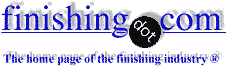
-----
Zinc sulphate Plating vs. copper sulphate Plating-7th grade science project
My son (13 yrs) is doing an electroplating experiment for his 7th grade science class. He is trying to see which solution will plate a metal ingot better (more durable): a solution of tap water and copper sulphate ⇦ on eBay or Amazon [affil links] or a solution of tap water and zinc sulphate ⇦ on eBay or Amazon [affil links] . He is using a piece of copper tubing suspended into the solution and a 12-volt battery. After each solution has had a chance to "cook" for 40 minutes, we find that the zinc sulphate solution appears to have coated the metal ingot more fully and it is also more durable. After rinsing each ingot with running water, the copper plating washes off. The zinc plating, while not thick or 100% coated onto the ingot, adheres better.
Why would this happen? What makes the zinc coating more durable than the copper? We think it has to do with the properties of the individual metals, but cannot find any info on the subject. His project is due in 2 weeks and we need to have a better conclusion. Can you help?
Thanks very much!
Elise Mikus- Dallas, Texas
I'm unclear as to what the "ingots" are made of (presumably steel?) and what the role of the piece of copper tube is (I guess it's the anode, but zinc should be used for the anode when zinc plating), so we have to make some guesses.
Zinc will not deposit on the ingot without electricity being applied; therefore the electroplating is engineered, the zinc ions in solution are reduced to zinc metal precisely at the interface, under your conditions, in proportion to the electricity you apply.
To the contrary, copper is more noble that your ingots and what happens is that even without electricity being applied, some of the surface of the ingot is dissolving into the solution and the copper coming out of solution in proportion, depositing in its place. This happens out of your control at whatever rate it feels like. This undercutting of the metal onto which the copper is trying to adhere means adhesion will be terrible.
In commercial practice--your son can tell the teacher-- copper is not electroplated from simple salts onto steel, aluminum, or zinc for exactly the reason that you are discovering.
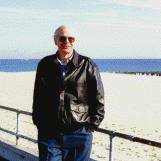
Ted Mooney, P.E.
Striving to live Aloha
finishing.com - Pine Beach, New Jersey
Q, A, or Comment on THIS thread -or- Start a NEW Thread