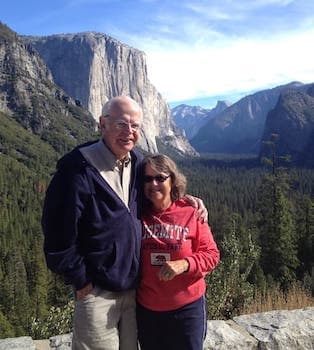
Curated with aloha by
Ted Mooney, P.E. RET
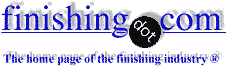
The authoritative public forum
for Metal Finishing 1989-2025
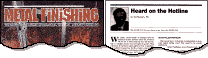
-----
High % Tin on Burnt plating
Q. I just started working in a semiconductor company that assembles integrated circuits. In solder plating tin-lead on leadframes using a continuous type plating machine, increasing the gap between leadframes will have a drastic effect. Burnt plating is a result of this. Plating thickness measurements on high current density regions such as the ends of the leadframes where there is a large gap were high. I also found out that these regions had very high percentage tin. Plating thickness and percent tin were normal in the middle region of the leadframes. I would really like to know what is the cause of this increase in percent tin in the HCD regions.
Thanks,
Ramon Navarro- Philippines
A. Hi Ramon. You plate at a much higher current density than a rack plater could, and are able to do so by minimizing the thickness of the boundary layer through which the metal ions must slowly diffuse. You achieve this high current density and minimal boundary layer through agitation, rapid turnover, and close anode to cathode spacing. As soon as you do something that allows the boundary layer to thicken you will get burning because the ions cannot diffuse through it fast enough. The electrons are there on the cathode, demanding to neutralized, and without tin and lead anions available, they'll steal hydrogen atoms from the water.
Alloy ratios are always affected when you change things because one metal is more noble and wants to deposit in preference to the other. This tendency must be carefully held in check. Lead is more noble than tin, but high current densities tend to shift the deposit to the less noble metal.
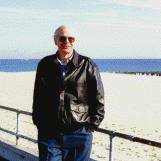
Ted Mooney, P.E.
Striving to live Aloha
finishing.com - Pine Beach, New Jersey
Q. Thanks. When high current densities occur, why does the process favor the deposition of the less noble metal?
Ramon Navarro- Philippines
Look at it from the other direction: the nobler metal always wants to deposit preferentially, that's why we call it the nobler metal, right? So to keep things in desired balance, you need to ration how many noble ions are in solution. If the current density is very low, after one atom of the noble metal plates out preferentially, there is time enough for others ion to migrate to that spot and for the process of preferential plating of the nobler metal to continue. But at higher current density, when the electrons on the cathode are hungry to reduce whatever they can get their hands on, they'll grab an ion of the base metal because there is no noble metal ion there right now.
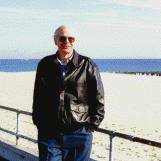
Ted Mooney, P.E.
Striving to live Aloha
finishing.com - Pine Beach, New Jersey
May 28, 2013
Q. I have tin-lead (60Sn40Pb specified) plating supplier who was plating small brass standoffs. My first problem was that the plating flaked off when the standoff was being swaged onto a flex circuit. As a result of this flaking we did an elemental analysis of the plating which determined a worse problem-the plating was from 98-99% tin which now causes tin whiskers concerns. The plater has stated that he miscalculated the surface area setting the amperage too high and therefore causing too much Tin to be "thrown" onto the standoff. Does this explanation make sense? Thanks for any help.
Bill Pinzon- Greenlawn, New York, US
A. Hello Bill,
If the current density for the bath was way too high, it will affect the alloy ratio of the bath. When a plating bath is formulated, the supplier has certain range specs for metal, acid, salts, anode composition and current density. A burned deposit can also cause the peeling you experienced.
Process Engineer - Mesa, Arizona, USA
June 5, 2013
Q, A, or Comment on THIS thread -or- Start a NEW Thread