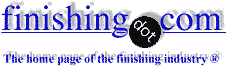
-----
Sand blasting standards: Swedish SA 1, SA 2, SA 2.5, SA 3 vs. NACE and Ra
Q. I need to know about surface preparation, about sa 1, 2, 2.5 and 3.
And application method, paint defects, what is the meaning of 417, 519 for spray?
Junior coating Advisor - Dhaka, Bangladesh
June 5, 2021
A. Hi Rani. The SA sand blasting standards are clearly (I believe) explained by Bijit Sarkar below, and there is a lot of detail on this thread. Hopefully it will help.
We also have many threads here about spray painting, and application methods, and paint defects -- please try the search engine.
Unfortunately your numbers "417" and "519" don't mean anything to me. Can you give us some context please? Please try to give us a couple of paragraphs about your situation. Thanks :-)
Luck & Regards,
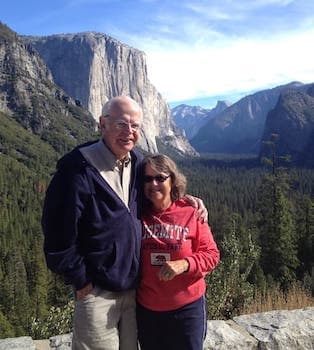
Ted Mooney, P.E. RET
Striving to live Aloha
finishing.com - Pine Beach, New Jersey
⇩ Related postings, oldest first ⇩
Q. I need to know the technical details about the following- Surface preparation - Cast Iron part (gratings, used for cooking ranges); the surface needs to be prepared by sand blasting as per Swedish Standard, SA 2.5 or better as per Swedish Standard, SA 3. If it is possible then please inform about the surface finish value (Ra, Rmax) which can be achieved by the above mentioned process.
Please respond as early as possible.
Best Regards,
Souren Palsteel company - Ahmedabad, Gujarat, India
2002
![]() |
Q. Dear Mr. Souren Pal, I am also interested in the relationship between the SA standards SA 1, 2 2.5 and 3 and Ra. An interesting answer on your question which may be of help to me? Best Regards, Laure Spriensma- Jirnsum, The Netherlands Q. I WOULD LIKE TO INQUIRE INFORMATION REGARDING SAND BLASTING PROCEDURES, EQUIPMENTS AND MATERIAL, AS DESCRIBED IN SWEDISH STANDARD SA1, 2, 2.5, 3? YOUR COOPERATION ON THIS MATTER WILL BE HIGHLY APPRECIATED. FADI MUSALLAM- ABU DHABI, UAE |
A. Mr. Souren Paul , Laure Spriensma, Mr. FADI MUSALLAM,
Surface preparation standards are stipulated by various bodies throughout the world to designate the cleanliness condition of blasted steel, prior to applying a protective coating. The applicable cleanliness standard is usually called for by either the protective coating manufacturer or the owner of the structure to be painted. The most commonly referred to standards are SSPC, NACE, and Swedish Standards. Each standard is divided into four standards of cleanliness, broadly described as follows; brush off, commercial, near white metal, white metal. Whilst each standard may differ slightly in requirements and terminology the following cross reference chart indicates the close approximation of each level of cleanliness for each standard.
- BRUSH OFF, NACE No. 4/SSPC-SP7, SWEDISH Sa.1
- COMMERCIAL, NACE No. 3/SSPC-SP6, SWEDISH Sa.2
- NEAR WHITE METAL, NACE No. 2/SSPC-SP10, SWEDISH Sa.2.5
- WHITE METAL, NACE No. 1/SSPC-SP5, SWEDISH Sa.3
A brief description of each of the four levels of cleanliness is as follows:
- Brush Off - Loose mill scale, loose rust and foreign particles are removed.
- Commercial - Mill scale, rust and foreign particles are substantially removed and grey metal is visible.
