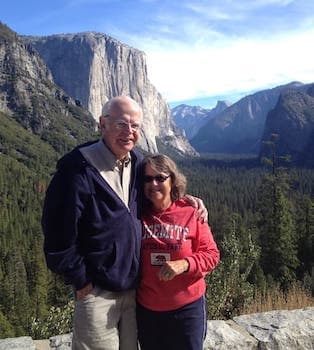
Curated with aloha by
Ted Mooney, P.E. RET
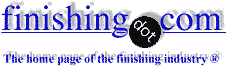
The authoritative public forum
for Metal Finishing 1989-2025
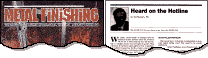
-----
Lacquer and zinc plating
Q. I want to lacquer some of our fasteners which have Blue Passivation and the minimum resistance should be 48 hours in Salt Spray Test. Kindly help me out about the percentage of lacquer to be used and an economic way to test it after lacquer. How can I do salt spray test at my workplace. An easy and economic way.
Thanks,
Tejinderauto fasteners - Rajpura, Punjab, India
2002
2002
A. It is not uncommon to lacquer the parts, Tejinder. For your non-demanding requirements I would be surprised if immersion in the simplest water soluble lacquer or wax wouldn't get you past this test. But your zinc plating plus chromating should easily pass this test without any lacquer coating, so you might concentrate on getting them right first.
You need an engineered salt spray cabinet to do an ISO or ASTM accelerated corrosion salt spray test. But if you want a simple test for internal use, you might do a search for "CAMRI testing". This is a repeatable accelerated corrosion test that can be done with very little investment, and has been used by very reputable organizations including the International Zinc Association. Good luck.
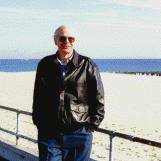
Ted Mooney, P.E.
Striving to live Aloha
finishing.com - Pine Beach, New Jersey
A. Salt spray is not an easy and inexpensive test. Obtain a copy of theASTM B117 specification, and you will see why. I suggest you find a few reliable testing companies and get a 2-3 quotes.

Tim Neveau
Rochester Hills, Michigan
2002
Q. Is it advisable to provide lacquer coating on Zinc plated & passivated parts for better corrosive resistance ?.
If yes , how lacquer coatings protects passivation/plating?
If No, What is the best method to protect passivation/Zinc plating from corrosion to enhance the life of the coating.
Please clarify.
- Coimbatore, India
2005
A. Hi, Mr. Senthilnathan. Lacquer of this type increases corrosion resistance the same way that paint would -- as barrier layer protection. For that reason it can be a good idea . . . if your customer agrees and understands. But it can also have a downside! If your customer relies on this finish for electrical conductivity, the lacquer will kill it; if he's planning to paint or powder coat the item, a lacquer or wax can destroy adhesion; if it's a threaded fastener, lacquer doesn't have the adhesion that plating offers (that's one reason fasteners are plated instead of painted).
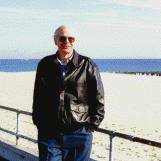
Ted Mooney, P.E.
Striving to live Aloha
finishing.com - Pine Beach, New Jersey
2005
Q. Is the zinc plating and lacquer coating acceptable for an equipment situation that is exposed to salt spray on an oil rig in the ocean? Basically, is it a good replacement for the corrosion preventative properties of Yellow Hexavalent chromate hardware?
More and more customers are requesting RoHS compliant hardware on our equipment. As a patch we are replacing all the yellow hexavalent chromate hardware with 304SST hardware. There are some components that we are not able to substitute and are getting permission, so far, to continue the use of hexavalent chromate for these special situations. Currently we requested an alternative to the Hexavalent chromate. We have asked our vender to suggest alternatives. One alternative they have suggested was to go the trivalent hexavalent chromate route, but another was to go the route of zinc plating and coating with layers of lacquer. They are performing 96 salt spray tests that have failed a couple times so far. Now they are trying different layer thicknesses to pass the test. I wonder even if they get it to pass the 96 hr salt spray test. Will it really work as well as the trivalent chromate in a working scratched thru assembly environment.
Evan Frazier- Florence, Kentucky
May 18, 2009
A. Hi, Evan. No, the lacquer is not a substitute for chromate conversion coating . . . it's a topcoat over it. Lacquer might not even reliably stick directly to zinc.
You can use a proprietary trivalent chromate and a topcoat as a substitute for yellow chromate, but I don't think either the substitute or the original will hold up long on an offshore oil rig. I think you need galvanizing, or a heavy (25 µm) alloy zinc plating, or stainless steel construction. There are special standards for oil rig equipment.
Regards,
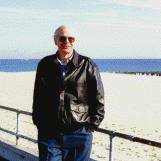
Ted Mooney, P.E.
