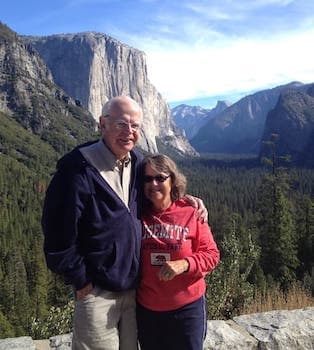
Curated with aloha by
Ted Mooney, P.E. RET
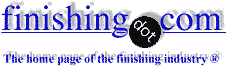
The authoritative public forum
for Metal Finishing 1989-2025
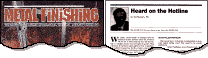
-----
Bias sputtering
Q. I would like to know if someone can explain me what bring a bias magnetron sputtering ( in comparison with a simple magnetron sputtering).A DC bias on the anode, and RF on the cathode.
Thank you,
Maï MARQUES- Compiegne, FRANCE
2002
2002
A. All sputtering requires a negative bias on the target to create the sputter plasma by ionizing the gas and draw the ions to the target. Sputter yields depend on ion energy (bias voltage). For argon, the most common gas used in sputtering, the sputter yield on most materials peaks around 1 kV. If the sputtered material is not conductor, the bias won't hold. In such cases, a pulsed bias, usually RF, is used. Lately, researchers have been having good success with "pulsed dc" biasing, i.e., biasing at very low frequency compared to rf. The only time a bias is not needed is when an ion beam is used in lieu of a trapped plasma.
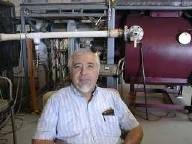
Jim Treglio - scwineryreview.com
PVD Consultant & Wine Lover
San Diego, California
Q. Dear James,
Thank you for your response but I think that I was not clear. When I say Bias, I mean Bias on the substrate, actually we have got a bias on the target (RF).
Best Regards,
Maï MARQUES [returning]- Compiegne, France
A. To get the coating to adhere, you need to bias the substrate. If the coating is a non-conductor, a pulsed bias is needed. Otherwise, you can use d.c. You need two levels of bias. A high voltage bias (around 1000 V) should be used before you start the deposition to sputter clean the surface, and a lower level during deposition. Note that the bias only works if you have some level of ionization near the substrate. Your bias voltage for sputter cleaning must be high enough to create a glow discharge in the chamber. You may not need a glow discharge during the deposition phase if sufficient ions are arriving from the source.
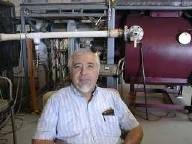
Jim Treglio - scwineryreview.com
PVD Consultant & Wine Lover
San Diego, California
A.
You need to look into the subject of ION PLATING which gives the advantages and disadvantages of ion bombardment during vacuum deposition.
Donald M. MattoxSociety of Vacuum Coaters
Albuquerque, New Mexico
"Handbook of Physical Vapor Deposition (PVD) Processing" (2010) [on AbeBooks or eBay or Amazon affil links]
and "The Foundations of Vacuum Coating Technology" (2018) on AbeBooks or eBay or Amazon affil links]
A. The bias sputtering help to retrieve a better film. The bias voltage causes the ions that are created between the bias layer and the substrate, to be accelerated towards the target. Bombarding the target makes a more compact film and will push away the molecules that are not good attached into the film.
Anila Gottschling- Köln, Germany
Q. Is pulsed DC bias useful in metal film sputtering deposition on conductive substrate?
David Xu- Fremont, California
July 1, 2010
Q. I am P.G. student, I am working on thin gold deposition on silica substrate using RF sputtering, How we can obtain minimum surface roughness, what parameter should be varied to obtain this?
Shriniwas Yadav- Jhunjhunu, Rajasthan, India
May 1, 2012
A. Sputtering process does not affect the roughness of the film. It maintains the surface finish of the substrate.
H.R. Prabhakara - ConsultantBangalore Plasmatek - Bangalore Karnataka India
May 2, 2012
Q. Why do we usually use argon in the chamber for ionization process, rather than other gases in the same group with argon?