- Near White Metal - Mill scale, rust and foreign particles are removed to the extent that only traces remain in the form of spots or stripes. The cleaned surface will show varying shades of grey.
- White Metal - Visible mill scale, rust and foreign particles are entirely removed. The cleaned surface should have a uniform metallic colour but may show varying shades of grey when viewed at different angles.
I hope the above info is useful to you. We are setting up a shipyard and are installing a plate preparation shop.
Regards,
Bijit Sarkarshipbuilding - Calcutta, WB, India
2004
![]() ![]() ![]() |
Q. May I know the surface profile difference between SA 2.5 and SA 3 in microns? Shahaji Doltade- UAE 2007 A. Dear Mr. Shahaji Doltade - Karachi,Pakistan February 17, 2012 Q. Dear sir, - student - ROHINI, DELHI, INDIA March 19, 2010 A. Hi, Prashant. The above discussions lead me to believe that Sa2.5 is not a "surface finish" but a visual standard for cleanliness and is not related specifically to grit size and surface roughness standards like Ra / Rz, and it cannot be measured with a profilometer. Do you have a copy of ISO8501-2 handy, with its description of Sa2.5? Thanks. ![]() Ted Mooney, P.E. Striving to live Aloha finishing.com - Pine Beach, New Jersey Q. Thanks for the information that SA 2.5 is not measurable in Ra, but we have seen specifications, such as in containers manufacturing that surface finish to SA 2.5 to achieve 25 to 30 micron finish. Is it correct? S P S DHINGRA- Kolkata, India May 5, 2010 A. Hi, S P S. You can't measure the things that are covered by Sa 2.5, like discoloration, visible oil, and greyness with a profilometer. Nor should we reasonably expect a given surface profile to consistently result simply by complying with a blast cleaning specification that is unconcerned about it, and which apparently permits the use blasting grit of any material, any size, and for any amount of time. However, you can certainly specify both the Sa 2.5 requirement AND a given surface finish! Just as specifying that an automobile be red in color doesn't specify how many seats it must have, but you can certainly require both that it be red and that it have 5 seats. Good luck. Regards, ![]() Ted Mooney, P.E. Striving to live Aloha finishing.com - Pine Beach, New Jersey |
A. I hope this will clear your queries on Blasting and surface preparation..
BLAST CLEANING - PREPARATION GUIDES
grade - BS 7079 SS 05 59 00
description, when viewed with the naked eye
- SA 2
- thorough blast cleaning:Commercial finish 65% clean
The surface shall be free from visible oil, dirt and grease, from poorly adhering mill scale, rust, paint coatings and foreign matter. Any residual contamination should be firmly adhering.
- SA 2.5
- very thorough blast cleaning: Near white metal 85% clean
The surface shall be free from visible oil, dirt and grease, from poorly adhering mill scale, rust, paint coatings and foreign matter. The metal has a greyish colour. Any traces of contamination shall be visible only as slight stains in the form of spots or stripes.
- SA 3
- blast cleaning to pure metal: White metal 100% clean
The surface shall be free from visible oil, dirt and grease, from poorly adhering mill scale, rust, paint coatings and foreign matter. The blasted surface must have a uniform metallic colour.
BLASTING GRADES
Following is a table giving a clear indication of the comparative blasting grades applicable to national and international standards:
BLASTING GRADE COMMON STANDARDS COMPARISON
SSPC steel structures painting council
BS 7079 British standards
SS 05 59 00 Swedish standards
BS 4232
NACE, National Association of Corrosion Engineers
white metal (SP5) SA 3
1st quality
grade 1
near white metal (SP10) SA 2.5
2nd quality
grade 2
commercial finish (SP6) SA 2
3rd quality
grade 3
- RUST GRADES
- A Surface mostly covered with adherent mill scale, with little or no rust
B Mill scale has begun to flake, rust has started to form
C Mill scale has rusted away or can be scraped off easily and slight pitting has taken place
D Mill scale has rusted away and general pitting can be seen with naked eye
- Baroda, Gujarat, India
November 1, 2008
Q. Dear sir
We want photographs of standard blasting profiles like Sa 2, Sa 2.5, Sa, 3 etc.