Striving to live Aloha
finishing.com - Pine Beach, New Jersey
May 2009
Zinc plated and trivalent passivation with lacquer top coat
Q. We are doing Alkaline Zinc plating and trivalent passivation of small parts. We apply lacquer after passivation as top coat. In the Salt Spray testing a white layer appears. This goes away under running water leaving a stain. Is it white rust and rejectable? There is an opinion that this lacquer migration that appears as a white layer and not White rust of Zinc. Can any one clarify please?
Ravi NarayanPlater - Bangalore,Karnataka, India
December 25, 2016
A. Hi Ravi. First, can you tell us what spec you are plating to which allows for a lacquer coating? Whether the white discoloration is due to the lacquer emulsifying to opacity, or whether it's due to white rust, may be a moot question because you can't take a spec which doesn't mention lacquer, then lacquer coat the parts, then claim you met the spec if you achieve the required salt spray testing time :-)
Trivalent chromating is a fairly high technology operation compared to the old hexavalent chromating, and I think you should always plate to a spec, and always use the topcoat specified by the trivalent chromate supplier, rather than applying a lacquer on top of it. If you are lacquering without your customer's understanding and permission you could find yourself in a contract dispute. Good luck.
Regards,
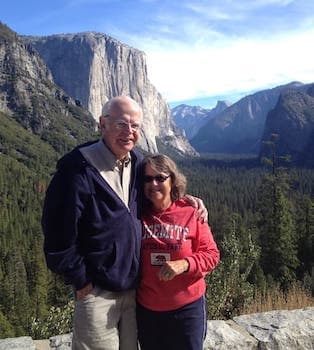
Ted Mooney, P.E. RET
Striving to live Aloha
finishing.com - Pine Beach, New Jersey
December 2016
Q. Thank you Mr.Ted. The lacquer coat is approved by the customer.
Coating Thickness: 8 microns minimum.
The salt spray life spec is 96 hrs minimum for White Rust and 240 hours minimum Red rust. Now please tell about lacquer migration which we feel might happen and be construed as white rust.
- Bangalore, Karnataka, India
December 26, 2016
A. Hi again Ravi. I ducked your question the first time, and will have to duck it again because I don't know how a reader could know whether your verbally described discoloration is due to white rust or emulsification of a lacquer coating.
But I also don't know how we can say in the absence of a spec that 96 hours to white rust is satisfactory performance, and discoloration of a lacquer coating is to be ignored. A wiser man than me once told me: "If you have to talk yourself into the parts being good, they're not".
Surely the parts are supposed to be capable of withstanding 96 hours to white rust without any lacquer coating, so why not just test unlacquered parts and you'll know whether they get white rust. I'm betting that they will and the investigation into whether the whiteness is white rust or lacquer discoloration will become moot; but if unlacquered parts do not fail, you'll know that the lacquer is what is discoloring, and you'll be able to investigate whether a better lacquer will maintain clearness.
Regards,
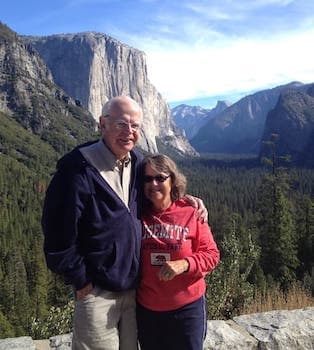
Ted Mooney, P.E. RET
Striving to live Aloha
finishing.com - Pine Beach, New Jersey
December 2016
![]() |
Q. How to do lacquer on brass and zinc? If we do lacquer on brass and zinc, will there be a difference in color? If yes then what is the solution for this type of thing. kanhaiya kumaracquaviva india pvt ltd. - noida, uttar pardesh, India July 10, 2019 A. Hi kanhaiya. The discussion on this page so far has referred to very thin lacquers used on zinc plated articles to hopefully add a small additional amount of salt spray resistance. But 'lacquer' is a very general term, and lacquer on brass and zinc bathroom fixtures will certainly give them a different appearance than unlacquered. Unlacquered brass will very quickly discolor and turn brownish in a moisture-laden environment; and unlacquered zinc will quickly pit and develop white rust. Please give us a fuller description of what you are trying to do in getting lacquer finishes to look like raw metal. Thanks! But maybe you are complaining of runs and drips and various thicknesses of lacquer? In that case, I can tell you that the way to avoid them is multiple thin coats -- some premium brass chandelier manufacturers do 6, 8, or more coats. And there are also a number of finishes which people may call "lacquer" without necessarily being typical brass lacquer formulations. Electrophoretic lacquer (e-coating) is a possibility, as are radiation hardened formulations, and other types of clear coats. Good luck. Regards, ![]() Ted Mooney, P.E. RET Striving to live Aloha finishing.com - Pine Beach, New Jersey October 2019 |
Q, A, or Comment on THIS thread -or- Start a NEW Thread