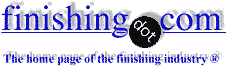
-----
Rapid Corrosion of Stainless Steel in oil separation plant
We are currently constructing an oil separation plant for Sullage ( a combination of 75% sea water and 25% waste oils from the bilges of ships). The process involves chemical treatment of the sullage, removing the oils as sludge. The plant is constructed of Grade 316L Stainless Steel. The latter part of the process scrubs the effluent sea water through a aerated washed sand filter and then aerated charcoal filters, at which point the material is nearly 100% sea water and slightly alkaline. We now have severe corrosion in the two filter stages which has manifested within two months of material being passed through. We are aware of micro-organisms existing in the sullage. Is this microbiolohgical influenced corrosion ? and if so why does this not occur in the earlier stages of the process? What remedial measures can be taken?
Geoff Willcocks- Plymouth, Devon, United Kingdom
A guess: In plating, the greatest attack is at the air-liquid interface. You have substantial oil to prevent/reduce corrosion in the early stages. In the latter stages, there is very little oil and a significant air/liquid/tank interface. Solutions-Fiberglass? Polyethylene liner? plastisol? heat set vinyl? Do away with the air?
James Watts- Navarre, Florida
Hi Geoff,
You have a most interesting problem. This could be caused by a number of things but lets try the most likely explanations first.
According to your description this problem occurs in the filters only and not any other place in your system. Assuming that the pitting takes place all over the inside of these two filters and that they were properly fabricated and passivated prior to use we must search for what is different in the filters than in the rest of your system.
It seems possible that you are getting abrasion of the passive film on the stainless steel from the media in your filter stages. This could occur during normal running or during backwash. If you breach the passive film during any part of the process the film will not reform in sea water, because of the attack of chlorine ions. Once pitting begins it will continue. Passivation may help, electro-polish would be even better. Trouble is that the problem will recur if it is caused my mechanical damage during running. Reducing velocities through the filters may help minimize surface damage but you may have to periodically repassivate as well.
Bacterial attack is not normally this rapid and normally takes place in the surface slime that forms in stagnant tanks containing water and nutrients (hydrocarbons would be ideal). This would not be among my first choices unless there are long periods when the system stands idle. If you have long periods between runs while the system stays filled with sea water you have an ideal system to set up slime forming colonies which will attack stainless steel. The carbon filter in particular is a place that would encourage slime growth (carbon source + sea water). Periodic sanitization is necessary to fix the problem, I would suggest steam or very hot water followed by nitric acid passivation. Do not use cold chemical sterilants such as sodium hypochlorite as they will simply provide more attack of the surface.
I would consider using different material than 316L for the filter stages. You could try Hastelloy, seacure, or titanium. It is probably not a good idea to try copper nickel alloys, even though they are excellent in sea water, because they are also very sensitive to surface abrasion damage caused by entrained solids and/or high velocities and they also are very prone to attack in media containing sulfur ⇦ on eBay or Amazon [affil links] (bilge oils contain sulfur).
I hope these comments prove to be of some use to you.
Good luck,
John Holroyd- Elkhorn, Wisconsin, USA
Dear Geoff,
I am strongly supporting the suggestion of Mr.Holroyd but think that it is very difficult ti use any coating here for a lot of reasons. As titanium expert I would advice to use proper titanium alloy here. It is necessary however to check it "in sity". Titanium alloy with or without oxidizing treatments would be supposedly your right choice.
Andrey Igolkin- St.Petersburg, Russia
Dear Geoff,
From what you have said, I believe that you will require a protective coating. We use a nylon coating from a coating company in Sydney Australia. It has stopped all tea staining on stainless that we install near the ocean.
Steven Scarpin- Melbourne,Victoria, Australia
Q, A, or Comment on THIS thread -or- Start a NEW Thread