Zurita Zulkifli- Kuala Lumpur, Malaysia
July 4, 2012
A. Argon is cheaper.
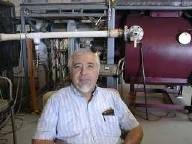
Jim Treglio - scwineryreview.com
PVD Consultant & Wine Lover
San Diego, California
July 9, 2012
Q. Hi, I am trying to figure out what is the "bias" indication I read on my RF source and how it affects the final product (thin film). Consider that in the Magnetron Sputter I am using there's not the possibility to apply a DC (or RF) bias to the substrate, nor the generator is connected to the (grounded) sample holder... this bias must be related to something else then.
i.e.: if I apply a 60 W RF power to the sputtering cathode, I read up to 35 W on the bias display, and I cannot modulate (reduce or increase) it ... it must be something related to the system.
So the question is: what the bias the RF generator displays is? A bias on the target?
- Longarone, Belluno, Italy
November 14, 2012
Q. To clean the surface is the 1000V positive or negative on the substrate, and to adhere the film is the subsequent lower voltage positive or negative?
Thanks!
- Watlington, Oxon, UK
August 24, 2013
![]() |
A. Bias is always negative. ![]() Jim Treglio - scwineryreview.com PVD Consultant & Wine Lover San Diego, California August 27, 2013 A. Negative in both cases. The first large negative bias is for both cleaning and adhesion while the second is for getting required crystalline structure assuming that you are talking about some PVD process. H.R. Prabhakara - ConsultantBangalore Plasmatek - Bangalore Karnataka India August 27, 2013 |
Q. How does DC bias apply to a dielectric substrate? Current cannot pass through insulators.
Navdip Singh- Santa Barbara, California USA
May 12, 2017
Q. I am attempting to utilize the DC Bias capability on an old MRC sputtering machine. The literature describes a bias current of about 500-700 mA when the target is running around 7-10 kWatts. We typically run 7 kW when sputtering Ti. Right now we are only seeing about 150 mA of Bias current.
The issue we are trying to resolve is the appearance of nodule during the Ti deposition, which then are telegraphed up into the subsequent depositions. The idea is applying some bias to the platen will improve the surface mobility of the Ti and theoretically improve the surface condition. The melting point of Ti is very high, so we are easily still in Zone 1 on the Thornton model...trying to get into Zone 2 with the additiuon of the bias (can't raise the ambient temp)
So the pointed question is about the low bias current (I think the electrical path is good).
The big question is getting rid of the nodules.
Thanks for any comments!
Littelfuse Reed switch production - Lake Mills, Wisconsin, USA
June 14, 2017
![]() |
A. The bias current depends on how much of the gas in the chamber is ionized around the substrate, size of the substrate, bias voltage, geometry of the substrate and other factors. In other words, you need to provide a lot more information for anyone to be able to help you. ![]() Jim Treglio - scwineryreview.com PVD Consultant & Wine Lover San Diego, California June 19, 2017 A. Sputtering is not expected to deposit nodules on the substrate. Probably the magnetron is going into arcing mode occasionally. Best way to avoid this is to use a high frequency pulsed DC source for sputtering. One can also try optimising operating parameters. Substrate biasing is unlikely to solve the problem. On the contrary depending on the operating parameters there could be arcing even on the substrate. This should be avoided by working in a proper regime of operating parameters and using suitable bias supply. Substrate bias current depends on the magnetic field configuration and operating conditions. For example it would be high when unbalanced magnetron is used. Add atom mobility improves the quality of the films by shuffling the atoms on the surface. It is unlikely to disturb the nodules which,I suppose, are macroscopic in nature. H.R. PrabhkaraBangalore Plasmatek - Bangalore, Karnataka, India June 20, 2017 |
Q, A, or Comment on THIS thread -or- Start a NEW Thread