Regards
- coatings - Vadodara, Gujarat, India
June 11, 2009
Q. I want sand blasting profile books for SA2 and 2 1/2 with complete pictures. Please let me know where can I find this.
Thanking you in advance.
- contractor - Vizag, AP, India
August 13, 2009
A. Hi Kirit; hi Shivaraju.
HMG Paints Ltd. offers a free 24-page PDF with pictures of these surfaces at:
https://www.hmgpaint.com:443/PDF/knowledge-base/KNB0026.pdf
But I think you'll want to try to get a look at ISO-8501-1, which is a hardcover 74-page book, and the actual official reference.
Regards,
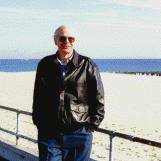
Ted Mooney, P.E.
Striving to live Aloha
finishing.com - Pine Beach, New Jersey
Q. I want to know what the term "Sa" in blasting standards actually stands for.
My boss always asks me and I cannot answer. Help me please...
Painting Executive - Johor, Malaysia
August 26, 2009
A. SA stands for Standard Abrasive ... Similarly ST means Standard Tooling
Rahul T.- Mumbai, India
A. Sa Simply stands for Sand as that is the abrasive medium that they used to determine the blasting standards on the 4 Rust Grades for ISO 8501-1.
Remember Sand was the most widely used abrasive back in the days before the health risks of silicosis were identified.
Alternatively St stands for Steel sorry its nothing more technical, but that's it guys, and the reason I know is that I asked SIS years ago when I first started Inspection to settle an ongoing debate between myself and a colleague.
The relationship between the standards Sa3 and 2.5 is practically identical except that a 2.5 allows for staining or traces of contamination i.e. Very thorough blast cleaning. When viewed without magnification, the surface shall be free from visible oil, grease and dirt, and from mill scale, rust, paint coatings and foreign matter. Any remaining traces of contamination shall show only as slight stains in the form of spots or stripes.
And Sa3 does not have any visual contamination present it is a white metal finish.
For a more definitive view at amounts of contamination which are allowed visually to be included in a blast please take a look at the joint Nace SSPC blasting standards which are equivalents, however not identical to the ISO 8501-1 standards. These standards give a better representation of the actual amounts of contamination which should be present.
Nace 1, SP5, Sa 3 = 0%
Nace 2, SP10, Sa2.5 = 5% Staining
Nace 3, SP6, Sa2 = 33% Staining
Nace 4, SP10, Sa1 = 100% as long as its tightly adherent
inspection services - United Kingdom
Thanks a lot everyone. It was really helpful.
- Bangalore,Karnataka, India
Q. Dear Sir,
I want to know about the detail of SA 2.5 about blasting for steel equipment.
Regards,
project engineer - Chennai,Tamil Nadu, India
June 4, 2010
A. Hi, Shanthi. The general meaning of Sa 2.5 is explained above.
My understanding is that the full details are covered by specification SS 55900, available from the Swedish Standards Institute at www.sis.se -- but that this standard was actually canceled in 2001 and is now superseded by ISO 8501-1.
Good luck.
Regards,
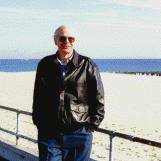
Ted Mooney, P.E.
Striving to live Aloha
finishing.com - Pine Beach, New Jersey
A. The blasting standards as depicted in ISO8501-1 are visual standards for surface cleanliness
Once a substrate is abrasive blasted the blast achieved is then compared to the visual reference pictures which are contained within ISO8501-1 and a comparison made between the blasting standard achieved and the standard required.
