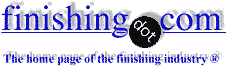
-----
Galvanizing: Zinc Bath Management
2002
Q. I am working for a galvanizing company engaged in zinc coating on cold rolled steel coils in a continuous galvanizing line.
The coil is coated in the zinc bath.
We have been considering use of zinc with the copper present as an impurity to the extent of 0.06% to 0.08%.
I would like to know what is the effect of copper in the zinc used for galvanizing on
(a) - the quality of the finished (galvanized)sheet/ coils and
(b) - on the life of the galvanizing equipments such as melting pot support rolls , etc.
(c) - dross generation during the galvanizing process shall be grateful if anyone has experience on this type of zinc (with copper) and can share it. Or if someone can refer to any literature on the subject.
(d) Also let me know the details of reducing the dross generation during galvanizing process.
Priy Vrat Shringi- Mumbai, India
by Kuklik & Kudlacek
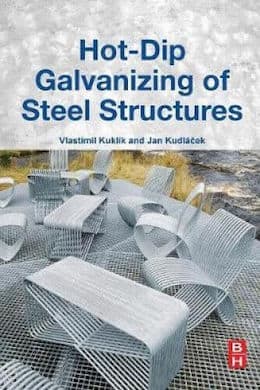
on eBay or Amazon
or AbeBooks
(affil link)
A. Hi Shringi, how are you?.
The questions you asked are answered as follows - Cu in a bath is considered as a impurity. The impact will be reduction in corrosion resistance of coating. Normally in a Galvanizing we use 99.995 % pure zinc and some quantity of Al for good adhesion. Zinc gives Galvanic protection to steel which is also called sacrificial type of coating. The dross generation in bath is mainly due to Fe, i.e. iron fines from strip or from iron pot.
To reduce dross you can take following measures -
1. Wipe Zinc at min. possible air.
2. Use of SS 316L POT.
3. Minimum line stoppages.
4. Bath management and Zinc charging practices needs to be improved (Exp. Al alloy charging directly in bath will lead excess Al2O3 on surface). The drosses are top and bottom where Al% is higher and low respectively. As solubility of Fe in Zinc at 460 deg.C is 0.03% excess Fe from strip or from pot came in to dross. You can arrange brain storming session at your works to improve operational practices and to take corrective measures to reduce dross. It was said that if Al % in bath is more than 0.2% there is no bottom dross formation possible as Al takes Fe oxides at top and we can remove top dross.
- Latur, India
Q. Dear Sir
We have a ceramic zinc pot 200 ton weight and simple galvanizing production with 0.2% Al now the problem is incorrect distribution of Al in coating; it has more Al in coating at surface. what I know the problem is because of bad charging. I want you to please give me a charging instruction for zinc pot ingot charging.
thank you
best regards
technical engineer - Iran
December 14, 2010
!! Sirs:
The three previous posts are quite disturbing. I do not recommend zinc for hot dip galvanizing that has more than 0.05% copper because it attacks the iron kettle and predictably accelerates corrosion in the zinc coating on the product.
The use of 316 L stainless steel for a kettle is quite incredible. Having a nickel component means the molten zinc will attack the 316L without showing much damage but indeed suffering much damage. 316L is quite likely to look good but predictable will have sudden failure. For example galvanizers have used stainless for hooks and they look fine and suddenly they break.
I find it quite disturbing that the operator of a sheet line does not know how to uniformly attain aluminum/zinc in the kettle. He does not even mention his starting source for the aluminum (e.g. pure aluminum or an aluminum/zinc alloy or its composition).
Regards,
Galvanizing Consultant - Hot Springs, South Dakota, USA
December 16, 2010
Copper from unknown source is rising in galvanizing kettle
November 5, 2013Q. Hello folks,
I work in a company that galvanizes angle steel (A36) and sheets (A572) for electrical power transmission towers. We have two lines (100 tons of zinc in each) operating.
We're facing a situation that we don't know how to handle with it. Since I've started working here, I noticed that the copper in one of our continuous lines is continuously increasing. In February of 2012 the level of copper in this kettle was 0,0245% and it reached its maximum in October of 2012 0,124%. This value kept constant until July of 2013, when the kettle leaked.
When the line started operating, the copper level was 0,0027%, but is growing again, and it's already 0,0123%, about 6 times greater in only 4 months.
The question is, where is this copper coming from? Is it the kettle being eroded? Or might it be from the steel? We galvanize only A36 and A572.
-The kettle is made from steel plate called USI-GV (COS AR COR 350) and the chemical composition is: C 0,04% Si 0,01% Mn 0,24% P 0,008% S 0,013% Al 0,052% Cu 0,01% Nb 0,001% V 0,001% Ti 0,001% Cr 0,02% Ni 0,02% Mo 0,00% Sn 0,001% N 0,0039% As 0,004% B 0,0003% Ca 0,0003% Sb 0,00% |
-The zinc composition in the kettle is: Zn 98,7597% Fe 0,0388% Ni 0,00123% Al 0,0010% Cd 0,0004% Cu 0,0123% Pb 1,1867% Sn 0,00067% |
-We use a zinc alloy called ZN-4E with 0,05% of Al, the composition is: Zn 99,99%min/100%max Al 0,005%min/0,009%max Cd 0,000%min/0,003%max Cu 0,000%min/0,001%max Fe 0,000%min/0,002%max Pb 0,000%min/0,004%max Sn 0,000%min/0,001%max |
I hope all this information will be enough for us to find a cause to this contamination of copper.
Few last questions, what are the disadvantages of having a high level of copper in the zinc? What is the maximum? Now that the level is high, how can I take this level to below the maximum?
Thank you for the help!
Process Engineer - Brazil
November 13, 2013
A. Daniel,
The copper is likely coming from the steel. I never worry about copper until it is above 0.05%.
Regards,
Galvanizing Consultant - Hot Springs, South Dakota, USA

Q, A, or Comment on THIS thread -or- Start a NEW Thread