for poor quality. A good coater will quote a job, and..once the quote is accepted, will produce a finish meeting the customers specs.
Now..I'll put my 2 cents in on possible causes of his problem. Coating thickness, improper seal, poor dye control, using the wrong dye for the job, and the fact that some alloys are difficult to anodize (you didn't mention your alloy, Bill)..all of these could be causes of the problem.
Bill.. If I were you.. have your coater provide proof that his coatings meet the required mil-spec. If a coater CERTIFIES that his coatings meet the spec, that means he should be able to provide you with documentation that he has sent his coatings out to an independent lab for certification, and these documents should be in his files. Ask your coater to provide certification with each batch, and ask him to fax you confirmation that his coatings meet these requirements. This is not an unusual request, my company does this on a very frequent basis (provide certs with the job).
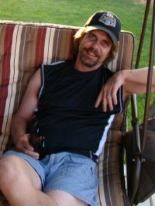
Marc Green
anodizer - Boise, Idaho
The MIL-A-8625 sets the minimum for acceptable anodic coatings. Color and color uniformity as well as light fastness are barely addressed. These requirements are to be specified "... on the contract, purchase order or applicable drawing." Therefore, the particulars on these issues must be dealt with outside of the specification. A properly certified coating may still not meet a customer's needs. I would suggest setting up visual standards for acceptable color ranges and adding a light fastness test.
PS. There is no requirement that certification or testing be done by outside laboratories.
Chris Jurey, Past-President IHAALuke Engineering & Mfg. Co. Inc.

Wadsworth, Ohio
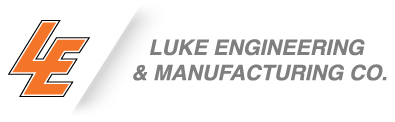
Whoa! I just reread your original question. You do not state what Type of anodize is specified. Most responses seem to assume a Type II sulfuric anodize. Type I chromic acid is a whole different story. Many anodizers, including me, would argue that a good Class 2 black is impossible with Type I. However, due to environmental considerations and shrinking demand, Luke Eng. got out of this business several years ago. New developments may have improved this situation.
Chris Jurey, Past-President IHAALuke Engineering & Mfg. Co. Inc.

Wadsworth, Ohio
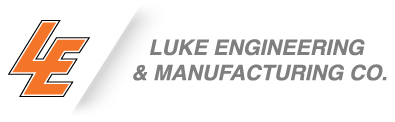
Hi guys,
Things he should discuss with his anodizer and they all somewhat echo what you guys mention. I also noted to him that some black dyes are formulated with a blue base, and others with a red or green base. You can tell this easily by dying very thin anodized parts. I think he's pretty well got all the ammo necessary to figure out the issue and together we've covered pretty much all the bases.
Matthew Stiltnerplating company - Toledo, Ohio
While Chris is correct, that the spec does not go into detail about color/lightfastness, some of the things the spec does require could directly relate to the problems he is having, i.e., coating weight, thickness (I'm not 100% sure thickness is specified on the type II spec), and seal quality. The spec, unfortunately, normally requires said testing to be carried out on 2024, and 7075 (for type 3) alloys, which can be a challenge to anodize without proper equipment/parameters. I'll be honest, I haven't completely compared the new revision F to the D version, so there may be some changes..does anyone know the differences? (I'm feeling lazy). And..once again, Chris is correct that the spec may not meet the customers actual needs, but.. if that is the case, the customer needs to state what his needs are, as opposed to referencing a Mil. spec. And yes.. I too, have assumed that he was referring to Type II coatings.
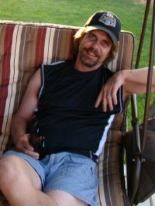
Marc Green
anodizer - Boise, Idaho
Q, A, or Comment on THIS thread -or- Start a NEW Thread