When you speak of Ra you are speaking of surface profile, roughness or anchor pattern which is the peak to trough amplitude of the blast profile usually expressed and specified in microns and created during the blasting process this is usually measured with surface replica tape, surface comparators or surface profile needle gauges however surface profile is not an indication of the surface cleanliness do not get confused surface profile and surface cleanliness as depicted in ISO8501-1 are separate requirements.
I hope that this helps
Best Regards
inspection services - United Kingdom
Q. I would like reference/guidance for the relation between cleanliness standard with steel structural condition/type. Example: SA-2.5 is applicable for a structure on what conditions? Or what grade is suitable with what condition of structure?
Yuhanas Yuhanasstructure engineer - Jakarta, Indonesia
January 17, 2011
A. Sa.2.5 is expected for existing structure, while Sa.2 is for new installation.
Joseph Okoye- Ikoyi, Lagos, Nigeria
Q. Sir
Can we use silica sand in following Sa 2.5 & Sa 3? If not, which kind of sand do we use?
employee - Rahim Yar Khan, Pakistan
May 5, 2011
Is there a ± on anchor profile?
Q. I have an inspector concerned that the anchor profile is too aggressive and there may not be enough paint on the high points. The spec called for SSPC SSPC SP 10 Surface Profile 2-3 mils, we had an average of 4 after blasting. The paint application was a 3 stage: Prime Coat 3-5 (Zinc Epoxy), Intermediate Coat 6-10 (Epoxy), Top Coat 2-4 (Acrylic Polyurethane with a total DFT called out of 11-19 mils. We had average of 13-17 total. Is there a range on the anchor profile ± that keeps me in spec compliance?
Marty MossQA - Vienna, Ohio, USA
June 8, 2011
Q. Which term to follow regarding surface preparation of storage tanks, whether surface cleanliness or surface profile or both because both seems two different requirement of surface preparation for applying coating on metal surface.
A. Aziz- Karachi, Pakistan
August 21, 2011
A. It seems there is a whole book to be written on the blasting standard requirements, the differences between the required grades and surface profiles.
In short, our company approach the problem as follows:
The client needs to decide (or be advised depending on the application) what type of coating will be applied to the steel, this will decide the required blasting grade as specified by the coatings manufacturer (the norm seems to be SA2.5).The coatings manufacturer will also specify the required DFT (Dry Film Thickness) of the required coating to be applied.The DFT requirement is what needs to be looked at when one decides the roughness of a surface profile in microns.
- Alberton, Gauteng, South Africa
Q. Please advise me how to inspect sand blasting for steel structures like I beam, channel, plate.
1. What the pressure should I maintain to get the fine surface preparation.
2. What microns should be there after sand blasting.
quality control - Saudi Arabia
October 26, 2011
Q. I have a similar question to the one asked on October 26. For us we are being asked to prepare metal surfaces by Sandblasting to a SP 10 level finish. What does that entail and how do we inspect for this?
Carlos M [last name deleted for privacy by Editor]manufacturing - Stockton, California
October 28, 2011
Hi Carlos. SP 10 is a "near white metal" sandblasting spec. Some people, such as certified inspectors, spend their entire careers learning how best to inspect, so I can't pretend that how to inspect is easily answered in a forum :-)
But if you have a copy of SP-10, please try your best to phrase your question in terms of what information you feel it is not offering you about compliance. If you don't yet have a copy of SSPC SP 10 / NACE No. 2/SSPC-SP10 yet it's a joint product of SSPC (the Society for Protective Coatings) and NACE (originally National Association of Corrosion Engineers). You probably should download the 6-page spec before proceeding :-)
Luck and Regards,
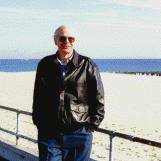
Ted Mooney, P.E.
Striving to live Aloha
finishing.com - Pine Beach, New Jersey
(You're on the 1st page of this topic) Next page >
Q, A, or Comment on THIS thread -or- Start a NEW Thread